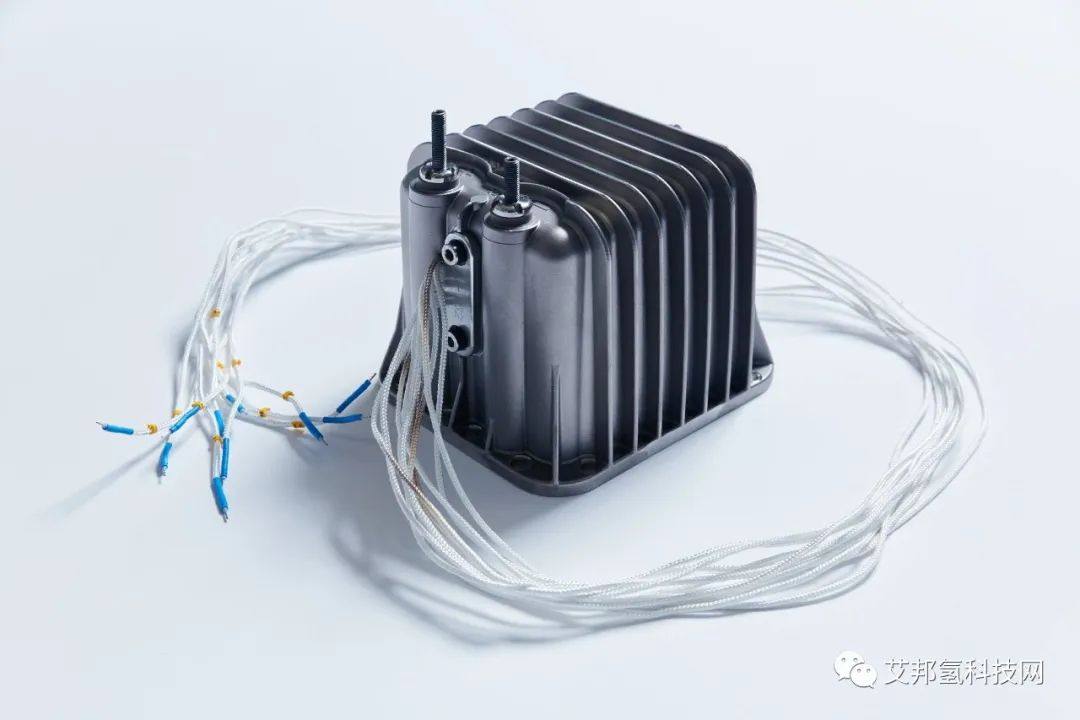
图源Topsoe
过去 100 年来,人们一直在研究电解水生产 H2的方法。然而,由于水是非常稳定的分子,因此分离水分子所需的电能消耗高,目前只有不到1%的H2由电解水产生。然而,由于多年来可再生能源成本一直在显着下降,因此鼓励通过电解生产H2 ,因为该路线是生产 H2的最可持续的工艺。
多年来,已经开发了几种水电解技术。目前,碱性电解(AE)和质子交换膜电解(PEME)已被证实为商业化技术。然而,固体氧化物电解 (SOE) 吸引了许多人将这项技术推向市场,以实现更好的能源效率。其他水电解技术——如阴离子交换膜电解 (AEME) 和质子陶瓷电化学电池电解 (PCECE) 等——正处于开发或示范阶段,本文暂不讨论。
低温电解 AE 和 PEME 在 100°C 以下运行,而 SOE 在明显更高的温度下运行。低温电解槽虽然工作温度低、效率高、技术成熟,但电能消耗较高。在热力学上,电解水的电能需求随着工作温度的升高而降低。因此,如果与余热回收工艺相结合,SOE 高温电解可以减少 30% 到 40% 的电力消耗。因此,与AE和PEME等低温路线相比,高温固体氧化物电解电池(HT-SOECs)可以生产最具能源成本效益的H2 。
本文探讨了生产绿色 H2的几种水电解技术,重点讨论 SOEC 技术及其优势和挑战。
更多行业信息,欢迎加入氢电产业交流群
一、水电解技术
电解是目前可用于直接从水中生产 H2的最直接的方法。水电解是用电离解水,产生纯 H2和副产品氧气。1789 年,Jan Rudolph Deiman 和 Adriaan Paets van Troostwijk 首次演示了使用静电发生器进行水电解。随后在 1888 年,Dmitry Lachinov 开发了一种通过电解工业合成 H 2和氧气的方法。
根据工作温度,电解技术可分为低温电解(LTE)和高温电解(HTE)。
低温电解水是目前最成熟的绿色H 2生成方法。低温电解基于液体或固体聚合物电解质。在这两种情况下,水分子都是通过施加电流而解离的。工作温度限制在 < 100°C。
碱性水电解由不透气膜隔开的阳极和阴极组成。电解质通常是水溶液,包含20 wt%–40 wt% 浓度的氢氧化钠 (NaOH) 或氢氧化钾 (KOH) 。
当将电能用于两个电极时,水分子在阴极解离,通过还原产生 H2和带负电的氢氧根离子。在阳极,氢氧根离子氧化产生氧气和水分子,释放电子。
表1 AEC、PEMEC、SOEC的主要特点
聚合物电解质膜或质子交换膜 (PEM) 水电解是当代发展的技术。在这种电解中,水在阴极电化学分解为 H2,在阳极分解为氧气,固体质子传导膜将电极隔开。
