说明:本文编译来自本田的技术论文!
图1:本田原创智能氢站的概念
一、简介
图2为差压式水电解示意图。高压下的水电解反应与常压下相同,是利用质子交换膜(PEM)进行的水电解反应。此外,电化学氢气增压方法的工作原理是只将阴极设置为高压,以获得高压氢气。因此,与使用机械压缩机的方法不同,氢气增压过程中没有振动噪声和电机旋转噪声,实现了极好的安静性,也没有摩擦损失和电机损失,提高了效率。然而,电堆结构应同时满足电化学反应器和高压氢气容器的功能,因此密封结构是必要的,以防止气体泄漏。同时,结构应具有不妨碍水电解反应的供水性能和排气性能。在35MPa的压差式电解水的研究过程中,建立了一种满足电解水性能、压差维持性能和外部密封性能的结构。如下:
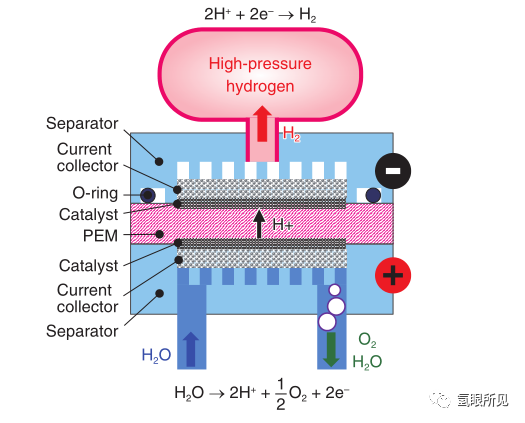
图2:高压差水电解概述
一般开发的目标通常是实现压差约为12兆帕的差压式水电解,通过不使用机械压缩机的差压水电解获得70兆帕的氢气,目前还没有已知的报道。本内容研究了一种实现70MPa差压式水电解的结构,并利用该结构制作了一个实际的电解堆,并对其性能进行了评估。
1、压差维持机理的认识
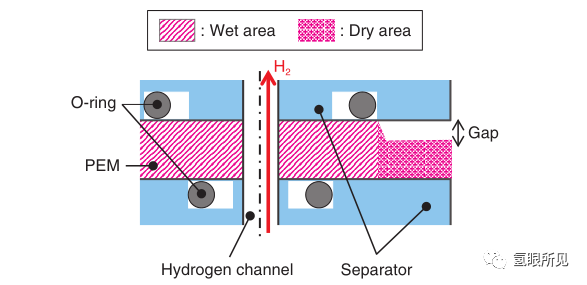
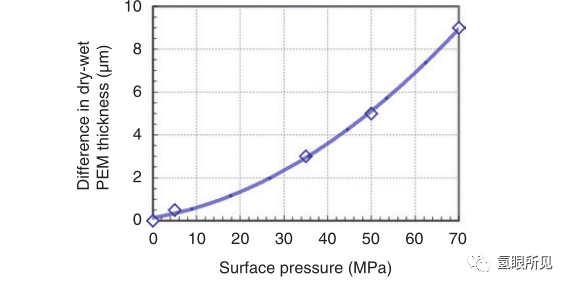
1、PEM最小厚度的理解方法
图6显示了用于研究70MPa耐压结构的单元的横截面视图。如上所述,该结构在电堆中心有氢通道,集电器支撑PEM, o型圈提供密封功能。通过活塞内部的弹簧对电堆施加恒定的表面压力,整个电堆按照高压氢气容器的设计准则制造。试验中使用的氮气使用气体增压压缩机逐级加压,经证实可以承受高达70 MPa的压力。