膜电极(MEA)是质子交换膜燃料电池(PEMFC)中的“芯片”,主要由质子交换膜、催化层和气体扩散层组成。
MEA的性能主要受三个方面的影响:活化极化、欧姆极化和传质极化引起的电压降(如图1所示)。活化极化由电极中催化剂表面的反应速度过慢导致,影响主要表现在低电密区;欧姆极化是电子通过电极材料及各种连接件以及离子通过电解质膜的阻抗引起,这种电压降与电流密度成线性比例;传质极化由电极中发生电化学反应所需反应物浓度不足引起,影响主要表现在高电密区。其中传质极化的大小决定了MEA的最大输出功率,它是催化层和气体扩散层相互匹配共同影响的结果,如催化层的微孔结构、催化剂/树脂界面结构,气体扩散层的内部孔结构、亲疏水孔的比例、导热等。
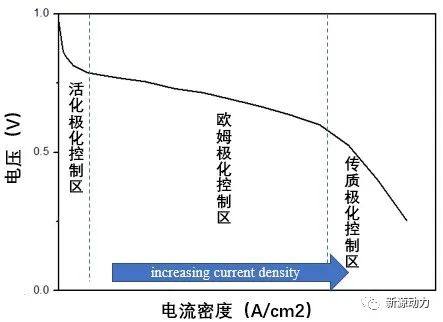
高性能、低成本、长寿命MEA的开发首先就是克服上述三种极化。新源动力膜电极研发团队在长期的MEA产品正向开发工作中,建立了相应的分析测试方法,对MEA开展极化性能研究及失效分析,极限电流法就是其中之一。本文向大家介绍通过极限电流法对MEA传质性能及水管理能力的分析。
燃料电池运行过程中,氧气从流场穿过气体扩散层到达催化层,再透过催化层的孔隙和包裹在催化剂颗粒表面的树脂到达催化剂颗粒表面发生反应。当氧气从流场到催化剂表面的扩散速率等于反应过程的消耗速率时,其产生的电流称之为极限电流,用极限电流值可以计算出氧气的传质阻力,如公式(1)所示:
公式(1)
公式中Rtotal为单电池总的传质阻力,CO2,FF为流道中氧气的浓度,ilim为实验测得的极限电流值。极限电流法分析MEA的传质性能,体现在三个方面:
一、MEA内部干湿状态变化过程的分析
在特定工况下利用不同氧气浓度的O2-N2混合气测试单电池的极限电流ilim,根据公式(1)计算出总传质阻力Rtotal,做Rtotal-ilim的关系图,得到单电池内部由低润湿到水热平衡区再到水淹区的过程中电流密度转折点的位置,以此分析MEA内部干湿状态的变化特性。如图2所示为两种不同工艺制备的MEA组装的单电池测试结果,MEA-2与MEA-1相比可以看出MEA-2发生水淹的电流密度点大于MEA-1,说明MEA-2在水管理方面的性能优于MEA-1。