在电解过程中,水分子的氧化导致在阳极形成氧气和带正电的H离子。外部电源电路促进电子流动,而H离子通过半透质子交换膜移动到阴极。在阴极,这些电子与两个质子重新结合,通过还原过程生成一个 H2分子。产生的H2气体具有99.99%的高纯度。
HTE 尚未商业化,但HTE系统已在实验室规模上开发和演示。HTE 是一种电解方法,其中蒸汽在 650°C 和 1,000°C 之间的温度下分解为 H2和 O2。在电解中,系统效率随着操作温度的升高而提高。可以使用低压蒸汽 (LPS),但效率低于上述温度。如果这种热源是清洁热源——例如地热、太阳能或核能——HTE 产生H2的温室气体 (GHG) 排放量几乎为零。
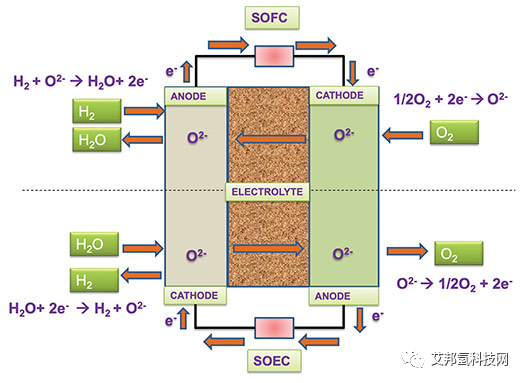
图1. 固体氧化物燃料电池(SOFC)和固体氧化物电解电池(SOEC)的电化学反应。
SOEC 从根本上说是固体氧化物燃料电池 (SOFC) 的反向对应物。参考图1的电化学反应。
二、SOEC详细工艺方案
SOEC H2生产系统的典型流程图如图2所示。该系统旨在通过使用电和水来生产H2。该系统的主要组件包括串联的 SOEC 堆栈和平衡装置 (BOP)。BOP 包括水泵、热交换器、蒸汽发生器等。水在一系列热交换器中被加热,以从 SOEC 出口气流中回收热量。预热水被引入蒸汽发生器产生蒸汽,然后进入电加热器使蒸汽过热。为了最大限度地减少电力需求并提高 SOEC 系统效率,蒸汽在多个热交换器中通过排出的 H2和氧气流进行加热。在外部蒸汽可用的情况下,图2中所示的方案可以进一步优化。
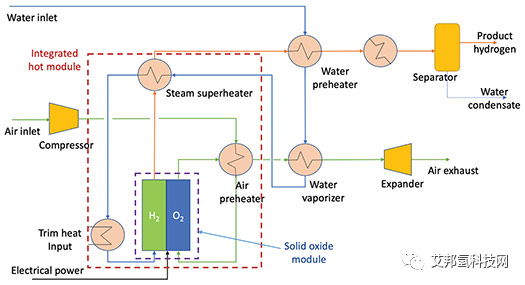
在电解槽中,蒸汽在 650°C–1,000°C 的温度下在阴极分解,形成 H2分子和氧离子(水还原反应)。氧离子从阴极迁移到阳极,释放电子到外电路,通过析氧反应变成氧气。高温热激活氧化物离子迁移并促进两个电极上的电化学反应,提高了整体效率。
-
阴极反应:在 H2电极-电解质界面,蒸汽分解为 H2和氧离子(式 1):
2 H2O + 4 e –→ 2 H2 + 2 O2– (1)
-
阳极反应:氧离子通过陶瓷电解质,在电解质-氧电极界面处被吸入,并产生氧气(方程式 2):
然后氧气沿着阳极流动,而 H2与一些蒸汽混合物一起沿着电解质另一侧的H2电极流动。在电解槽下游,富含 H2的产品流在与入口流进行热交换后被冷却,然后通过分离器将 H2从冷凝水流中分离出来。
一部分产品 H2被回收并与入口蒸汽(蒸汽中5%–10% H2 )混合,以保持还原条件并避免 H2电极中的镍氧化。因此,HT-SOEC 可以在高电流密度下运行,从而允许使用相对较小的电池面积实现大产能。实际上,约 90% 的电-H2效率[在较高热值 (HHV) 的基础上] 似乎是切实可行的。