此外,还确认了提供密封性能的o形圈和集电流部件是否有损坏。耐压测试的测试温度设置为80°C,并通过在电堆内循环热水来维持该温度。测试中使用的PEM厚度从200µm开始逐步减小,以确定可以维持压差的最小膜厚度。基于这些结果,在不同膜厚度的位置观察了测试后PEM的横截面,以检验能够维持压差的机理。
2、结构耐久性实验
图7显示了70MPa电池结构耐久性试验中使用的评价体系。压力循环测试以1000次循环为耐久模式,重复加压至最高85MPa,然后减压至常压。原因是目前在日本验证的太阳能氢气站每年启停大约100次,因此目标被设置为10年的启停次数。测试介质为不可压缩的水,测试使用具有足够耐压的空气驱动液压泵进行,以便更容易检查泄漏并缩短耐久性测试。通过事先调节压力调节器和流量调节器的阀门输出,并通过计时器打开和关闭电磁阀来实现增压和减压。此外,从安全角度考虑,在高压过滤器之前、压力调节器之后分别安装了溢流阀。耐久性测试温度设置为电堆最高工作温度65℃。通过上述氮气密封试验(25°C, 70MPa)评估电池结构耐久性。采用换水法采集高压侧到对侧的氮渗透量,通过耐久性试验前后的对比来判断耐久性。
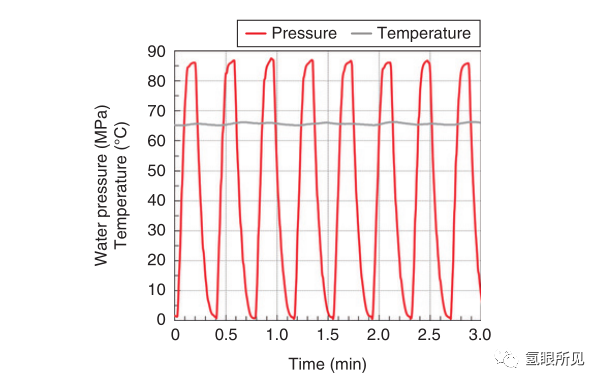
1.压差维持机理及所需膜厚度
图8显示了不同PEM厚度下压差维持性能的差异。在膜厚度为60µm或更大时,可以维持70MPa的压差,但在50µm时,膜在达到70MPa后4分钟破裂,在30µm时膜在达到50MPa后立即破裂。此外,在膜厚度为60µm的测试后,发现PEM、O形环或集电器没有损坏,并且中心具有高压氢通道的结构可以同时满足压差维持和密封结构功能。
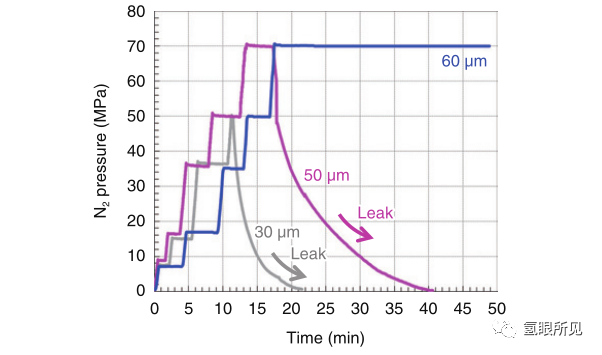
