气体扩散层在工作中蕴含着 “气—水—热—电—力” 复杂多物理场的共同作用,焦博士最新的文章。
评价影响 GDL性能的核心指标可以从其厚度及厚度均匀性、密度、机械性能、透气率、粗糙度、电导率、热导率、亲疏水性等出发,整体涵盖了燃料电池气体扩散层的尺寸特性、力学性能、电学性能、热学性能,从多个角度实现对性能的综合评价。
当前常见的 GDL厚度为 160~240 μm,GDL的厚度及厚度均匀性属于 GDL本身的尺寸特性,其对 GDL的整体性能起到了基础影响作用。考虑GDL具有支撑电极的作用,在装配过程中不同厚度的 GDL压缩变形量有所不同,同时也会影响到产品设计中的密度、透气率等参数。
相比于 GDL厚度,将厚度均匀性作为 GDL产品的考核指标更具实际意义。厚度均匀性直接反映产品的生产工艺等,其会影响到接触电阻的大小。同时厚度均匀性过差的产品在装配过程中,部分纤维突入流道会造成流阻过大;此外,严重时还可能会刺破电极或质子交换膜,造成燃料电池损坏。
密度与碳纤维的分布情况紧密相关,一定程度上与 GDL的孔隙率、厚度等具有直接关系。测评常采用面密度和表观密度(体密度)来进行衡量;面密度指的是单位面积样品的质量,而表观密度指的是单位体积样品的质量。显而易见,密度测量机理是采用质量除以面积或者体积的方法进行。样品的密度决定了碳纤维的用量,同时作为产品设计的基本性能为整体产品质量奠定了基础。
一般情况下每层内的碳纤维数量越多,GDL的密度越大。然而此时,GDL的孔隙率大小会降低;同时测试发现,GDL厚度值越大其表观密度也会越大。因此,GDL的各项性能参数之间具备强关联性 。常见的 GDL密度在 0.3 g/cm3。密度反映了GDL生产过程中的碳纤维分散技术及碳纤维的数量情况。
拉伸强度反映了 GDL生产制造工艺的特点,其性能主要取决于碳纤维自身强度、浸渍粘结剂碳化后的强度,与压缩特性、抗弯强度一同组成了GDL的典型力学特性,也即机械性能。由于 GDL在支撑电极方面的重要作用,其力学特性是核心性能指标之一。从测试角度而言,三者需要借助力学试验机进行 ,并配备相应的力学传感器和测试夹具。
GDL拉伸强度反映了 GDL制造过程中的技术路线的差异性。包括了纤维本身的强度,以及碳化、石墨化过程中的工艺水平,碳纤维的直径尺寸也会影响到力学性能。具有较好强度的 GDL可为质子交换膜燃料电池的安装和使用带来保障,同时稳定整个电极的结构,提高电池的寿命。GDL产品的拉伸强度更多地由浸渍粘结剂碳化后的强度决定,如树脂加工制造过程的差异性。
拉伸强度对性能的影响还体现在生产过程中产线的稳定性,批量化生产时不会从中间断裂,体现在电堆装配过程中性能的稳定性。GDL强度太差发生断裂会对性能造成恶劣的影响,包括刺破电极、断裂后热导率、电导率性能急剧下降、接触电阻/热阻升高、电极压缩受力严重不均匀造成电流密度分布、水传输通道及水管理、气体传输通道等偏离设计值,使得电池性能及寿命急剧下降。
