上一次,小捷为大家介绍了燃料电池系统的总体诞生过程。那么在燃料电池的系统的设计过程当中,会遇到哪些问题?又该怎么解决呢?
今天,就让小捷给大家介绍燃料电池系统在结构设计上会遇到的问题和解决方案。
对于燃料电池系统的结构设计而言,安全性和可靠性肯定是重中之重。那什么样的产品可以认为是安全可靠的呢?
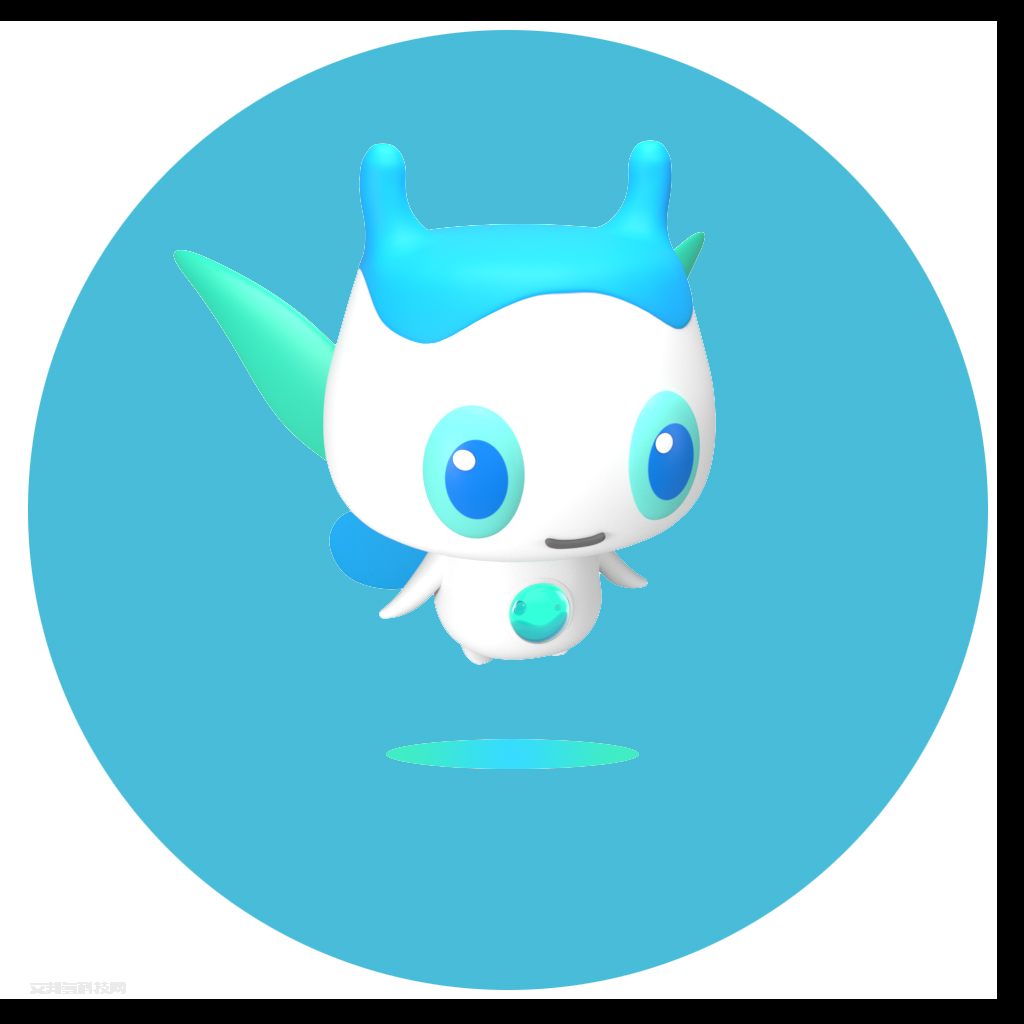
简单来说,就是燃料电池系统在规定的载荷等条件下,经历规定的时间和里程等,最终保持可靠性,就可以认为这个燃料电池的结构是可靠的。
那么该如何评估燃料电池系统的结构可靠性呢?有没有具体的例子?