上述试验结束后,观察各膜厚度下的膜截面。图9为压差维持条件和破膜条件示意图。这说明在膜破裂的情况下,整个膜相对于集电孔处于拉伸状态,而在膜厚度维持压差的情况下,膜相对于集电孔保持压缩状态。这表明,为了确保在70MPa下的耐久性,必须确定维持压差所需的最小膜厚度,以及由于集电器孔处的变形和压缩蠕变而使膜厚度减小的量。因此,通过将孔隙体积转换为膜厚度,可获得PEM对孔隙的变形,计算结果为20µm。此外,通过单独获得PEM的特性来确定PEM压缩蠕变,发现应大约为20µm。这些结果表明,100µm或以上的PEM厚度满足耐久性要求。
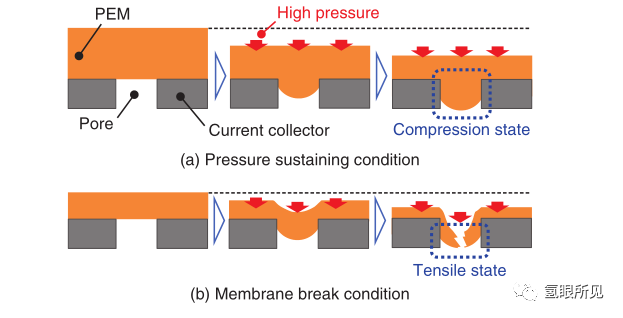
2、结构耐久性实验结果
图10为水压上升和降低耐久性试验的温度和压力分布图。压力上升和降低测试进行了1000次循环,每循环大约25秒。
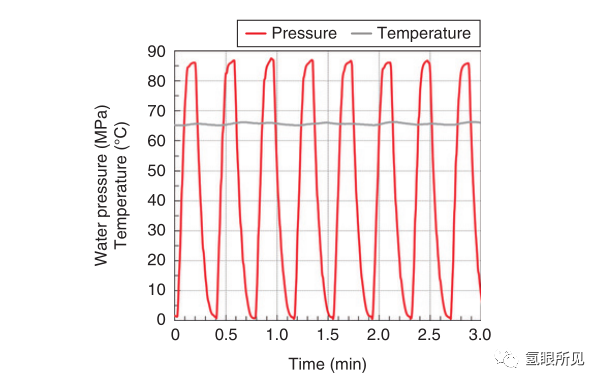
表1比较了水压循环试验开始时和70MPa密封试验1000次后对侧氮气渗透量。耐久性试验前后氮渗透量无差异,证明该结构在压差维持和密封结构性能方面均能承受较长时间的使用。此外,在耐久性测试后,PEM、o形圈或集流器均无损坏,这也证实了部件的耐久性。
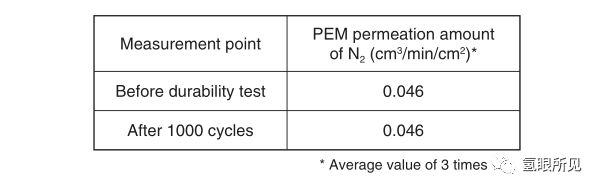
1、性能评估项目
在70MPa堆中,需要确认改变电解槽结构是否会影响电解性能。因此,通过对比高压水电解过程中电解电压与常规35MPa叠层电解电压的差异来验证这一点。此外,对比了现有70MPa制氢站所消耗的压缩机功率和高压水电解所需的增压能量,验证了差压水电解的优势。