高温是启动过程中热源的关注点之一。为了克服这个问题,自加热(通过电力)备用 SOEC 可能会有所帮助。由于电池提供电力的同时,电阻会发生焦耳热效应,使电池保持在相对较热的状态,并使其在启动期间更容易使用备用 SOEC。相反,可能需要来自外部源的H2以在待机模式期间将阴极保持在还原条件下。
预热空气或蒸汽可用作吹扫气体以从烟囱中去除氧气。吹扫气体的目的是稀释氧气浓度,从而减少氧气处理组件的腐蚀。纯氧可以通过电池堆产生,如果可以开发出令人满意的材料和涂层来构建氧气处理组件,这将是一种有价值的商品。
SOEC 使用固体离子传导陶瓷作为电解质,能够在明显更高的温度下运行。潜在优势包括电效率高、材料成本低以及可选择以燃料电池的反向模式或共电解模式将水蒸汽 (H2O) 和 CO2 生产合成气 [一氧化碳 (CO)和H2 ] 。
一个关键的挑战是由于高工作温度导致严重的材料降解。目前的研究重点是稳定现有的组件材料、开发新材料以及将工作温度降低至 500°C–700°C(从 650°C–1,000°C),以实现该技术的商业化。甚至 LPS 也可用于增强商业化。此外,将温度降低到 500°C 以下,以及将 SOEC 与高温工艺(如常规重整等)相结合,也可以降低 H2 的综合生产成本。
从整体效率的角度来看,电解系统应该在接近热中性电位的情况下运行。在 SOEC 中,可以以更高的电流密度运行,因此更高的H2生产率是可能的。水的高温电解发生在气相中,因此电解的总能量需求因汽化热而减少。汽化可以通过使用廉价的热能而不是电能来完成。吉布斯生成自由能(用于电解反应)随温度升高而降低——在图3 中可以看出电输入随温度升高而降低。在大约 800°C 的高温下,电力输入比传统电解低约 35%。当温度升高到高达 900°C 时,电力输入可进一步降低至约 50%。
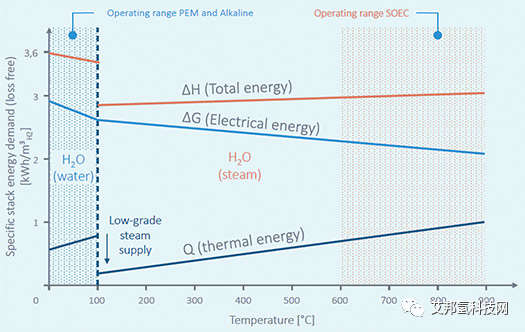
HT-SOE 过程是有利的,因为它在与热集成相结合时具有较高的整体热转化为 H2的效率。
一旦实现汽化,就需要高温使蒸汽过热,以在电解质(蒸汽)中实现足够高的离子电导率。这种额外的热量可以通过结合废热源、回收所产生的 H2和氧气的热量以及电池由于其固有电阻而自加热来提供。
当蒸汽使用外部热源以更高的温度进入电池组时,SOEC 的温度相关效率增益要高得多。为了分解蒸汽,SOEC 在 1.29 V 的热中性电位(吸热电解过程的冷却效果被电池中电阻引起的焦耳热效应所平衡的电位)下运行,将获得约 1.5 A/cm 2 的电解电流密度,而在 1.47 V 的热中性电势下运行的 PEM 电解槽获得的电流密度约为 0.5 A/cm 2。
