在甲烷裂解制氢过程中,反应器的选择与优化是关键因素之一。不同的反应器类型在反应效率、催化剂寿命以及产物纯度等方面表现出显著差异。
固定床反应器是最早被采用的反应器类型之一。其基本原理是将催化剂水平放置在反应器内的载片上,通过控制较小的表观气速来实现反应。在反应过程中,催化剂与生成的碳纳米管保持相对静止状态,而氢气产品则可以自然与固相分离,出反应器后进行收集。然而,由于碳纳米管的不断沉积,固相体积逐渐增大,导致床层局部空隙率变小,进而引发反应器堵塞现象。一方面,压降的增加使得甲烷进料受阻;另一方面,催化剂被大量碳包裹后会逐渐失活,导致氢气收率逐渐下降。
流化床反应器在甲烷裂解中具有独特的优势。通过较高的气速,可以将炭颗粒与催化剂颗粒悬浮起来,从而满足固相碳产品体积增长的需要。常用的催化剂包括活化碳或其他金属负载型催化剂。氢气产品在经过气固分离装置(如旋风分离器或过滤器)后进行收集。然而,由于纳米颗粒(包括催化剂与纳米碳产品)的高比表面积,易团聚,很难均匀流化,因此流化床技术中的难点在于控制催化剂单元与生成的碳纳米管产品的结构。通过催化剂的结构设计,可以使碳纳米材料在催化剂上生长时,形成体积较大、空隙率高、密度小的二次聚团,从而实现氢气与碳纳米管的同时大批量制备。
甲烷裂解过程受热力学特性制约,存在催化剂在低温下甲烷转化率低、氢气产率低的低效问题,以及在高温下瞬间转化率虽高但会迅速积炭失活的矛盾。这种温度依赖特性在等温的流化床或固定床反应器中很难解决,而多段变温流化床反应器则提供了一种有效的解决方案。例如,将流化床下段设为低温段(700℃),上段设为高温段(850℃)。所通入的气流将催化剂悬浮,由下段带入上段。在高温下,催化剂可快速裂解甲烷而生成碳;当所生成的炭块大于催化剂所能迁移的碳(接近于催化剂被碳包覆失活的状态)时,在上段(高温)中的催化剂由于重力作用自然下落到下段。而在下段由于温度低,催化剂基本不裂解甲烷。上下段的温度差恰好构成碳在催化剂体相内向外扩散及析出的推动力,使得碳进行有序迁移生成碳纳米管,而不是无序堆积将催化剂包覆。催化剂在碳析出后表面更新,活性恢复,然后再随着气流到达上段(高温),进行下一轮的甲烷裂解反应。这样利用多段流化床的变温操作特性,及反应器内固体流动的特性,可有效控制氢气与碳纳米管生成过程。 图:两段变温流化床设备示意图
下表展示了不同反应器在甲烷裂解过程中的反应效果对比。从表中可以看出,单段流化床(700℃,恒温)的甲烷转化率为30%,催化剂寿命约为60小时,氢气产率为26.6g/g催化剂,碳纳米管纯度约为98%。而单段流化床(850℃,恒温)的甲烷转化率高达85%,但催化剂寿命极短,仅为10秒,氢气产率极低,小于1.3g/g催化剂,碳纳米管纯度为75%。相比之下,两段变温流化床(上段850℃,下段700℃)提供了单段流化床恒定高温与恒定低温下的折中转化率,甲烷转化率为45%,催化剂寿命延长至约80小时,氢气产率大于40g/g催化剂,碳纳米管纯度高达99.2%。这表明两段变温流化床在总体效果上显著提高了氢气产率与碳纳米管的纯度。
在流化床反应器放大过程中,可能会遇到一些问题。例如,当甲烷在气体进口的局部浓度过高时,接触到高活性的催化剂,反应剧烈,会导致局部温度大幅度下降,使催化剂的结构状态发生变化。为了解决这一问题,可以采用间隔进料与连续少量进料的反应器技术,以降低局部甲烷浓度,进而控制温度,获得较好的控制效果.此外,在甲烷转化制备氢气时,整体温度过高会导致纳米金属催化剂在氢气气氛下还原过快,从而引起晶粒长大,活性降低。下行床与湍动流化床相结合的甲烷制氢反应器技术则提供了一种有效的解决方案。在下行床中,催化剂与甲烷的接触时间段,甲烷转化率较低,只能部分裂解生成氢气。而生长的低密度碳纳米管在催化剂表面上起到空间占位作用,客观上抑制了金属晶粒在面临高温反应环境的快速还原。在后面串联的流化床反应器中,催化剂与甲烷的接触时间较长,催化剂的活性可以得到充分利用,从而最大限度地提高基于催化剂质量的氢气产率。
图:下行床与湍动床耦合反应设备
除了上述几种常见的催化路线外,还可以将甲烷通过高温等离子体反应器进行裂解,得到氢或其他烃类以及碳材料。然而,本文将不再对这一路线进行详细赘述。 综上所述,不同的反应器类型在甲烷裂解制氢过程中具有各自的优势与局限性。通过合理选择与优化反应器类型,可以有效提高甲烷转化率、催化剂寿命以及氢气与碳纳米管的产率与纯度,从而为甲烷裂解制氢技术的发展提供有力支持。
原文始发于微信公众号(吉冠):甲烷裂解制氢技术中的反应器选择与优化
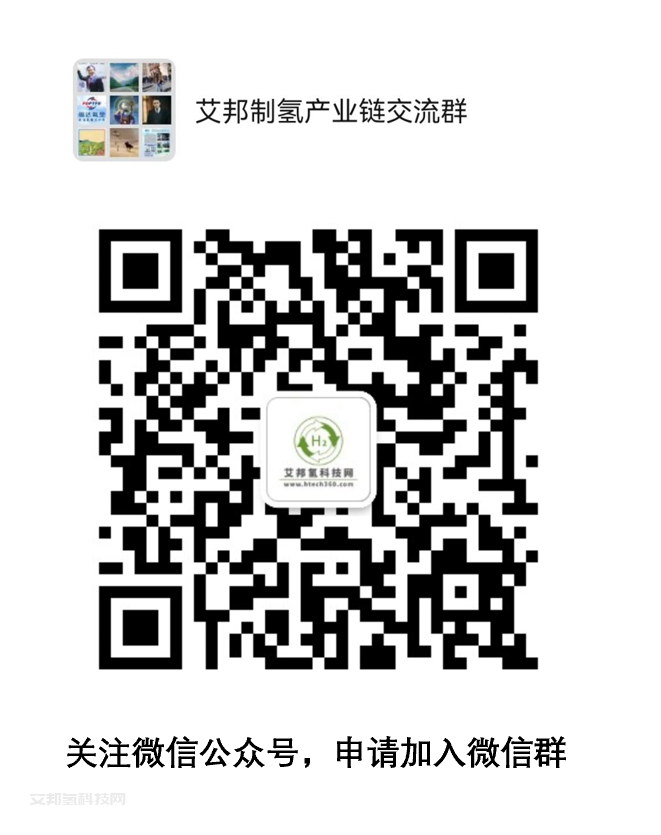