1.双极板
技术路线 |
优势 |
劣势 |
应用现状 |
未来发展方向 |
备注 |
|
金属双极板 |
涂层金属(碳基、金属基) |
导电导热性能好,机械性能优越,制造容易,成本低,结构耐久性好,抗冲击和振动、可形成超薄双极板 |
易腐蚀 |
金属双极板因具有更大的功率密度和更为成熟 的生产工艺而成为乘用车应用的主流,丰田 Mirai、 现代 NEXO 等均采用的是金属双极板 |
未来金属双极板须突破金属薄板成型、 表面涂层寿命的关键技术在乘用车市场将有更广阔 的发展。 |
寻找性能优良且成本低廉的双极板新材 料和加工方法是燃料电池汽车产业化的重要课题。 高性能、 低成本模压成型的热固性树脂 /石墨板和具有优异 性能的金属板是双极板未来发展的趋势。欧美日石墨、金属双极板整体较强,美、英复合材料双 极板处于世界先进水平,国内石墨双极板部分性能达 DOE(2015 年)性能指标水平,金属和复合材料双极板 提升空间大。 |
无孔石墨双极板 |
耐蚀性能好,导电导热性能高,化学性能稳定,制造工艺成熟 |
机械性能差(脆性),质量和体积大,可加工性差,加工成本高 |
国内石墨双极板发展较为广泛,主要采用 机加工方式和模压石墨板进行生产,由于石墨双极板寿命长且商用车对于体积比功 率要求相对较为宽松,因此,石墨双极板在商用车领 域应用广泛。但由于石墨板体积大无法制作薄板及 冷起动的问题使得石墨双极板应用于乘用车存在一 定困难。 |
/ |
||
复合材料双极板 |
金属基复合材料 |
耐腐蚀、体积小、重量轻,强度高 |
电导率高,成本高 |
复合材料双极板多数处于研究阶段,目前市场上 复合石墨板电堆较少,主要由于其成本高,工艺复杂, 难以批量生产 |
未来通过改进复合石墨板材料,提高 应用可靠性,结合金属双极板与石墨双极板的优点也会有较好的应用前景 |
|
碳基复合材料 |
2.质子交换膜
技术路线 |
优势 |
劣势 |
应用现状 |
备注 |
全氟磺酸膜 |
机械强度高,化学稳定性 好和在湿度大的条件下导电率高;低温时电流密度 大,质子传导电阻小 |
温度升高会引起质子传导性变差,高温时膜易发生化学降解;单体合成困难,成本高;价格昂贵;用于甲醇燃料电池时易发生甲醇渗透等 |
全氟磺酸离子交换膜由碳氟主链和带有磺酸基团的醚支链构成,具有极高的化学稳定性,是目前应用最广的燃料电池膜材料。目前在国内外应用最广泛的是由美国杜邦公司研制的 Nafion 系列全氟磺酸质子交换膜。全氟磺酸质子交换膜仍然是商业化应用的最优选择 |
质子传导性与阻醇性作为 PEM 的基本性 能 指 标,影响着 PEM 材料的合成与改性方向。而在高温 环境中的使用性能,则关系到 PEM 的应用前景。同 时机械性能、溶胀度、含水率和离子交换容量等也是 表征 PEM 性能的重要参数。 |
非全氟化质子交换膜 |
加拿大 Ballard 公司的 BAM3G 膜的主要特点是具有非常低的磺酸基含量、高的工作效率,并且使单电池的寿命提高到15 000h,成本也较 Nafion 膜和 Dow 膜低得多,更易被人们接受。 |
制备工艺复杂,机械强度和化学稳定性不好,不能满足燃料电池长期使用的要求 |