较低的电池电压意味着较低的运营成本(单位生产气体的电力需求较低),而较高的电流密度意味着较低的成本,因为与低温电解槽相比,需要较少的电解槽来实现所需的气体生产能力。因此,更广泛采用 SOEC 技术的经济动机仍然很高(图 4)。
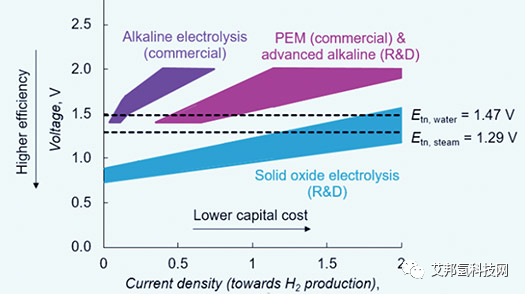
图4. 用于 H2O 分解的 AE、PEM 和 SOE 技术的典型性能范围
在 SOEC 装置中,电化学电池是发生电化学反应的主要电解槽组件。它由三个陶瓷层组成:致密的电解质和位于电解质两侧的两个多孔电极(阴极和阳极,分别产生 H 2和氧气)。考虑到高工作温度范围,电化学电池由陶瓷(固体氧化物膜电解质)制成。例如,Y2 O3-稳定的ZrO2[氧化钇稳定氧化锆 (YSZ)] 用作气体分离器和电解质。它用于在施加电压时氧离子开始从阴极迁移到阳极的地方,在高温下表现出优异的离子电导率。
电极必须既能传导电子又能传导氧化物离子,并且活性表面积最大化对于高效运行至关重要。对于 H2电极,通常使用孔隙率约为 30% 的镍和 YSZ 金属陶瓷(陶瓷和金属的组合),而氧电极则使用亚锰酸镧锶 (LSM)-YSZ 混合物。不同层的材料如图5B所示。
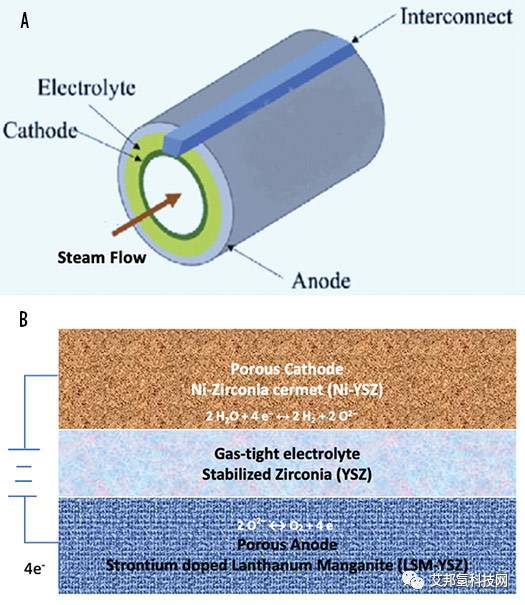
图5 SOEC 配置示意图:(A) 管状 SOEC 和 (B) 平面 SOEC
常用的SOEC材料是地球上储量丰富的材料,如氧化钇、氧化锆等。在燃料电池模式下提供 1 TW 功率的固体氧化物电池仅需要 1 个月的全球 ZrO2产量和 21 个月 的 Y2 O3 。相比之下,PEM 燃料电池系统提供相同的功率需要 53 个月的全球铂产量。
单电池是SOEC的最小单元,可以是管状结构,也可以是平面结构,如图5所示。在管状 SOEC 中,蒸汽通过管内输送并还原为 H2气体和氧离子。氧气从管状 SOEC 的外层提取。
与平面 SOEC 相比,管状 SOEC 具有更高的机械强度并且便于密封。管状 SOEC 与平面配置相比具有高压操作的特定优势,尽管互连器设计是一个挑战(图 5)。虽然阳极室和阴极室之间的密封长度更大,但平面电池具有更好的可制造性和更高的电化学性能。
由于平面 SOEC 上气体种类的均匀分布,以及平面电池更容易大规模生产,平面 SOEC 系统的性能优于管状系统——平面 SOEC 系统配置具有优势,应进一步研究。
表 2 平面和管状 SOEC 的设计特征
为提高生产率,应增加电解槽的活性面积。通过增加单电池尺寸增加活性面积具有挑战性;因此通常是将许多单电池连接起来构建一个堆栈。除电池外,堆栈由金属互连、玻璃密封、流动通道等组成。多个堆栈构建一个模块,多个模块构建所需区域的 SOE 系统以实现所需的生产率。
如图 6说明了从电池级到工厂级的典型 SOEC 系统配置。