我们是采用了两大工具:仿真与试验,并从五个维度:模态、振动传递、振动耐久、静强度、冲击强度来评估燃料电池的可靠性。
以PROME P3X系统为例,在设计初期,主要通过仿真进行分析。设置完善的工况条件,对系统进行多个维度的全面评估。
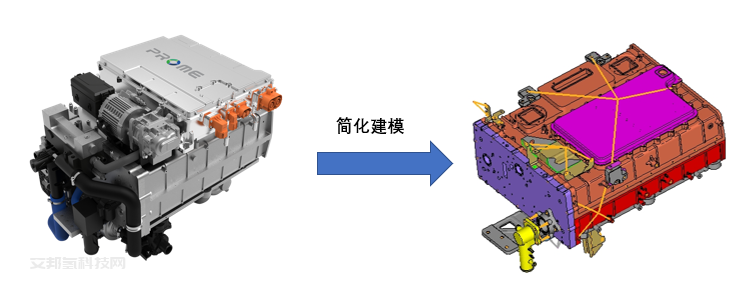
我们可以通过计算系统的模态,得到系统本身的振动特点。包括系统整体各个转动件的主要振型是怎样的?转动件是以轴向还是径向的运动为主?转动件的工作点与支架是否共振?转动件相互间是否有共振?等等。
对系统本身的振动特点分析,有助于在项目初期发现结构的薄弱点,找出主要的改进方向。