部分氟化质子交换膜是指聚合物主链为全氟或部分氟化结构,其侧链中的官能团通常具有磺 酸基团。 |
|
无氟化质子交换膜 |
机 械 强 度 高;成本低而且环境污染相对较小 |
主要问题是它的化学稳定性差,质子电导率低 |
无氟化膜实质上是碳氢聚合物膜,是质子交换膜发展的一大趋势。 |
3.催化剂
技术路线 |
应用现状 |
未来发展方向 |
备注 |
|
铂基催化剂 |
单原子铂基催化 剂,Pt/C,碳作为催化剂的载体,Pt以纳米颗粒 (PtNPs)的形式负载其上 |
Pt/C是目前质子交换膜燃料电池中所用的商业化催化剂。 |
高性能 Pt 基、 低 Pt 以及非 Pt 燃料电池电催化剂 |
如何在降 低 Pt 用量的同时保证高耐久性,从而大幅缩减成本,达到“降本增效”的目的,是目前燃料电池 ORR 电催化剂领域的研究重点 |
合 金 型 铂 基 催 化剂 |
||||
核壳型铂基催化剂 |
||||
特殊形貌的铂基催化剂 |
||||
非铂催化剂 |
钯系催化剂 |
|||
含过渡金属氮掺杂碳材料催化剂 |
||||
金属氧化物催化剂 |
||||
非金属碳基材料催化剂 |
4.气体扩散层
技术路线 |
优势 |
劣势 |
应用现状 |
未来发展方向 |
备注 |
|
碳纤维纸 |
干法工艺 |
该工艺制备的碳纤维纸碳纤 维含量较高,产品强度较高 |
干法工艺所采用纤维较 长,导致产品匀度较差 |
国外机构对于碳纤维纸的研究起步较早,工艺较成 熟,性能较好。目前,可以批量生产且能满足燃料电池气 体扩散层要求的高性能碳纤维纸生产企业主要包括日 本东丽公司、德国SGL公司以及加拿大BallardMaterial Products公司等我国在碳纤维纸领域的研究较为落后, 虽然在“八五”期间,我国就有过碳纤维纸的研究,但仅限于实验室阶段,且产品性能无法达到相关要求。我国尚未实现高性能碳纤维纸产业化,国内开发燃料 电池所用气体扩散层材料大多来源于日本东丽公司生产 的碳纤维纸 |
国产化 |
|
湿法工艺 |
经湿法成型工艺加工的碳纤维纸具有良好的均匀性和致密 的结构,适合加工成燃料电池用气体扩散层材料,是国外 燃料电池用高性能碳纤维纸普遍采用的生产方式 |
国外对 我国的碳纸出口控制非常严格,不仅出售价格高而且购 买较困难,进口量根本无法满足我国需求 |
5.膜电极
技术路线 |
优势 |
劣势 |
应用现状 |
未来发展方向 |
备注 |
|
第一代膜电极 |
第一代膜电极是最早的膜电极制备技术,使用 Teflon 乳液作为黏结剂将 Pt/C 催化剂通过刮涂、 喷涂、滚压、丝网印刷等方法涂敷在 GDL 上形成催化层,最后将质子交换膜放在两个涂有催化剂的气体扩散层中间通过热压形成膜电极,因此这种方式制备的电极叫做气体扩散电极 (gas diffusion electrode, GDE) |
优点在于工艺简单、电极气孔容易形成、质子交换膜不易发生形变 |
缺点在于以下几个方面:①质子导电率差;②催化层较厚,催化剂利用率低;③催化层与质子交换膜的膨胀系数不同,电池运行较长时间以后电极和质子交换膜容易 分离 |
/ |
有序化膜电极 |
|