燃料电池堆在装配过程中的预紧力会造成GDL发生压缩形变。在压缩状态下,GDL的孔隙率、孔径、厚度等等都会发生变化,进而影响到 GDL整体的水热传输性能。严重时,压缩变形幅度过大会造成 GDL内部发生断裂,使得其传导能力大幅下降。因此压缩特性是 GDL支撑电极的直观表现。在电池装配过程中,由于沟脊结构型的双极板设计,脊下的 GDL变形幅度更剧烈,会影响到脊下的传热及传质过程。因此,研究人员的一种设计理念便是通过改善流道和 GDL设计以强化脊下的横向传输。由此可以看出,压缩特性对于 GDL的性能至关重要。
电堆在装配过程中常见的压缩率大致在 10%~30%之间。由于 GDL的压缩幅度跟多种因素相关,难以直接评价具体压缩率对燃料电池性能的影响作用。研究人员也力图建立压缩率与性能之间的关联式,但普适性及准确度还有待于进一步验证。燃料电池用 GDL的厚度常在 160~240 μm之间,因此同等压力下压缩幅度也各不相同。一般厚度越大的变形幅度也越大 ,但整体压缩率较为接近。
当前压缩过程中需要重点考虑的是形变的均匀性以及压缩过程中变形情况。由于燃料电池沟脊结构的存在,理论而言脊下的压缩变形要高于沟下的变形量。而在装配过程中由于压缩导致的断裂以及纤维凸出至流道是更应该关注的影响因素。GDL断裂会影响到自身的全部本体性能指标以及对电极造成损伤。当未发生断裂仅凸入流道时,会造成流道内的压损升高,同时对于液态水的排出也较为不利。
此外,当前燃料电池一个重要的发展方向是单电池集成一体化装配。即若电堆中的某片发生了损伤,则电堆仅更换其中一片,实现快速更换大大降低成本。但电堆拆换后再进行装配,性能有可能受到较大的影响,因为再次装配改变了原有的压缩预紧状态。若考虑 GDL的压缩回弹能力,则 GDL在多次压缩过程中的性能一致性也是较为重要的性能指标。由于 GDL是膜电极中厚度最厚的部件,因此也是拆装过程中影响性能稳定性的最重要的部件。
粗糙度主要考察 GDL表面的光滑程度。表面粗糙度过大会增大 GDL与极板间的接触电阻,甚至会刺穿质子交换膜,造成电池不可逆损伤。因此粗糙度也是考察 GDL工艺水平的一个核心指标。
一般采用机械方法进行测试,用探针在纸表面移动,针头随着 GDL表面凹凸变化而上下运动。从测试精度而言,达到±0.1 μm即能满足 GDL的测试要求,且由于 GDL样品规整化程度高,形状简单(复杂程度远低于不规则凹槽结构的工业件),主流测试设备均能应用。研究人员常常采用平均轮廓算术平均偏差和平均轮廓的最大高度来衡量 GDL产品的粗糙度性能。
从形貌而言,粗糙度一方面是 GDL产品表面的凹凸不平情况,另一个方面则是 GDL的毛刺情况。毛刺会刺穿膜或者催化层,造成更大的性能损伤。由于碳纤维中间的孔洞是作为液态水传输及气体供应的通道,因此测试过程中探针在纤维表面和孔之间的反复运动即会产生一定的粗糙度结果。因此需要在选定的测量路径范围内进行平均,用多次测量结果表征整体水平。
透气率主要评价 GDL在气体传输层面的性能。反应气体(氢气或空气)透过GDL传输至催化层进行电化学反应,因此透气率直接决定了反应气体供给的能力。GDL的透气率与内部孔隙结构紧密相关,包括孔隙的分布及孔径的尺寸。一般而言,GDL的透气率需满足一定的阈值以实现足量的气体供给能力,在阈值之上,设计重点便不必着眼于透气率,要更为平衡地考量其他性能如电导率、孔径分布等等。当前,在反应气体过量系数较大时,阈值有可能较小。但考虑电堆装车运行时,提高燃料的利用率及减小空压机的寄生损失,对 GDL的透气率提出了更高的要求。尤其在高功率密度运行时,对气体供给速率的需求极高,且由于产物水的堵塞,更可能会引起电堆的缺气“饥饿” 。因此透气率性能是 GDL评价的核心指标之一。
