Ⅲ型瓶,又叫金属内胆纤维全缠绕气瓶,是一种金属与非金属材料相复合的高压容器,其结构为金属内衬外缠绕多种纤维固化后形成增强结构。
一、铝内胆要求
Ⅲ型瓶的金属内衬多采用铝合金,典型牌号如6061。根据美国DOT-CFFC标准,内衬材料主要有如下规定:
-
必须为无缝柱体,铝合金6061制造,回火条件T6 ;
-
可以由冷挤压或热挤压和冷拉制成,也可以由挤压管道和冲模的或者旋转的封头制成;
-
测试前,所有的铝合金6061柱体必须进行固溶热处理和老化热处理,且必须用统一性能的材料制造内衬;
-
内衬外表面必须防止不同的材料(铝和碳纤维)接触导致的电化学腐蚀。
二、铝内胆成型工艺
Ⅲ型瓶铝内胆的主流成型工艺是铝管强旋,其流程为:
-
固定毛坯 - 将短厚的铝筒毛坯套在旋压机的模具上,并将其固定。
-
旋压成形 - 筒体随机床主轴转动,通过旋轮或赶棒从端头开始对筒体坯料进行挤压。
-
塑性变形 - 坯料逐点连续发生塑性变形,导致毛坯壁厚减薄,内径基本保持不变,同时轴向延伸,最终形成符合壁厚及直径尺寸要求的圆筒。
强力旋压工艺的优点:
1. 材料强度与硬度的提升
通过强力旋压处理,材料的强度和硬度相比母材可以提高约35%至45%。这种显著的性能提升使得在航空航天领域,设计者能够有效减小零件的壁厚和重量,同时疲劳性能也得到显著增强。
2. 材料保护与性能优化
强力旋压技术通过对厚壁毛坯施加高压力,实现逐点减薄变形,保护了材料的金属纤维流向。这种整体成形技术生产的零件没有焊缝,从而显著提升了零件的整体性能和疲劳寿命。
3. 成本效益与生产效率
强力旋压的无切削加工和简易成形模具显著降低了生产成本并缩短了制造周期。在一次成形过程中,毛坯可以减薄60%甚至更多,这种高减薄率有效地揭示了母材中的冶金缺陷。
4. 精度与尺寸公差控制
使用强力旋压技术能够生产加工超宽板材。该技术确保了零件的尺寸公差和形位公差极小,其精度甚至超过传统的机械加工方法,满足高精度制造需求。
另外,该种工艺相对简单,生产效率需要进一步提升。
来源:艾邦氢科技网综合整理
原文始发于微信公众号(艾邦氢科技网):III型储氢瓶铝合金内胆生产工艺解析
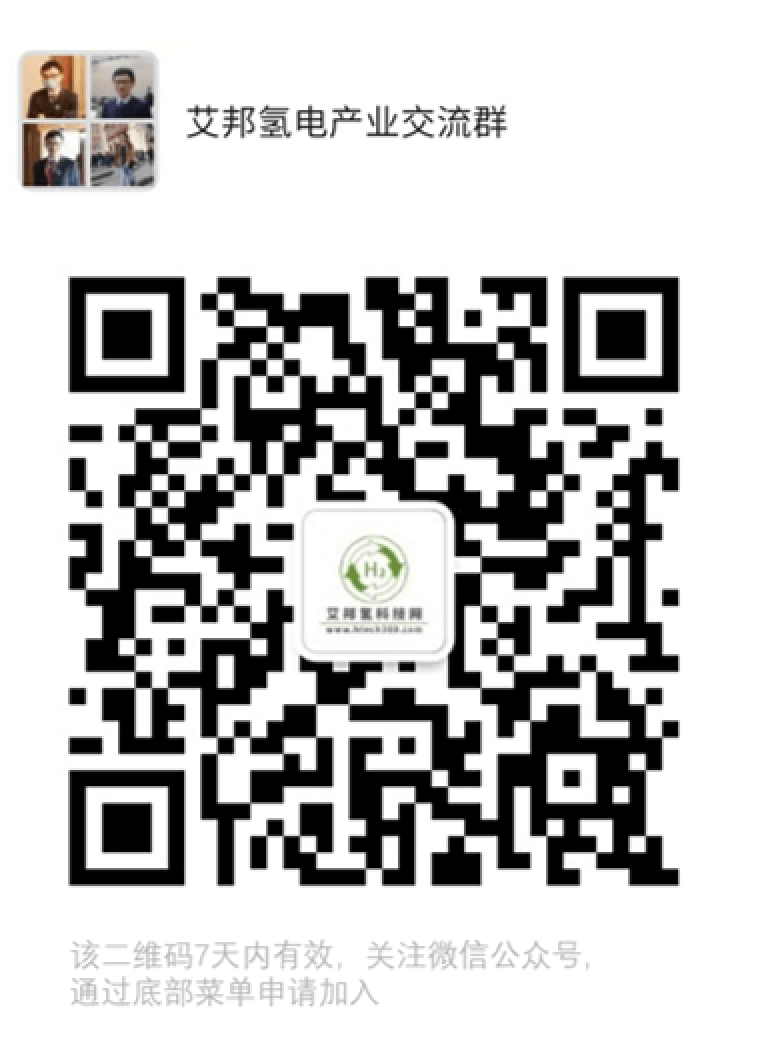