侯树文 科技日报记者 王春
在上海治臻位于临港新片区的冲压生产车间,体型庞大的冲压设备的下面,厚度只有0.1毫米的金属板上被冲压出一道道细密流道。这些流道深度在0.3毫米-0.5毫米之间,宽度在0.8-1.0毫米之间。记者了解到,氢燃料电池核心零部件金属双极板上的细密流场具有跨尺度特征,要求达到微米级的精度。为了保证每副金属双极板生产的精度和一致性,在上海治臻的生产车间,每一块金属板的摆放角度都要经过严格培训。
“高功率密度燃料电池薄型金属双极板及批量化精密制造技术”获上海市技术发明奖特等奖 摄/睿宁
在氢燃料电池汽车中,电堆是氢气和氧气发生化学反应的场所,流道主要用于气体的分配。“金属双极板流道中的氢气在催化剂作用下发生电离反应,产生的氢离子透过两片双极板之间的膜电极,与另一块极板上的氧气反应成水,最终形成电流。”上海治臻新能源装备有限公司总经理蓝树槐介绍到。5月19日,上海市科学技术奖颁发,该公司参与的“高功率密度燃料电池薄型金属双极板及批量化精密制造技术”获上海市技术发明奖特等奖。
电堆是氢燃料电池整车制造的核心。“金属双极板是氢燃料电池关键组件之一”,该项目第一完成人上海交通大学来新民教授介绍,“功率为100kW的电堆需要400多片金属双极板和膜电极叠装而成,其中双极板占电堆体积的80%,承载氢、氧、水三场传输和导电功能。”
创新工艺实现燃料电池车全功率驱动
据了解,在氢燃料电池产业领域,与国际先进水平相比,我国在基础材料、关键核心零部件等方面还有较大的差距。国内氢燃料电池领域,质子交换膜、催化剂、膜电极等关键零部件缺失,以及产业化高成本一直是套在这匹马上的双重枷锁。其中质子交换膜被美国一家企业垄断,该公司掌握了全球90%的市场。
根据我国2016年发布的“节能与新能源汽车技术路线图”,2030年,中国氢燃料电池汽车的规模达到100万辆。上海治臻建立了全套的金属极板制造技术体系,打破国外垄断,突破电堆核心部件自主化,为上汽乃至中国氢燃料电池技术跻身国际一流行业提供了关键支撑。
从2005年上海交大实验室的基础研究,到2010年世博会期间的工程化应用,再到2016年至今的产业化落地,金属双极板历经十多年核心技术攻关。
与传统的石墨极板相比,金属双极板在厚度、槽深偏差、寿命、产业化具有优势,更加符合车用电堆高功率密度、大功率输出、长寿命运行和低成本制造的要求。据了解,基于“两板三场”的新结构,金属极板厚度要比业界最薄的石墨板降低52%,比石墨极板电堆功率密度提升2.4倍,使得提高功率的同时,减少了电堆体积,实现电堆在轿车前舱的布置。