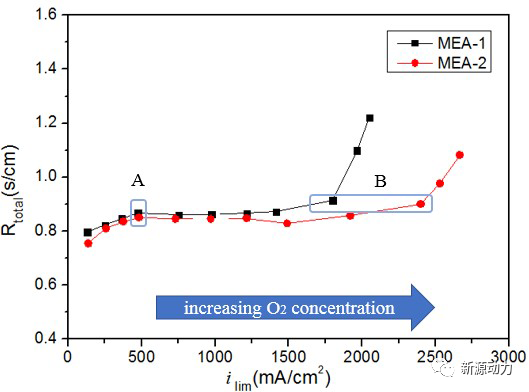
二、气体扩散层、催化层传质阻力的分离
氧气在扩散层和流道中主要发生分子扩散过程,分子扩散阻力与压强成正比。用不同压力的低氧浓度的O2-N2混合气进行极限电流测试,计算出总的传质阻力Rtotal,根据气体在流道中分子的扩散特性以及测试所用夹具的流道尺寸计算出流道的传质阻力Rch,总的传质阻力减去Rch即为扩散层传质阻力RGDL和催化层传质阻力RCL之和(记为RT)。通过RT-P线性关系计算出扩散层的传质阻力RGDL,剩余部分的阻力即为催化层的传质阻力RCL。如图3所示,为特定工况下扩散层传质阻力和催化层传质阻力分离的结果。
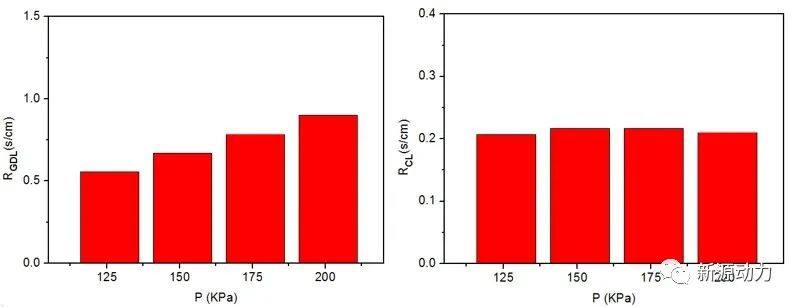
图3:气体扩散层传质阻力和催化层传质阻力
三、催化层中努森扩散阻力和溶解扩散阻力的分离
努森扩散指氧气在催化层孔隙中的扩散,溶解扩散指氧气在包裹在催化剂颗粒表面的树脂中的溶解扩散。努森扩散与催化层的孔径大小和传输距离相关,在保持催化层孔径分布不变、Pt载量不变的前提下,通过增大阴极催化层厚度的方式增加氧气的传输路径可增大催化层的努森扩散阻力Rkun,Rkun与阴极催化层的厚度Rh成正比。因此我们通过在基础催化层的表面涂覆碳粉层增加整个阴极催化层的厚度,对具有不同厚度的阴极催化层的MEA进行极限电流测试分离出RCL,得到催化层传质阻力与阴极催化层厚度的关系RCL-hCL,如图4所示。通过RCL-hCL线性关系中的比例系数计算出催化层的努森扩散阻力Rkun。剩余部分的阻力即为催化层的溶解扩散阻力Rion,如图5所示。
图4:催化层传质阻力与阴极催化层厚度的关系
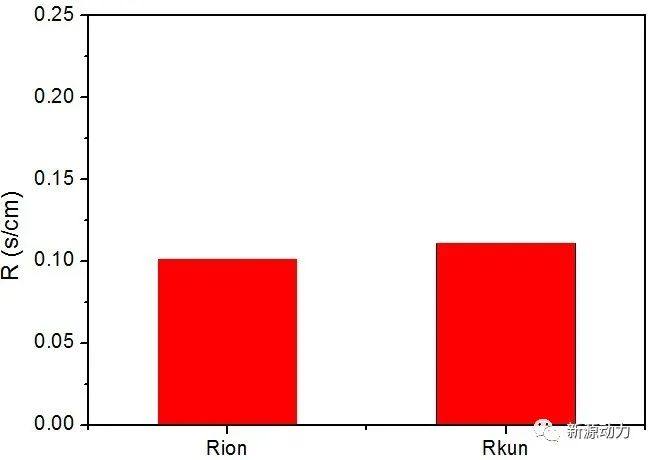
原文始发于微信公众号(新源动力):技术专题 第二期 | 膜电极性能及传质能力分析方法之【极限电流法】
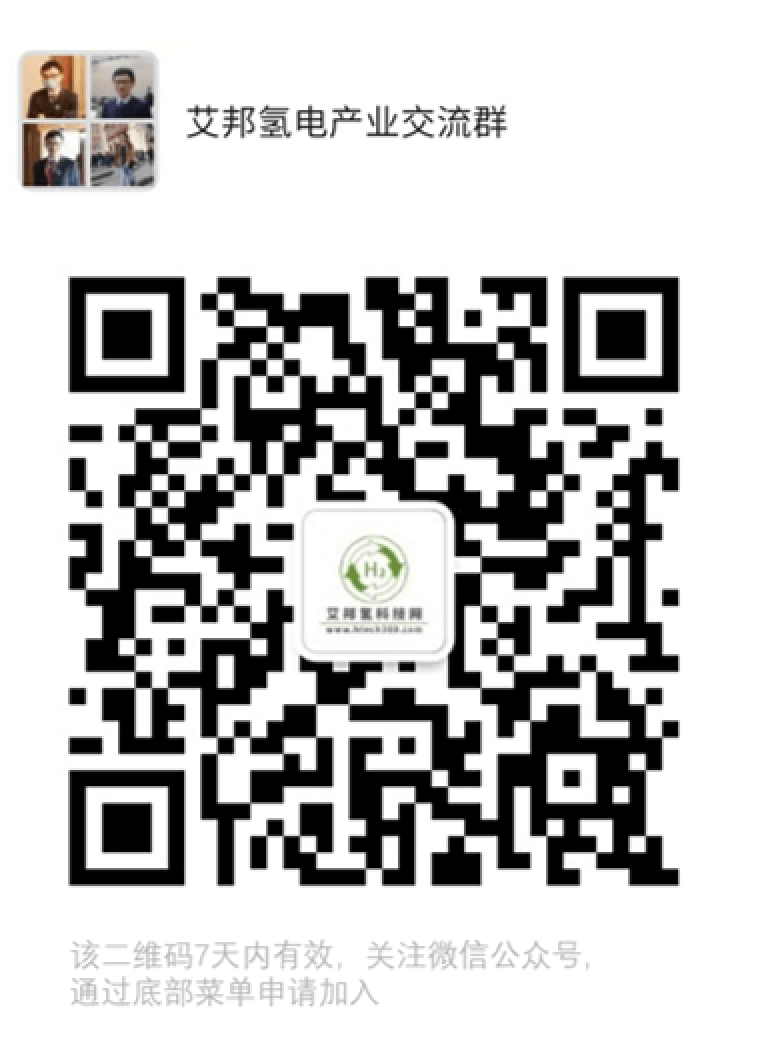