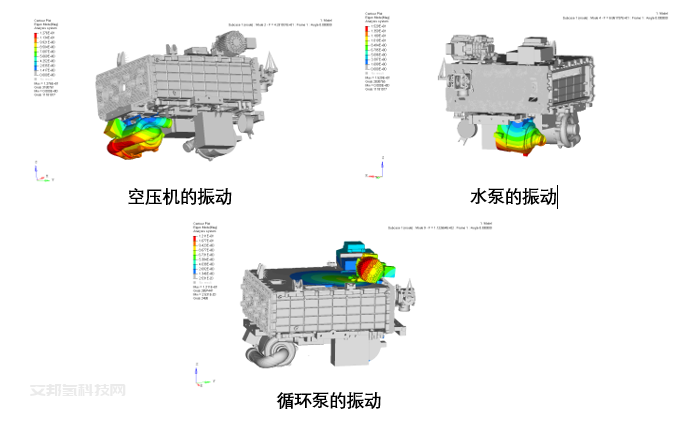
系统振动模态图
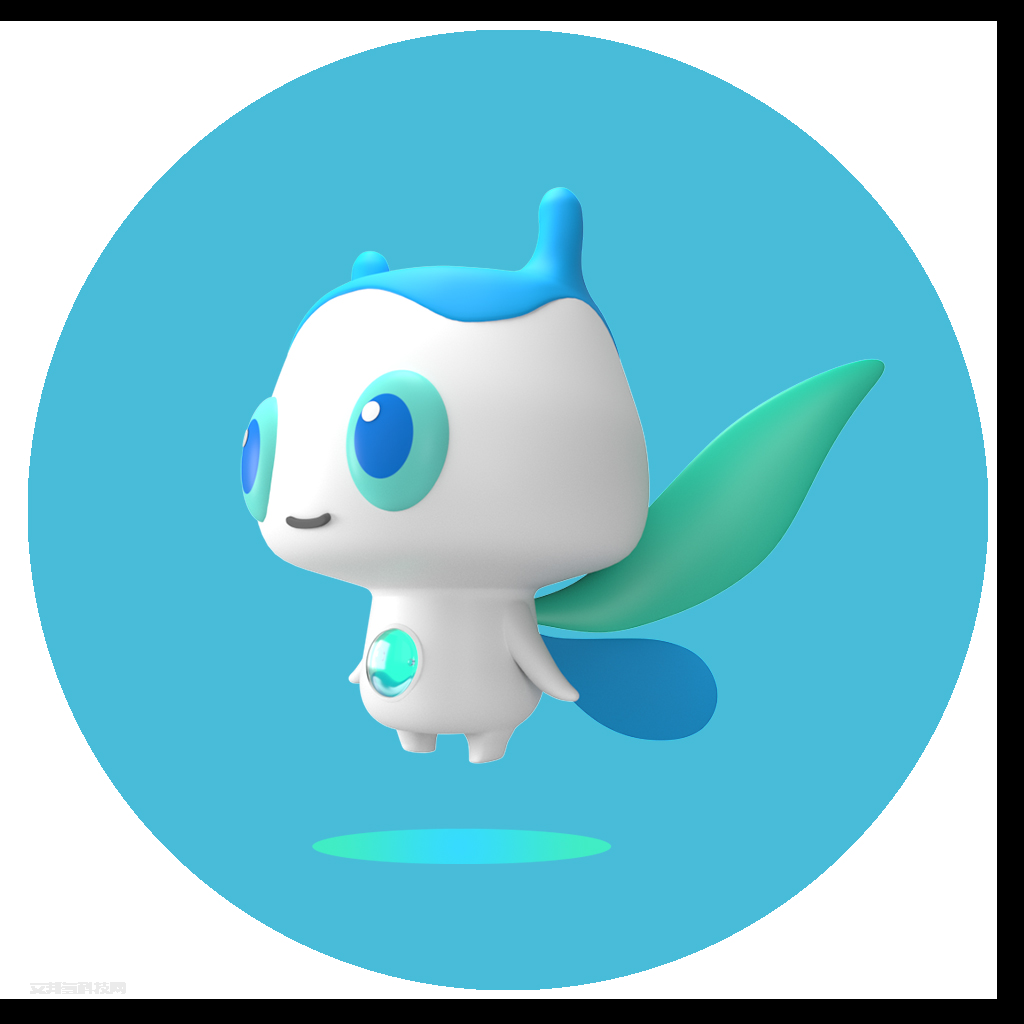
分析自身的振动特点之后,是不是还需要分析其他的因素?比如路面不平而引起的振动是不是也有影响?
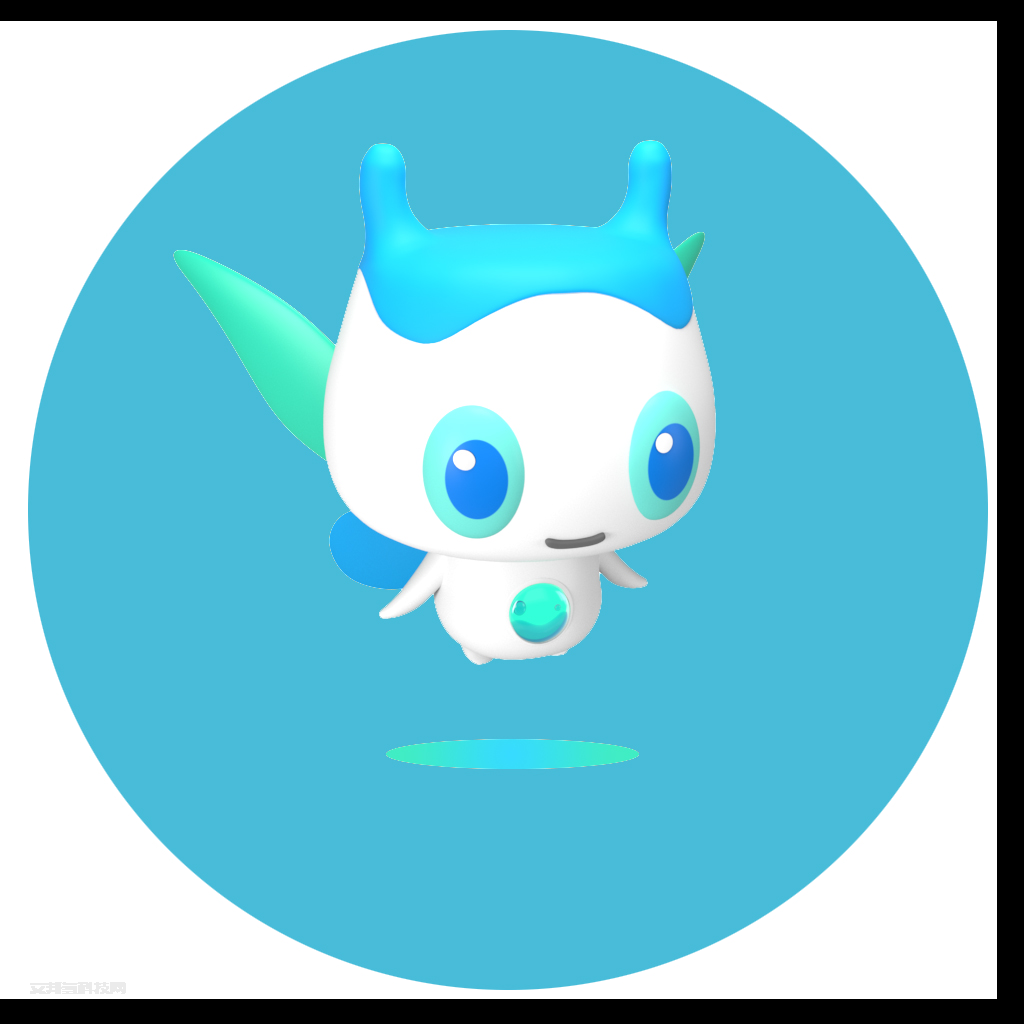
没错,除了评估本身的结构特点,系统的随机和冲击分析也是重要的分析项。分析工况条件尽可能涵盖实际的应用情况,这样才能更好的发现结构方面的应用问题。