2019年世界新能源汽车大会上,“两板三场”金属双极板燃料电池被评为代表新能源汽车方向的八项前沿技术之一。传统的“三板三场”结构由阳极板、隔板、阴极板三层构成。而“两板三场”结构则通过冲压件的间隔支撑和错层密封形成翻转的流场,采用两个冲压件形成独立联通的氢、氧、水三个流场。
基于该结构,团队发明氢、氧、水流场的新型分配形式,从第一代直道流道、到第二代叉分流道再到第三代导流岛分配,通过板厚减薄和流场匀化,双极板功率密度由2.4kW/L、2.75kW/L提高到3.3kW/L。
此外,该项目还创新多工序精密成形工艺,将流道深度精度提高了4倍,突破金属双极板电堆叠装的接触均匀性瓶颈,开发出首个400片115kW大功率车用电堆,实现氢燃料电池车的全功率驱动;发明不锈钢双极板耐蚀导电多元复合涂层,国内首次通过10000小时寿命考核,满足10年使用寿命要求;
年产50万片,占据国内主流市场
量产规模和自动化生产影响氢燃料电池产业成本,而上海治臻金属双极板量产规模已达到年产50万片。冲压、焊接、涂层、密封到最后的成品,每天1000多片的金属极板在治臻新能源的生产线上产出。
在核心技术开发过程中,团队的最大挑战在于克服供应商配套加工能力不足。“比如前期研究中,基材厚度均匀性、模具的加工精度不能满足要求,团队就要通过流道构型和工艺设计等给予其更大的自由度。”蓝树槐表示。随着主机厂市场需求增加,氢燃料电池金属双极板产业化进程加速,提高了国内产业链协同配套能力。
为了让金属双极板达到批量化生产,技术团队自主研发了30多套新的装备。从单极板成形、双极板振镜扫描激光焊接、磁控溅射涂层等装备,实现金属双极板多品种连续化制造,建成首条多品种金属极板全工艺流程生产线,建立极板质量控制系统,是全国第一家通过IATF16949质量认证的金属双极板生产线。
上海治臻首次实现了高性能高精度金属双极板从构型设计到全工艺链加工的一体化交付能力,其产品在上汽集团、长城汽车、新源动力、中船重工、武汉理工新能源、上海电气等国内知名主机厂、电堆公司得到批量应用,占据国内氢燃料电池金属双极板市场90%以上。
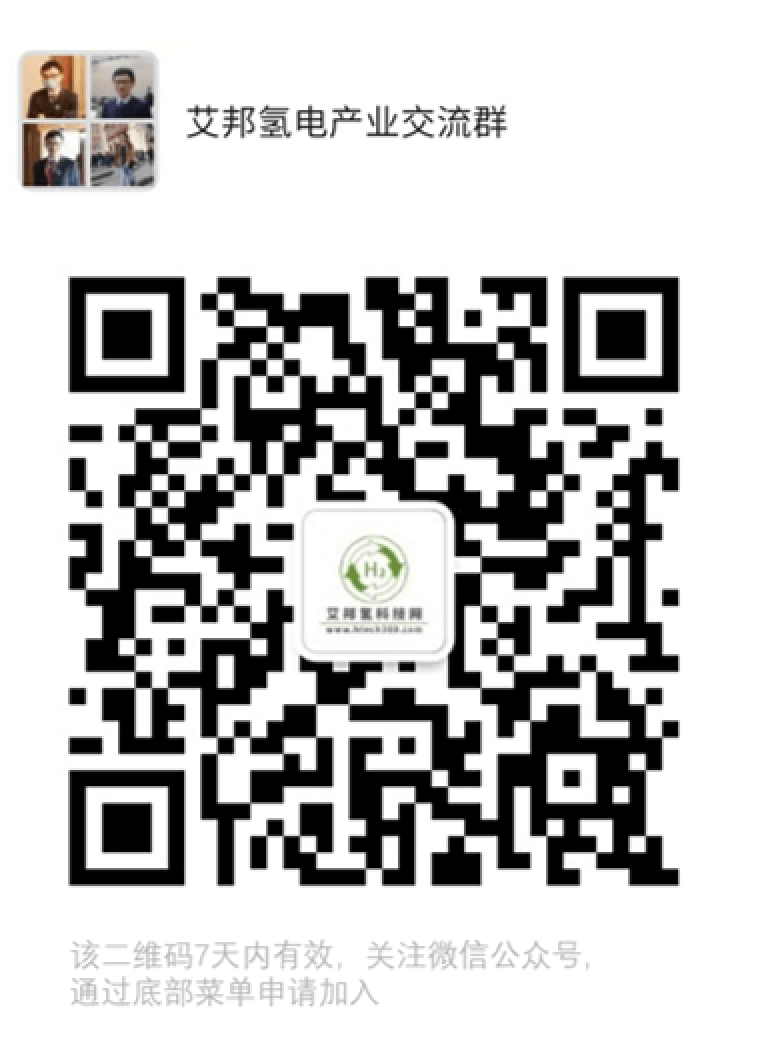