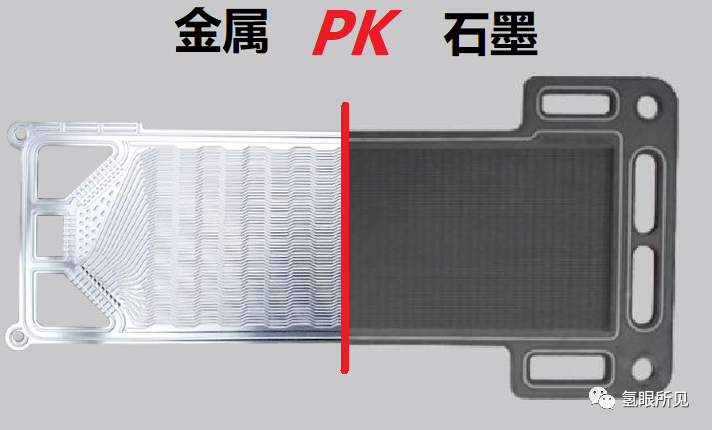
在氢燃料电池业界也一直存在着一个争议或者讨论,那就是氢燃料电池的未来到底是金属板还是石墨板,基于这个话题我们根据性能需求和成本做一些简单分析和预判。(简单归类,石墨复合板归类于石墨板)
从在这个层面看两者无本质区别,以现状流道截面(长*宽)需求来讲基本都可以实现功能,采用机加工的石墨板在异形流道加工上会略显欠缺;对于模压石墨板来说几乎和冲压成型的金属板在流道型式上无差别。
从材料特性的大方向看,石墨的导电性几乎是不锈钢的4倍,导热性也远优于不锈钢。当然以需求来论金属板和石墨板都能满足燃料电池需求。(现在也有很多复合石墨,我们以电阻率和导热系数评价和对比其性能就好)
现状都会对双极板表面做一些疏水处理,比如憎水溶液的浸泡等等,或者其他表面处理。这个层面也无大的区别。
尽管不锈钢金属板为了提升抗腐蚀有采用各种途径的工艺镀层处理,但至少现状是和石墨板无法比拟的。这一点上石墨板完全胜出。
1)机械强度。由于双极板在整个电堆中起到有支撑的作用。相对来说金属板在该点上要优于石墨板。尤其在电堆组装后的锁紧力的作用下石墨板会有挤压缺陷存在的可能,这点性能很重要。
单论密度,不锈钢密度大约是石墨的接近4倍,所以从减重的角度还得看最终双极板用材的体积,同样面积下看厚度状况。由于当下金属板最薄有做到1.1~1.3mm的;石墨板最薄也在1.3~1.6mm左右。所以从这个角度看金属板体积功率密度更占优一些。(丰田二代金属板除端板后5.4KW/L;巴拉德最新款复合石墨板HPS系列4.8KW/L)
目前金属板多数供应商给出的数据在5000~10000小时之间;石墨板给出的是12000~30000小时之间。目前在这一点上石墨板有明显优势。
寿命是一个需要长期实际工程运营验证的数据,尽管有一些替代耐久性验证方案和标准,但也仅能是个参考。
影响成本的因素来自两个层面。一是材料本身;二是加工工艺。从原材料的角度不锈钢单价接近石墨的2倍。但是从加工工艺复杂程度(原料准备—成型—表面处理—焊接(或粘结)—密封,金属板一般在焊接后再表面处理,石墨板多数是在表面处理后粘结)全流程来看,金属板子的加工工艺还是要容易一些。
石墨板采用卧式铣床结合专用定制刀具的方式目前生产效率也明显提升了;但金属板目前是可以上全自动生产线了。这个环节生产效率肯定是金属板高(焊接一片50秒左右)。以整个流程来看传统石墨板瓶颈是在机加工环节,金属板和石墨板在密封胶线安装目前工艺效率也是比较低的。但具体量化成本的数据目前还未能实际调研到,但从整堆来看目前成本差异不大。
5.未来的趋势问题(从一些前沿研究以及最新专利检索来看)
1)目前石墨板已经再往复合板的方向上走了,在保持石墨板基本性能的同时可以获得接近金属板的优点性能,如采用模压的成型方式来提升效率、减小厚度来降低成本并获得更大的体积功率密度。
2)采用金属框架做支撑,镶嵌石墨板做流场的结构。(有多种型式的框架)
4)金属板的其他镀层提升抗腐蚀性,来获得更高的寿命。
1.以当下国内推广商用车的使用背景来看,对寿命需求是首要指标。基本可以判定这个阶段还是要以石墨板(包含材料复合、结构复合这个大类)为主的。
2.以技术趋势和加工成本来看最终要达到一个殊途同归的个结果,也可能是一个兼容不锈钢和石墨优势的中间态。
3.近期天津大学提出的一个观点和路线值得关注,为了获得更高的功率密度和寿命未来的极板、MEA会是一个完整的复合单体,而不是一个组合件。原话描述为:“一体化”和“有序化”是未来设计的两个重要方向:一方面,双极板进一步减薄会极大增加流动阻力,给反应气体供给和冷却液循环带来困难,因此流场和电极的一体化设计是一种趋势;另一方面,电极设计的有序化能够更好地组织传递过程,并降低生产过程中的不确定性,也是未来的发展方向。下图是未来的技术路线图:
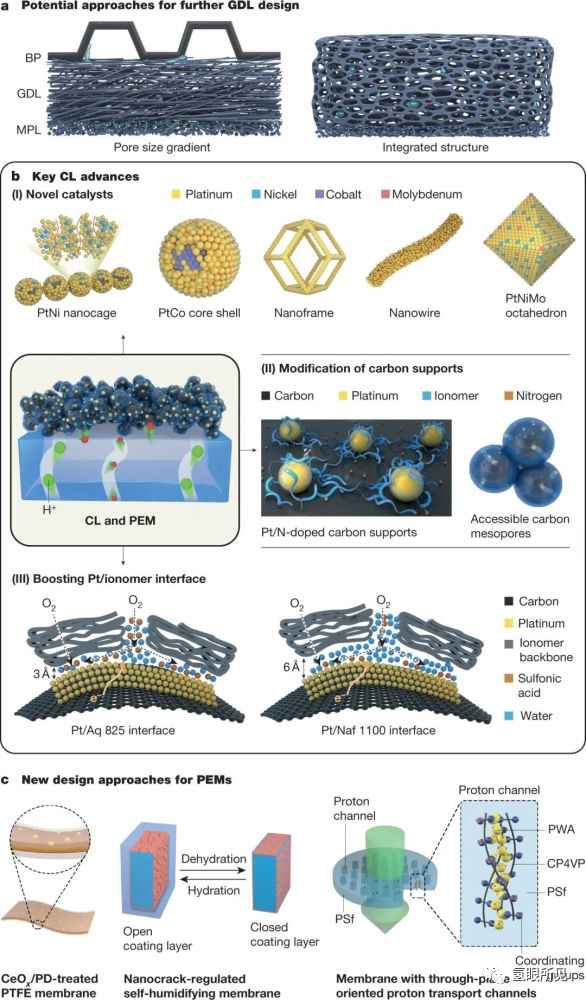
原文始发于微信公众号(氢眼所见):关于氢燃料电池石墨板还是金属板的思考