具体来说,随机振动分析是评估燃料电池系统的振动耐久性能,一般通过PSD载荷谱作为分析条件,反映的是车辆在长时间运行下系统受到的一个统计载荷,评价标准是要求系统在x、y、z方向的振动激励下不发生断裂损伤。
而冲击振动分析是评估燃料电池系统在大载荷下的结构强度,一般对应过坑、撞击等加速度较大的实际状态,同样要求x、y、z方向载荷下均不发生断裂损伤。
振动耐久分析的PSD载荷
仿真测试完没有问题就可以了吗?
当然不是,完成仿真评估后,系统的数模经过锁定到装配,还需要通过相关的测试,最终完成结构可靠性的评估与检验。
只有经过多轮静态特性、动态性能、疲劳耐久等的仿真分析,以及试验的评估,燃料电池系统在各个维度上都达到目标要求,才能确保燃料电池系统能够在车辆行驶过程中可靠运行。
振动与冲击台架试验
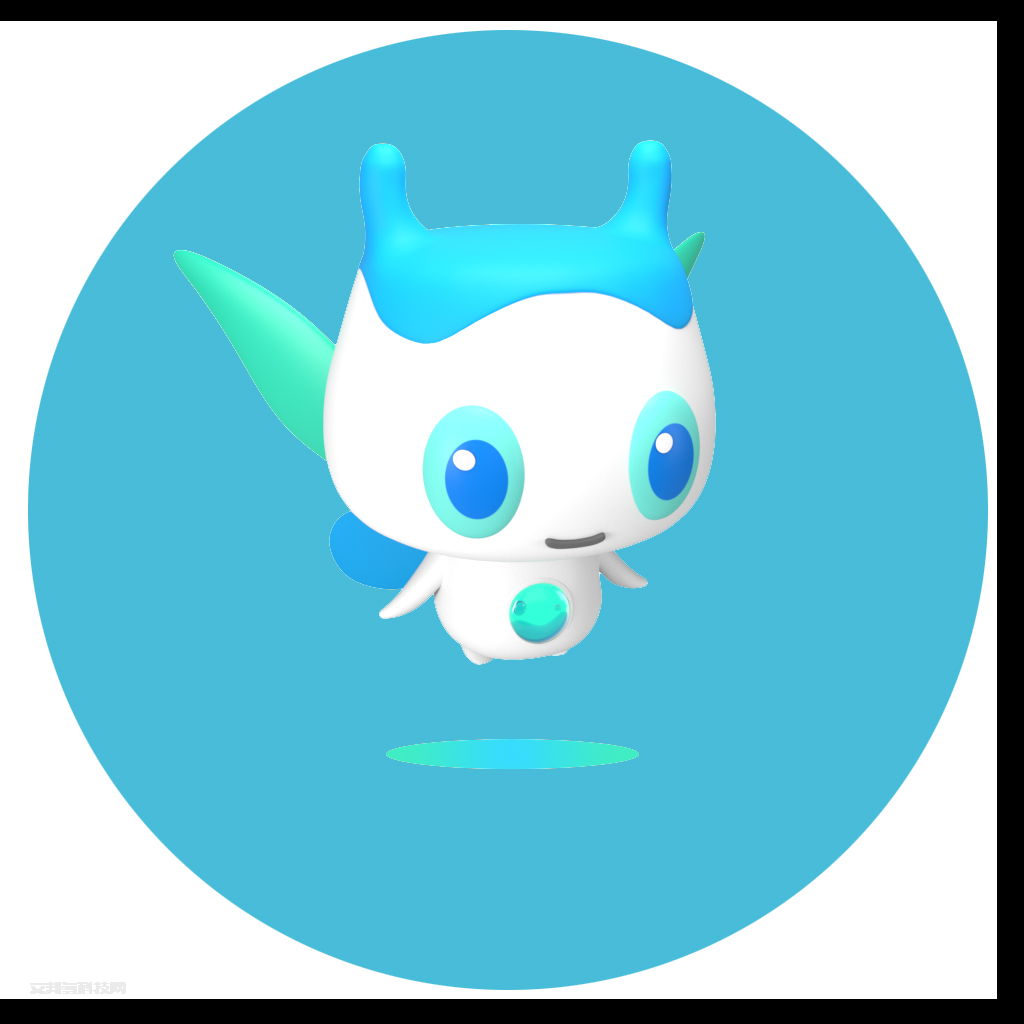
经过这么多工序的结构就是不是就完美了?
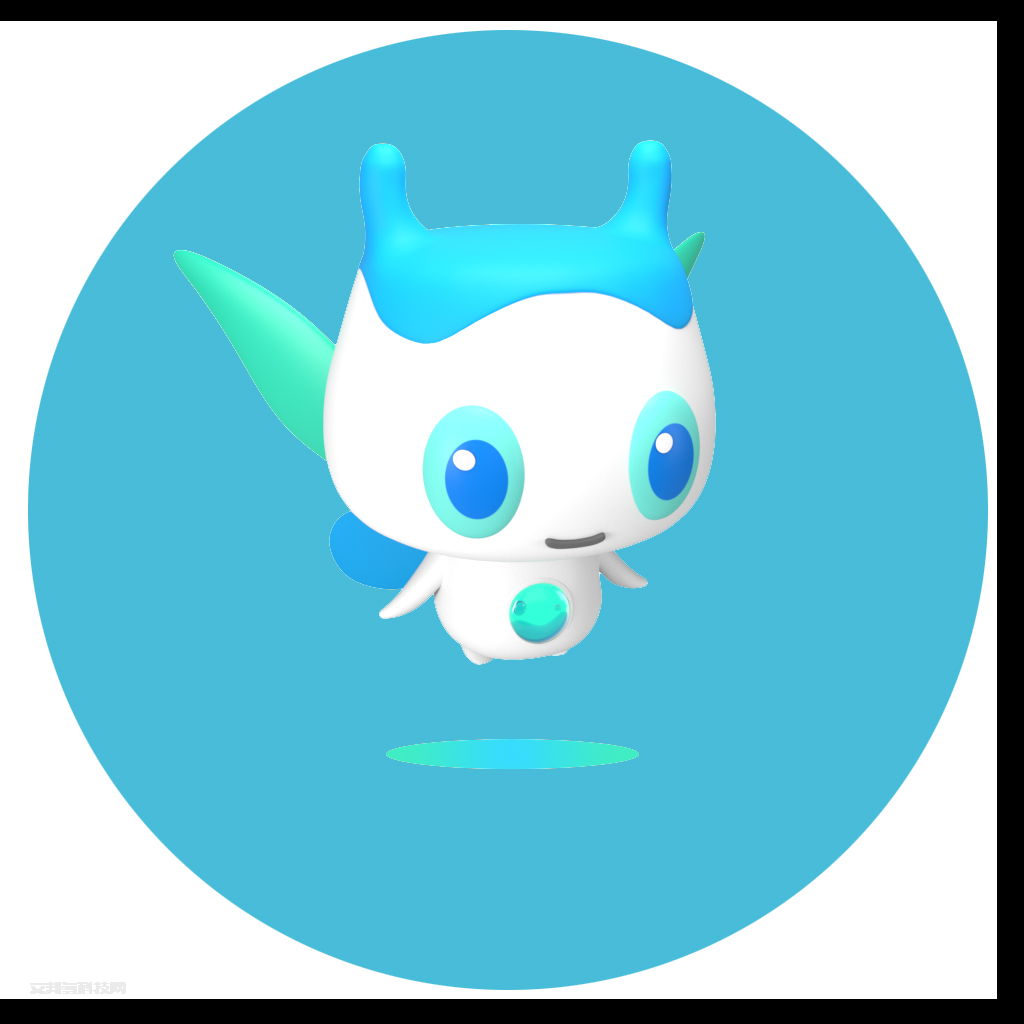
在其他方面仍然有提升的空间。有时,初期的结构设计会比较“稳重”,这是为了能够充分的满足结构的静态、动态特性以及耐久、抗冲击的要求。但过于“稳”,“重”的缺点也会随之而来。在保证系统的结构耐久稳定性的基础上,下一步的工作就是尽可能的降低结构重量,保持系统轻便,以提升燃料电池系统质量功率密度。
那怎么样才能使得系统变得轻便?