同时,使用70MPa高压水电解产生的氢作为氢燃料汽车氢燃料,氢的质量应符合SAE J2719和ISO 14687-2的规定,水的浓度应小于5ppm。在水电解反应中,水伴随着质子在PEM内移动,因此产生的氢中总是含有一些水。在后续过程中去除氢中所含的水所需的能量可以通过定量确定这个水量来估计,因此这对系统设计很重要。因此,在制造的70MPa堆中测量高压水电解法产生的氢气中所含的水量。
2.堆栈性能评估方法
实验使用的PEM膜厚度为100 μ m,采用Ru-Ir络合氧化物催化剂作为阳极催化剂,铂黑作为阴极催化剂。这些催化剂被热压到PEM的两个表面,以制造测试中使用的堆栈。图11显示了用于评估制造的70MPa差压式电解堆性能的评估系统。在高压水电解期间从相对电极渗透的氢包含在氧侧,因此出于氢安全的原因,通过在氧-水分离器处用氮气稀释并用氢传感器测量以确保氢浓度足够低来进行测试。
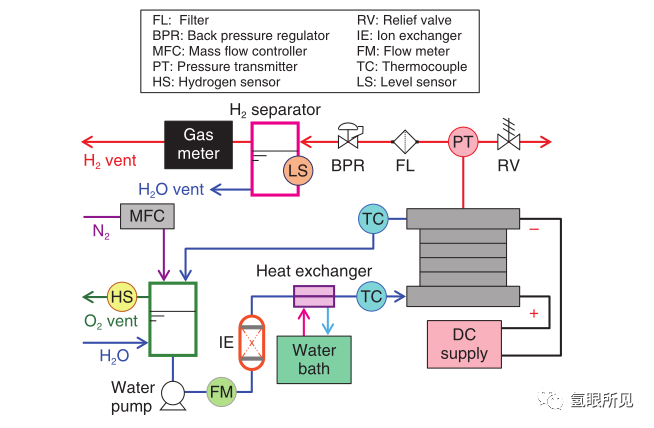
测试条件通过通过烟囱的循环水的温度将温度调整到电解堆的工作温度60°C。水质为纯水,电流密度设置为1.2A/cm2。通过将电解压力提高到70MPa所需的电解电压计算值与实测值进行比较,并在每个压力下进行不同电流值的I-V测量,比较不同压力下的电池电压,从而评估电池组性能。此外,使用背压调节器将压力降低到常压后,使用湿气流量计测量产生的氢气量。将高压水电解过程中高压氢侧氢水分离器的水位上升速率与生成氢中所含饱和蒸汽量相加,得到高压水电解过程中高压氢侧渗透水量。
3、堆栈性能评估结果
将上述涉及维持压差性能、密封性能和电解性能的技术用于制造一台70MPa的压差电解堆。图12显示了外观的照片。
图12:70兆帕差压水电解堆照片