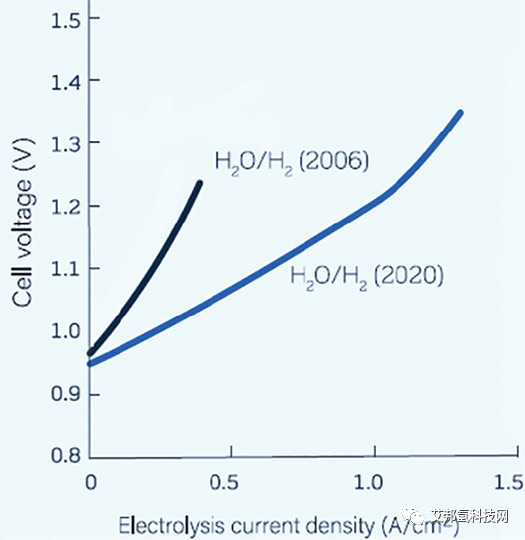
三、SOEC 的挑战和进展
需要进一步改进的 SOEC 技术的主要挑战仍然是电极(特别是 H2电极)的寿命,这受到退化和电池的长期性能的限制。
电池退化的主要原因之一是杂质的影响。在 H2电极中,含二氧化硅的杂质会阻塞非导电相的电催化活性位点,从而导致降解并增加极化电阻。如果保持堆栈入口气体的质量,电池退化会减少。
对于在高过电位 (~300 mV) 下长期运行的H2电极,最接近电解质的渗透镍 (Ni) 网络易被破坏。Ni从电解质电极界面迁移到支撑层,导致不可逆的电化学性能损失。为了改进 SOEC,必须解决这个问题。
高温也是与不同层之间的热膨胀不匹配以及电池中材料层之间的扩散相关的主要挑战。降低电池组工作温度可最大限度地减少互连腐蚀和不同电池组组件之间的反应。
挑战也存在于加压操作中。低压 SOE 操作的优点是使用容易获得的低压蒸汽,其温度比高压蒸汽低。相反,加压操作可以提供几个好处(例如,加压可以增加电池功率密度并减小辅助组件的尺寸)。制造技术的发展和组装大面积电池可以降低商业工厂的总体成本。
SOEC 领域的发展仍在继续。本文讨论了 SOEC 迈向持久未来的一些进展。
(1)电池层面改进:蒸汽电解中记录的电流-电压曲线表明,SOEC 的初始性能在过去 15 年中提高了 2.5 倍以上(图 7),这是由于在 750°C的面积比电阻从 0.71 ohm.cm2下降至 0.27 ohm.cm2。这是通过改进电池层处理等实现的,尤其是 H2电极。
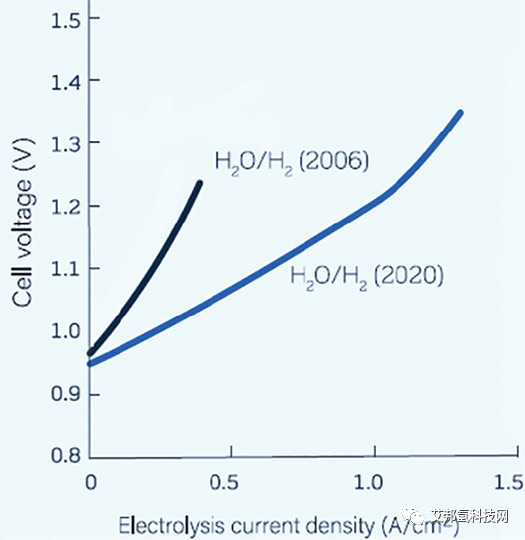
图7 电池单元级改进;2006 年和 2020 年制造的电池在 750°C 下的电流-电压曲线,测量条件H2O/H2 = 1。
在 10 年的时间内,电池降解率往往会随着时间的推移降低 100 倍。从 2005 年到 2015 年,在 1 A/cm 2的电流密度下进行的电池测试(所有电池均由 Ni-YSZ 电极支撑且活性面积为16cm2)发现长期降解率从 ~ 40%/1,000 小时至 ~0.4%/1,000 小时用于蒸汽电解。而碱性电解槽的降解率为1%每 10,000 小时 ——要达到这一水平,SOEC 需要进行更多改进。
SOEC 堆栈性能由电池和其他堆栈组件的性能决定。在高温影响下长期运行过程中,各组分的性能会发生变化。如图 8显示了 2009-2019 年堆栈性能的改进。对于蒸汽电解,2009 年测试的电池堆寿命限制在 < 4 个月,而 2019 年通过实验证明电池堆寿命接近 2.5 年。这主要是由于电池堆耐久性的提高——SOEC 电池堆现在不太容易突然出现性能失败且退化的速度较慢。