首先可以采用更稳定的结构设计,而不是厚重的结构。例如,避免采用过多厚重的方钢作为主要支撑,在燃料电池系统中优化悬置的位置,使整体本身的刚度提高。
此外,初版结构设计锁定后,难以进行大的变动,可以考虑在原设计的基础上进行拓扑优化,以每个结构单元的使用率为优化对象,根据结构单元的使用率,对结构形式进行优化改进,达到系统减重的目的。
P3X集成框架的单元密度优化
在燃料电池系统结构性能满足要求的前提下,通过结构拓扑优化等仿真手段,采用高度一体化集成策略,基于多结构耦合设计理念,将系统布置空间及系统质量做到极致。
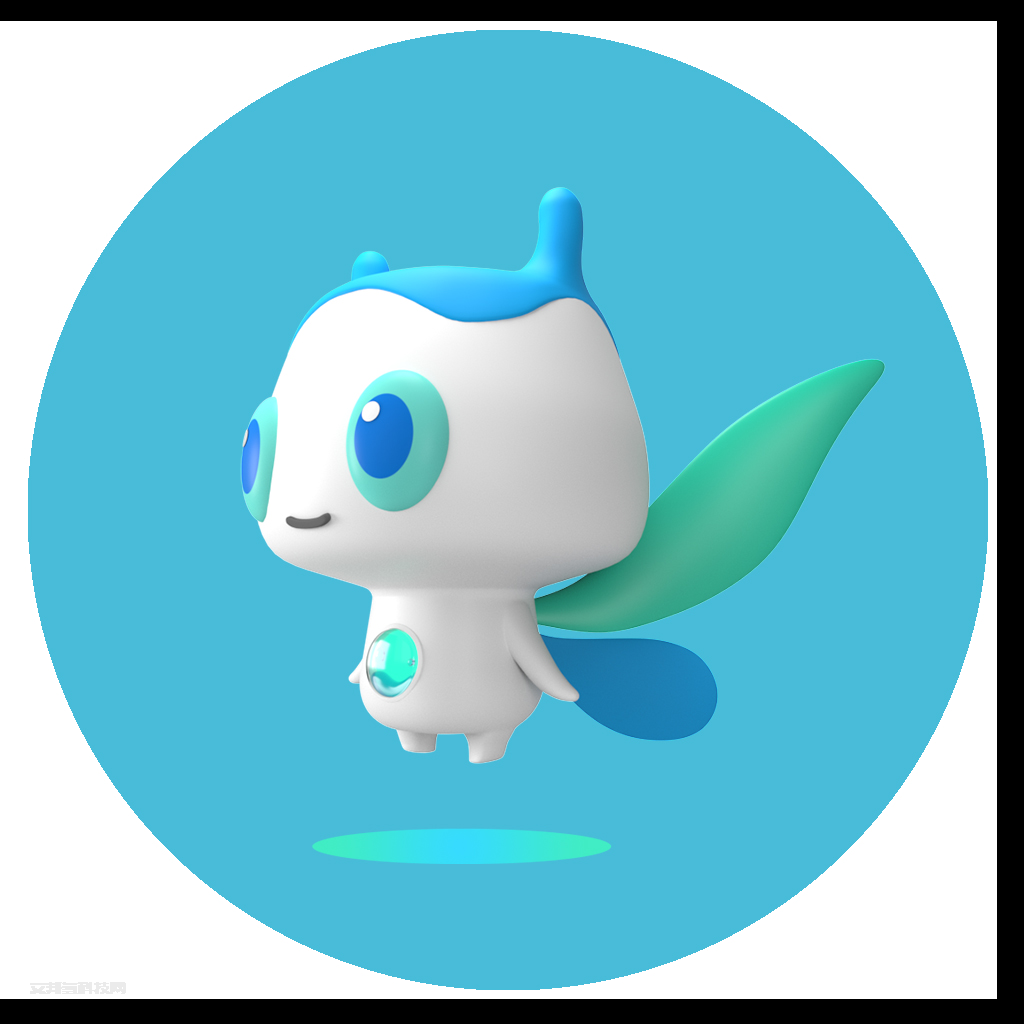
怎么样,大家对燃料电池的结构设计有一定了解了吗?下一期小捷会带大家了解,燃料电池系统的NVH性能(乘员感受到的噪声、振动及相关的声振粗糙度)是如何优化的~
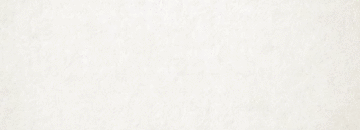
原文始发于微信公众号(捷氢科技):我们很稳,但不重 ——小捷带你走进燃料电池系统的结构设计
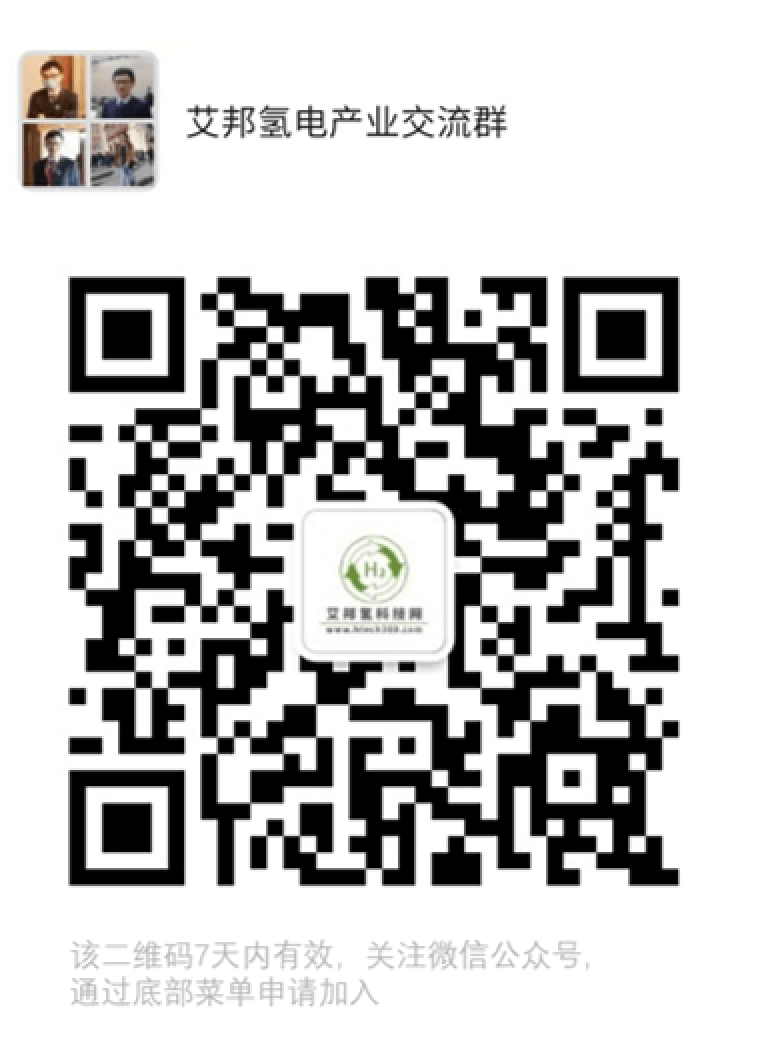