图13显示了将压力提高到70MPa所需的电解电压与传统35MPa堆栈的电解电压的对比图。这些结果清楚地表明,高达35MPa的压力曲线与迄今为止的报道相符。这表明,70MPa和传统35MPa电堆之间电池结构的变化对水电解性能没有不利影响。
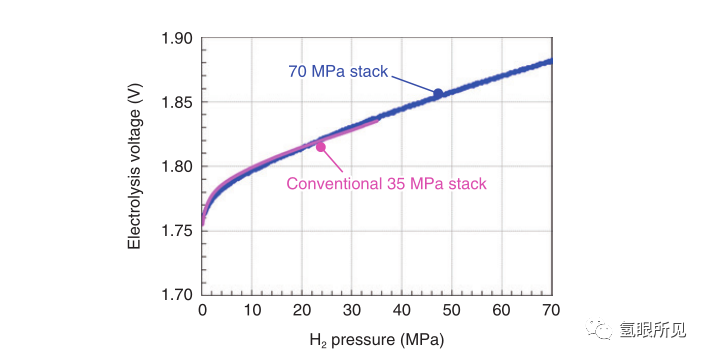
图23:70 MPa叠加与常规35 MPa叠加氢压缩曲线(60℃,1.2 A/cm2)
此外,表2:
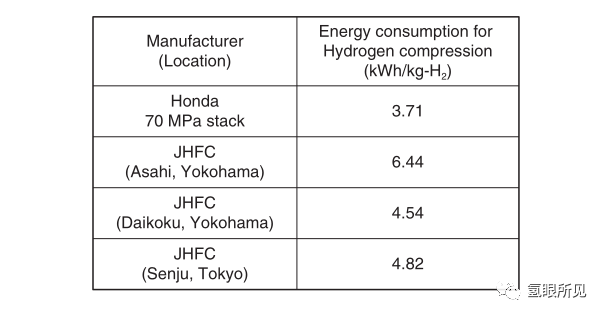
将式(1)中ir为零时高压水电解所需电解电压EWE的实测值与计算值进行了比较。之所以实测值比计算值大42mV,假设是由于PEM高度压缩时,PEM电阻上升导致直流电阻分量增大。

基于这些结果,表3:
比较了将1kg氢气压缩至70MPa所需的功率与现有氢气站的功率。这些结果表明,压差水电解所需的氢加压能量小于任何当前运行的氢站,并且与机械压缩机所消耗的功率量相比,功耗可减少约30%。
图14显示了在每个压力下进行I-V测量,并使用下面的公式(2):
获得电压效率(HHV转换)得到的图形。70MPa时的I-V斜率大于35MPa时的I-V斜率,这是由于随着PEM电阻的增加,直流电阻分量[Eq.(1)中的ir项]增加。结果表明,在70MPa和1.2 A /cm2时,获得的电压效率为78%。这低于35MPa时81%的电压效率,但也高于最初预测的75%,因此获得了好于预期的效率。
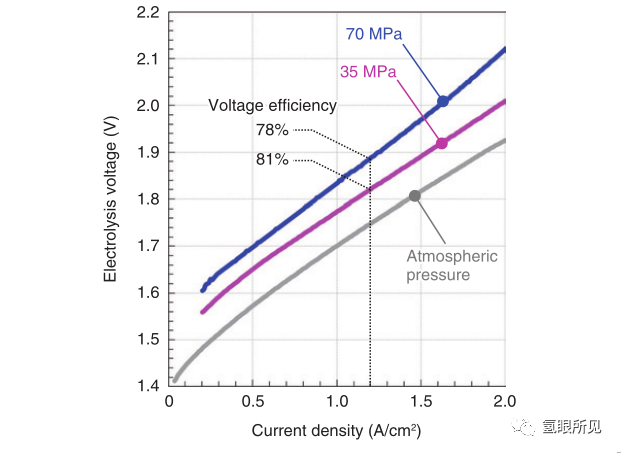
图14:H2压力对I-V曲线的影响(60℃)
图15显示了压力对电流效率的转变。
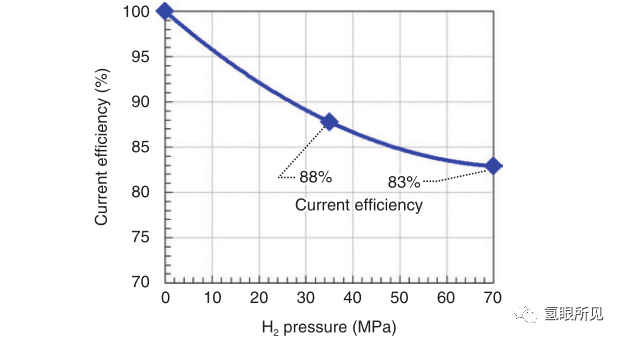
图15:H2压力对电流效率的影响(60°C, 1.2 A/cm2)