第二代膜电极 |
第二代膜电极又被称为催化剂直接涂膜技术 (catalyst coated membrane, CCM),是将催化剂直接涂敷在质子交换膜上然后将阴极气体扩散层和阳极气体扩散层放在两侧进行热压,从而制得膜电极。 |
第二代膜电极经过发展使用Nafion溶 液代替聚四氟乙烯溶液作为黏结剂提高了质子电导率,同时降低了催化层和质子交换膜之间的接触电阻从而大大地提升了MEA的性能 |
极孔隙无序分布导致催化剂利用率不高和催化层传质过电位过大 |
目前最普遍使用的膜电极制备技术之一 |
||
第三代膜电极(有序化膜电极) |
载体材料 有序化催化层 |
这种有序的结构在一定程度上提高了贵金属催化剂的利用率,降低了Pt负载量,且保持了较高的功率密度,同时有序的结构起到水管理的作用,减少了催化剂的聚集现象,有效地延长了膜电极的寿命 |
/ |
3M 公司的 NSFT 催化剂可以实现产业化以外,其他还处于实验室研发阶段 |
||
催化剂有序化催化层 |
||||||
Nafion 纳米结构有序化 |
6.空压机
技术路线 |
优势 |
劣势 |
应用现状 |
未来发展方向 |
备注 |
离心式 |
空压机转速高、尺寸小、质量轻 |
存在喘振现象,在变工况下,性能会变差,甚至影响到压缩机的使用和寿命安全 |
国内的氢燃料电池市场来看,螺杆式空压机所占市场份额相对较多,但现在已经有越来越多的燃料电池和系统厂商开始采用离心式空压机替换 |
||
螺杆 式 |
在工况变化的情况下,其性能几乎 不变,效率高、可靠性高 |
噪声较大、质量较重 |
|||
罗茨式 |
/ |
因压力值达不到氢燃料电池工作的最佳效率点、振动噪声大、效率低 |
|||
涡旋式 |
/ |
受限于自身结构原因,空间占用较大在工作运转过程中,密封条磨损大、寿命短; 在车用变工况使用的情况下,可靠性差 |
7.氢气循环方案
技术路线 |
优势 |
劣势 |
应用现状 |
未来发展方向 |
备注 |
循环泵方案 |
能够对回流量进行主动控制,并且在全工况范围内具有良好的循环效果 |
噪音大、重量大、 成本高、冷启动结冰问题、消耗多余的功率等 |
以上几种技术方案从成本、效率、技术成熟度、资源可行性等不同的角度进行了分 析,综合考量的结果,引射器将成为未来发展的热点,越来越多的整车厂将设计研发的重点放在了全功率范围工作的引射器上,并且在应用层面逐步优化控制策略,从而提高系统应用的合理性和寿命 |
||
单引射器方案 |
结构稳定、成本低、满足全工况范围需求、不消耗多余功耗 |
循环量不可主动控制 |
|||
双引射器方案 |
结构稳定、重量小、成本低 |
不能满足全工况范围需求、循环量不可主动控制 |
|||
引射器和循环泵并联方案 |
满足全工况范围需求 |
体积大、重量大、冷启动结冰问题、 成本高 |
|||
引射器旁通喷射器方案 |
循环量可控、体积小、成本低 |
双喷射器和引射器的匹配控制难度高 |
原文始发于微信公众号(燃料电池汽车):燃料电池关键材料及核心零部件的技术路线、应用现状、未来发展方向
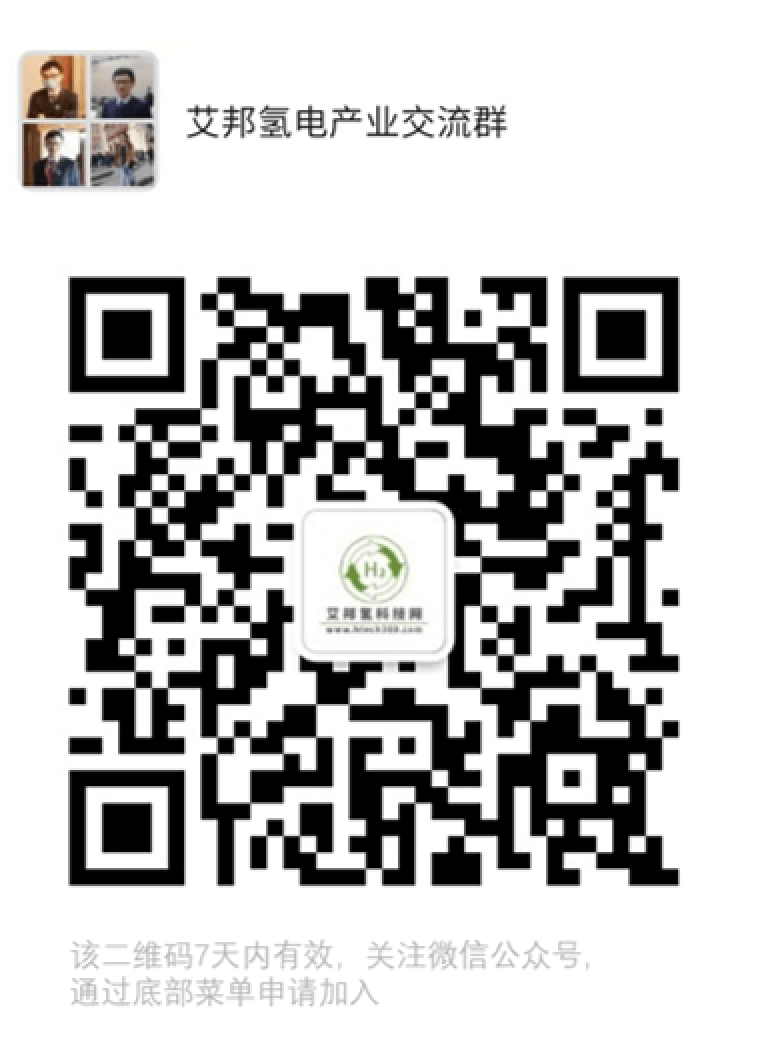