一般而言,炭纸基底层透气率都处于较好的水平,但在装堆过程中会在基底层基础上涂布微孔层改善接触电阻及水热管理性能。由于微孔层极为致密,会导致 GDL透气率在原有基础上衰减上百倍甚至千倍。虽然涂布微孔层制成的 GDL透气率性能大大降低,但装配成膜电极进行试验,由于接触电阻等的改善,电池的电化学性能还有可能上升。这也体现了 GDL各项指标间的制约协调作用。
电阻率是影响 GDL性能的最为核心的指标之一。降低电阻率可以有效减少燃料电池的欧姆损失,提高导电能力。欧姆损失的直观表现是通过产热的途径损耗,这意味着电阻率也会影响到电池的热管理性能。平面方向电阻率受产品制备工艺的影响,如碳纤维的分散、碳化、石墨化的效果等。
相比于平面方向电阻率,由于电子传输的方向,垂直方向电阻率对电池性能影响更甚。在测试过程中,常选用不同压力下的垂直方向电阻率值来代表,也有助于装配预紧力等的确定,如 0.6 MPa及1 MPa下的垂直方向电阻率值。
水热管理性能是现阶段质子交换膜燃料电池调控的重点和难点。为了保证电池正常工作温度区间在 60 ℃~90 ℃,热导率起到了至关重要的作用。当前测试热导率的方法有稳态法和瞬态法等。稳态法采用上下冷/热极形成热流温度梯度进行计算,而瞬态法如激光闪光法使用短能量脉冲照射样品的正面,并使用红外探测器记录样品背面的温度变化情况。
由于燃料电池产物水需要高效排出以免堵塞气体传输通道造成电池“水淹” ,GDL的亲疏水性处理即为提升排水能力。常见的是采用一定量的聚四氟乙烯(Polytetrafluoroethylene,PTFE)来实现GDL的亲疏水性处理,使得接触角为 120°~150°左右。在涂布微孔层设计的 GDL中,亲疏水性也具备差异性。一般而言涂布微孔层的表面接触角更大,疏水能力更强,但也与产品的设计紧密相关,部分产品两面的接触角差异性较小。
GDL测试的相关指标除了来源于产品本身的理论应用场景以外,还来自于行业积累的长久经验。如本体性能中的厚度及厚度均匀性、电导率、热导率等;反映工艺水平的粗糙度,应用场景不同亲疏水性不同而进行不断优化设计的接触角;由于装配条件不同使得压缩特性、抗弯强度等指标对于材料工艺等提出了更高的要求。而评价指标会随着技术发展水平的不同而确立新的发展目标,进而催生测试方法、测试装备等的更迭。
如何构建完美的三相界面不只是CL的问题,是侧重于跨尺度和跨组件传输的优化,同时在结构控制和润湿性方面与其他组件的改进相兼容,这里GDL起到承上启下的重要作用。一直以来,如何做到完美匹配将工程问题与化学问题找到兼容点一直困扰着设计者。在GDL层面小编认为可以从本文的八个测试评价参数尝试找到平衡(某一个参数的优异≠性能表现优异)。更为复杂的是,不同测试评价参数之间也存在着强相关性,所以GDL的匹配设计是复杂且,需要根据设计者的思路,以平衡的、整体的思维去考量。
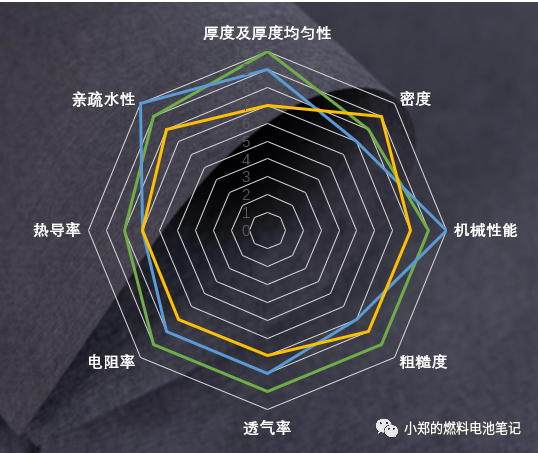
原文始发于微信公众号(小郑的燃料电池笔记):关于气体扩散层测评技术