电流效率表示相对于供应电流产生氢气的速率,由式(3):

ηA:电流效率[%]
Q:产氢量[mol/hr]
IWE:电解电流[A]
计算得出。发现电流效率随着压力的增加而降低,但在35MPa或更高的压力下下降的速率减小。电流效率最初被认为与压力成反比降低,因此假设为75%,但结果表明,在70MPa时,电流效率达到83%。
图16显示了高压阴极的渗透水量与压力的关系。这表明,随着压力的增加,水量减少,在70MPa时比35MPa时少60%,比常压时少90%。这表明所产生的氢气的水含量降低,这表明高压氢气-水分离器的内部体积可以减少,并且除湿所需的能量与35MPa时相比也可以减少。这为进一步简化系统提供了可能性。
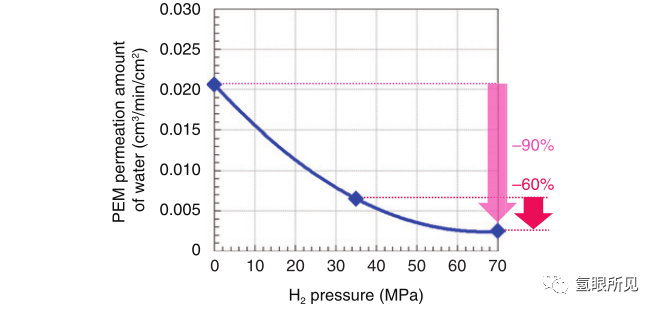
研究了70MPa差压电解堆的耐压结构,并对该结构进行了耐久性试验。因此,得到以下结论。
(1)确定了能承受70MPa压差的膜厚度极限,阐明了PEM能承受压差的机理。
(2) 70MPa电解堆使用的中心带有高压氢通道的密封结构被证明具有相当于10年运行的耐久性。
结合上述技术,研制了一台70 MPa的差压电解水堆,并对其性能进行了验证。得到了以下结果。
(1)与使用机械压缩机的现有氢气站相比,使用70MPa差压水电解法成功地将产生压缩到70MPa的氢气所需的电力降低了约30%。
(2)产生的70MPa氢气的含水量比35MPa氢气的含水量低60%,因此除湿所需的能量减少,为进一步简化系统提供了可能性。
原文始发于微信公众号(氢眼所见):70MPa差压式PEM电解水电堆的研制
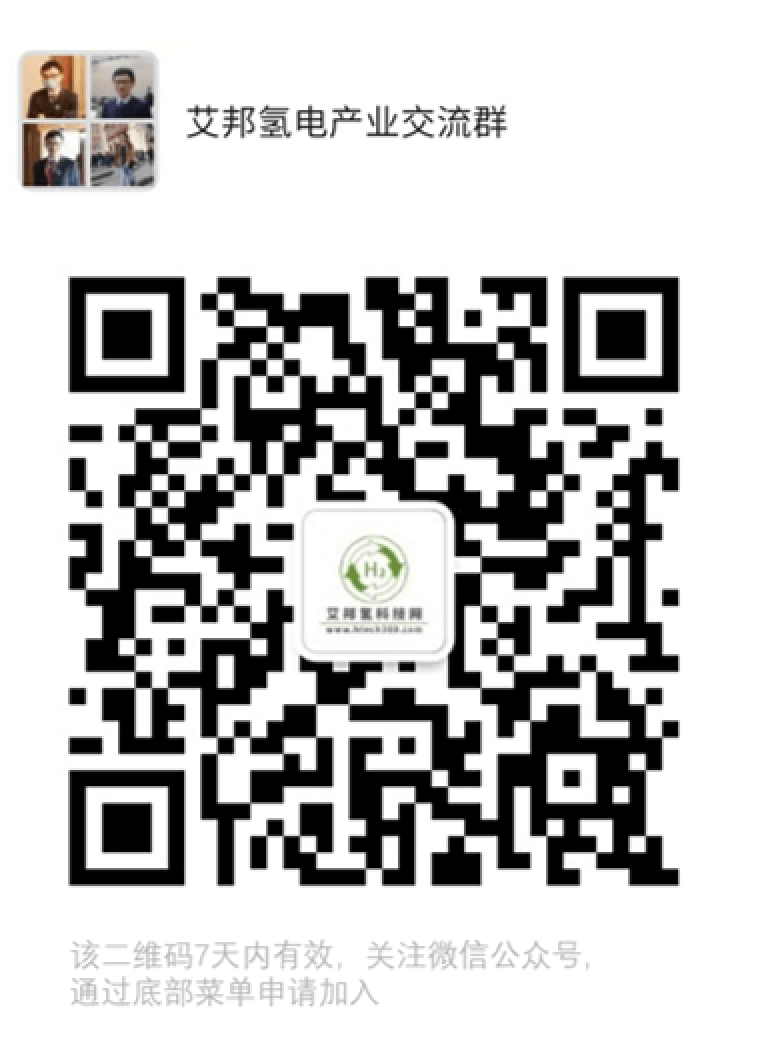
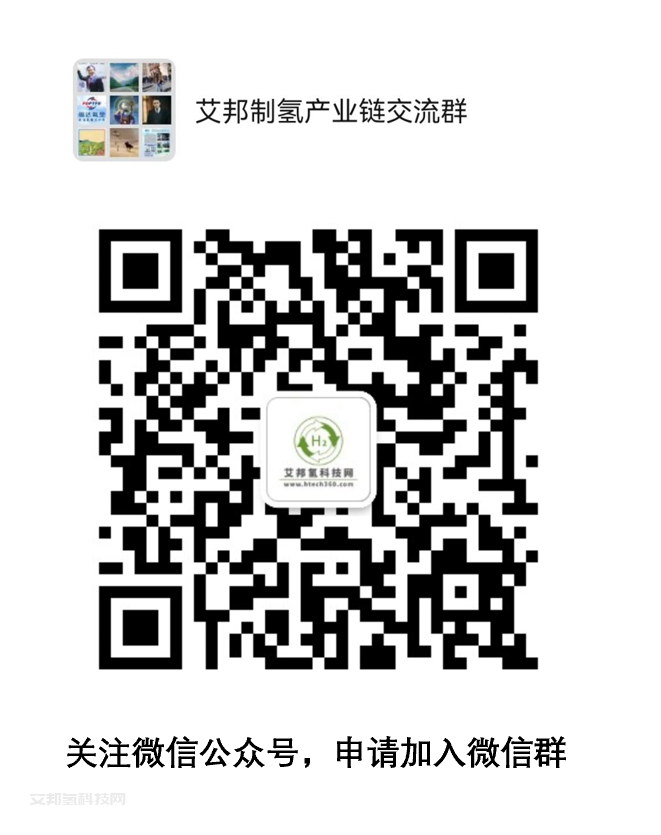