说明:
1.本文为接续上文《氢燃料电池膜电极(MEA)生产工艺详解》
2.上文讲到三合一的MEA已经加工完成。三合一分别为中间层PEM、阴阳两侧催化剂层。
3.今天接续《气体扩散层GDL的生产工艺以及最终贴合工艺详解》形成七合一的MEA模组.
4.七合一一般指:在三合一的基础上加入包含微孔层MPL的气体扩散层GDL
5.一般来说会倾向于将微孔层MPL与扩散层GDL烧结在一体。
下 面 正 式 开 篇
一、GDL生产、与MEA贴合工艺流程总述
工艺流程图
GDL工艺说明:
-
切碎碳纤维——形成碳纸——碳纸树脂浸渍——石墨化——憎水处理——烧结微孔层——与前制程形成的MEA贴合
-
本GDL工艺从碳纤维开始。碳纤维的制造工艺这里不再描述。
二、GDL的生产、与MEA的贴合具体工艺详解
1.切碎碳纤维
切碎碳纤维的工艺流程示意图
1)物料准备
干燥的碳纤维材料。
2)切碎纤维所有设备
压辊、刀片辊、带有聚合塑料齿的钢辊、碎纤维接料斗。(也可用切断机替代以上设备实现切碎纤维的工艺)
切碎碳纤维原理示意图
说明:主要是实现碳纤维束切断,可以用其他工艺替代。
3)启动设备切碎碳纤维。
工作原理为:图示蓝色聚合塑料齿压住碳纤维,黄色刀片辊图示灰色为切刀切断碳纤维,图示黄色为含有高压气流的聚合塑料齿用来给切割施压和将切断的碎料脱落。
4)切碎过程参数控制:
a.切割速度:9m/分钟
b.纤维切断长度:6~12mm
c.压辊压力:0.1MPa
5)影响品质因素
切刀的锋利程度、切刀材料和形状
6)品质特征
碎纤维的表面形状和外观
2.形成碳纸(造碳纸)
形成碳纸的流程示意图
1)材料准备
上制程加工好的碎纤维、聚合物粘结剂、水。
2)所用设备
料斗(装碳纤维和粘结剂混合悬浮液)、斜筛网、压辊、加热辊、传送带(如上图设备部件标注)。也可以采用类似无纺布等生产工艺设备替代。
3)加工流程:
a.悬浮液从料斗均匀分布到筛网上,筛网可以将悬浮物留在网带上,其余溶剂以及水分从网眼向下排出。
b.经过压辊挤压整平排水形成为干燥的碳纸。
c。潮湿碳纸经过多次热辊干燥形成干燥的碳纸同时粘结剂也固化了。
d.通过冷却压延结构形成最终碳纸。
e.采用质量传感器监控碳纸质量分布均匀度等。
4)造纸过程参数控制
a.生产能力:300~320平方米/小时。
b.比重15~70g/平方米。
c.材料厚度:150~300 µm。
d.粘合剂含量:≤25%。
e.采用质量传感器监控碳纸质量分布均匀度等。
5)影响品质因素
悬浮液的含水量、压延过程间隙和压力的控制、纤维分布状况、粘合剂的均匀分布、碳纸张力等。
6)品质特征
碳纸厚度均匀性、材料表面平滑、碳纸湿强度、表面无破坏。