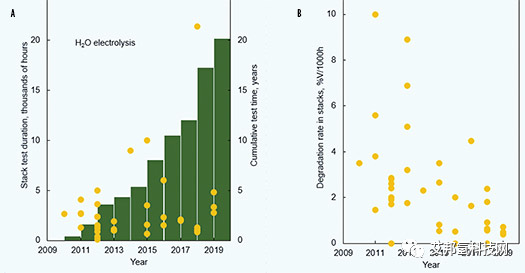
图8. 随着时间推移的堆栈发展:(A) 自 2009 年以来的堆栈测试持续时间, (B) 相应的退化率。
集成 SOEC 和热回收单元仍然是一个挑战。此外,设计优化还必须考虑整个工厂的效率和成本。在下一节中,将讨论潜在的集成方案。
四、SOEC 热能与废热源的集成
SOEC 的运行效率很高,尤其是在使用高温废热的情况下。水的电化学转化允许以产生 H2的形式储存热量和电力。SOECs生产的绿色H2可以进一步加工成合成天然气、甲醇、绿色氨等,并与广泛的放热化学合成热集成,从而进一步提高效率。热集成也可以与核反应堆、燃煤发电厂、生物质、生活垃圾焚烧炉等能源结合使用。这里讨论了其中的一些方案。
1、SOEC 与柴油发动机的热集成。对于柴油发动机来说,废气是一种高级废热,其温度可超过 500°C。因此,如果将柴油机作为热回收蒸汽发生器(HRSG)与SOEC系统集成,将显着降低SOEC的功耗。
2、耦合 SOEC 和氨 (NH3 ) 生产工厂。NH3合成是在较高温度和压力下的放热化学反应(图9),大量热量可用于植物能量平衡中的回收。如果与适量的氮混合,产生的H2可用作NH3生产的进料(式3)。
1/2N2+ 3/2H2 → NH3
∆H298K = –45.7 kJ/ mol(在标准条件下) (3)
通过在高压 (150 bar–200 bar) 和高温 (300°C–500°C) 下运行的 Haber-Bosch 工艺,系统可以与SOE 和 NH3工厂集成。合成每摩尔氨气需要1.5摩尔的H2,氨反应可以提供电解反应所需的大量热能。
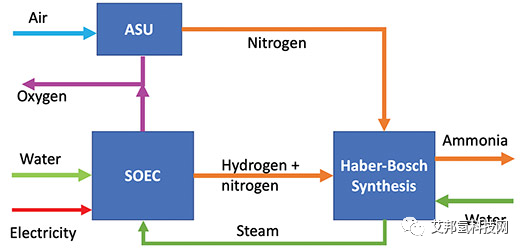
放热的甲烷化反应的热量可全部用于蒸发工艺用水以进行电解。
甲烷化反应将 H2与 CO 或 CO2催化成甲烷 [合成天然气 (SNG)] 和水(式 4 和 5)。
CO + 3H2→ CH4 + H2O
∆H 298K = –206 kJ/ mol (4)
CO2+ 4H2 → CH4 + 2 H2O
∆H 298K = –165 kJ/ mol (5)
甲烷化的放热反应热、甲烷化后产物流的冷却和过电压产生的热量(放热操作)大于气化和预热反应物水所需的热量。因此,通过耦合高温电解和甲烷化来实现高效率(图10)。
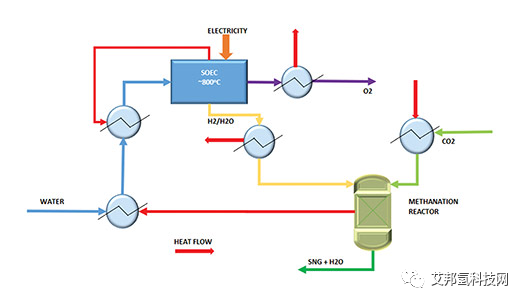
SOECs可以可逆地运行,实现电能和化学能之间的高效循环转换,并提供长期和大容量的储能。在燃料电池模式操作中,电是通过氧化燃料产生的。在SOEC模式下,电力产生H2、合成气等。
正在开发直接生产除绿色 H2以外的特种化学品和商业化学品。例如,可以使用高温 SOEC 通过H2O 和 O 2的共电解生产合成气。然后,合成气可以通过随后的具有不同 H2 : CO 比率的催化反应转化为多种化学品。SOEC 还能够将 CO2分解为 CO 和 O2。将空气和蒸汽送入电解槽的 SOEC 氨生产正在开发中,目前产量非常低。然而,氨可以在 SOFC 模式下用作燃料用于海洋应用——这也在开发中。这种操作的多功能性使 SOEC 优于其他电解操作模式。
实现净零排放目标要求能源行业的运营方式发生重大变化,我们正在见证这一方向的发展。现在人们普遍认为,H2分子有潜力实现能源行业的深度脱碳,前提是能够以更可持续和更具成本效益的方式生产 H2 。
全球对于如何实现1 美元/公斤的绿色 H2成本意见不一。我们知道,可再生能源的成本在绿色 H2的总体生产成本中发挥着重要作用,尽管电解槽技术是主要障碍之一。全球正在宣布多个绿色 H2项目。碱性电解槽(AE)在容量方面处于领先地位,这一点已被充分证明并且具有价格竞争力,其次是 PEM 电解槽技术。固体氧化物电解槽处于小规模示范水平。在电池、堆栈和系统级别的进步推动下,这些技术取得了巨大的进展。
与其他经商业验证的技术(例如 AE 和 PEME)相比,SOE 技术的一些特定功能使其独一无二。例如,SOEC 的工作温度为 700°C 至 850°C,热力学水分解反应在如此高温下的吉布斯自由能 (ΔG)较低,从而使该过程非常高效。此外,集成外部废热源(如工业来源的低压蒸汽)有助于降低电力需求,具体取决于供应温度。除了绿色 H2生产外,同样的技术还可以应用于直接生产氨、甲醇、SNG 等最终产品的各种其他工艺。
由于工作温度高,主要电解槽部件,如电解质和电极,由陶瓷材料制成。这些 SOEC 材料在地球上储量丰富,因此扩大规模不会对材料可用性构成任何挑战。此外,SOEC 具有在可逆操作中工作的可能性,单个单元可以同时进行能量存储和发电,从而允许一个完整的绿色发电厂实现零能耗建筑和碳中和目标。
商用SOEC电解槽为千瓦级,大于3兆瓦的示范机组正在执行中。要充分发挥 SOEC 技术的潜力,必须证明在较高电流密度下电池退化水平要低得多。此外,要实现商业规模化,还需要在制造和组装电池方面做进一步的工作,以降低总体成本。
来源:https://h2-tech.com/articles/2022/q4-2022/special-focus-future-of-hydrogen-energy/solid-oxide-electrolysis-cell-soec-potential-technology-for-low-cost-green-h-sub-2-sub/
艾邦综合整理
原文始发于微信公众号(艾邦氢科技网):固体氧化物电解槽 (SOEC)技术与前进展望