3.碳纸树脂浸渍
碳纸树脂浸渍工艺示意图
1)所需材料:
前制程制备好的干燥碳纸、热固性树脂(如酚醛树脂等)
2)所需设备:
传送辊、压辊、导向辊、隧道式烤炉、浸渍槽等。(可以采用红外干燥以及分切后隔离堆叠的方式去替代)
3)加工流程:
a.用热固性树脂(例如酚醛树脂)浸渍碳纸,以获得所需的材料强度和孔隙率。此外,经过石墨化处理后,导电性和导热性增加。
b.通过压辊去除多余的液体。
c.在150度的隧道式烤炉内挥发残留溶剂并固化树脂。
4)树脂浸渍过程参数控制
a.干燥温度:150度。
b.材料厚度:200~270 µm。
5)影响品质因素
浸渍所有树脂的材料成分构成、干燥时间、干燥温度。
6)品质特征
材料厚度和密度。
4.石墨化(为了获得更好的弹性模量和更高的电气以及机械性能、导热性、抗氧化性)
石墨化工艺示意图
1)所需材料:
前制程浸渍树脂后的碳纸。
2)所需设备:
传送辊、烤炉(在氮气或者氩气或者真空状态的环境内,温度约为1400~2000度)。可用惰性或者真空环境的批量碳化设备替代。
3)加工流程:
a.碳纸在惰性气体环境(氮气、氩气)或在真空中下的熔炉中加热,加热至约1400-2000°C的温度(在间歇过程中超过2000°C)。
b.烤炉内会有不同的温度区,最后在冷却区冷却至常温。
c.最终形成厚度为150至300µm的材料。
4)石墨化过程参数控制
a.烤炉过程温度:1500~2500度。
b.材料厚度:150~300 µm。
c.材料密度:0.2~0.3g/立方厘米
d.工艺时间:自动流水线≤5分钟、间歇式工艺:≤15分钟(以上均在惰性气体或者真空状态下操作)
5)影响品质因素
石墨化过程温度曲线(趋势)管理、去除热解产物的低温石墨化阶段、烤炉的惰性工作环境。
6)品质特征
树脂的热解度≥99.5%、产品无死角全覆盖、电导率、碳含量。
5.憎水处理
憎水处理工艺流程示意图
1)所需材料:
前制程石墨化处理后的碳纸、憎水剂(PTFE类、氟乙烯、丙烯(FEP))。
2)所需设备:
传送辊、隧道烤炉、压辊、导向辊、浸渍槽等。(可以用喷涂、涂布等其他工艺来代替处理)
3)加工流程:
a.将GDL基板在PTFE浸渍槽中浸渍。
b.经过压辊去除多余溶液,有助于调整疏水性。
c.GDL中的PTFE可以由悬浮液的比例进行调整。
d.通过烤炉干燥去除剩余溶剂,约在300°C-350°C下烧结将PTFE颗粒结合到基材上。
e.干燥过程的速度影响PTFE在材料中的分布。快速干燥将导致PTFE保留在表面区域,而缓慢干燥能确保整体分布均匀。
4)憎水处理过程参数控制
a.干燥温度:300~350度。
b.PTFE质量分数:5~10%。
c.材料厚度:200~270 µm。
5)影响品质因素
憎水剂的成分、干燥时间、干燥温度。
6)品质特征
PTFE的均匀分布。
6.微孔层MPL烧结(主要作用是反应气体均匀分布和水管理,去除液态水)
微孔层MPL烧结工艺流程示意图
1)所需材料:
前制程憎水处理后的碳纸、MPL材料(由碳或石墨颗粒和聚合物粘合剂(如PTFE)组成,其孔径在100至500 nm之间;碳纸孔径一般在10~30 µm之间)。
2)所需设备:
传送辊、隧道烤炉、涂布设备、纵向分切刀具、在线摄像监控系统等。(可用的替代设备狭缝涂布、丝网涂布、喷涂等)
3)加工流程:
a.用刮刀将MPL浆料涂布于前制程加工好的材料上,大约厚度<50 µm。
b.采用慢干的方式可以有效改善裂纹,同时增加MPL层的附着力。
c.对干燥后的GDL进行分切,经过CCD进行品质检查,标记缺陷产品,最终采用离型膜分隔包装。
4)MPL烧结过程参数控制
a.MPL孔径:100~500nm。
b.烧结过程时间:≤10分钟。
c.烧结过程温度:250~350度(逐渐温升有利于改善干燥效果)
d.MPL层厚度:<50nm。
5)影响品质因素
憎水剂的成分、干燥时间、干燥温度。
6)品质特征
MPL的附着力、干燥温度不能超过其熔点、MPL表面无损平滑。
7.完整的GDL与前制程加工好的MEA贴合
最终贴合工艺流程示意图
1)所需材料:
成品GDL、上章节内容里加工好的MEA、热压粘合剂。
2)所需设备:
传送辊(带)、导向辊、粘结剂涂布设备、热压辊、刀模辊、纵向切割刀模、交叉切割模。(其他不连续的贴合生产设备、粘合剂涂布设备)
3)加工流程:
a.CCM在两侧连接到GDL,然后分离。形成带保护膜层的MEA。。
b.将粘合剂涂抹在GDL上,根据需要的几何形状对GDL进行冲切孔。
c.冲切好孔位的GDL定位在MEA密封边框的顶部和底部。
d.经过热压进行连接。
e.根据产品工艺设计进行纵横向切割。
f.由于材料的特性导致该加工过程位置精度不是很好管控,需要特别注意公差管理。
4)MPL烧结过程参数控制
a.热压温度:100~160度。
b.接触压力:1.000 ~10.000 kgf/cm²。
5)影响品质因素
整个加工系统轴向、径向角度和偏移量的管控,供料速度、热压温度和压力、以及时间的组合管理,主动压力持续时间。
6)品质特征
GDL的位置精度、连接强度、切割几何形状的精确度。
以上工艺过程就完成了完整的七合一的MEA制作
原文始发于微信公众号(氢眼所见):氢燃料电池气体扩散层GDL的生产、MEA贴合工艺详解
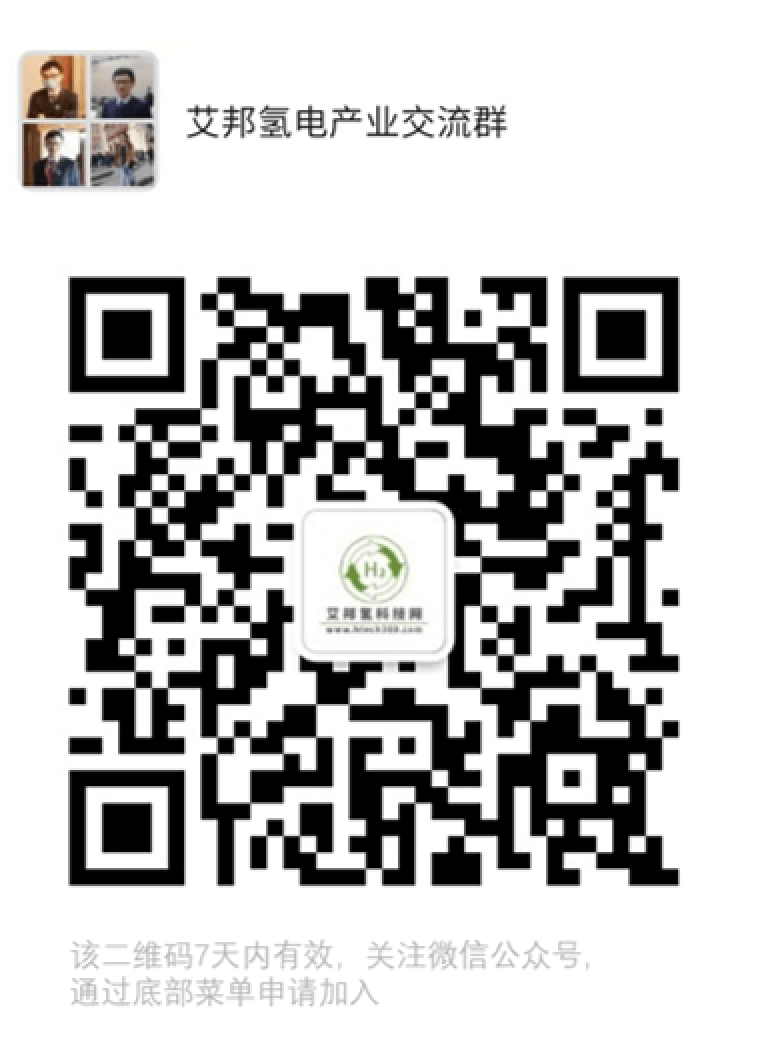