双极板是燃料电池电堆最主要的结构支撑件,其结构设计形成了电堆内部的氢气、空气和水的流动通道。作为电堆主要结构件,双极板的厚度直接影响到电堆的功率密度,目前行业内由于膜电极技术门槛相对较高,取得突破性进展缓慢,电堆产品性能提升的发力点还主要集中在双极板上。
燃料电池双极板必须满足如下性能要求:
- 结构上要起到单电池串联作用,双极板必须有较高电导率;
- 要隔离各个形腔的反应气体及散热水,双极板气体渗透率需要满足要求;
- 将反应区域的热量快速传递到冷却液中,双极板要有较高的热导率;
- 考虑到结构强度、振动、功率密度及低温启动,双极板材料的强度、密度、热容也要满足产品性能要求。
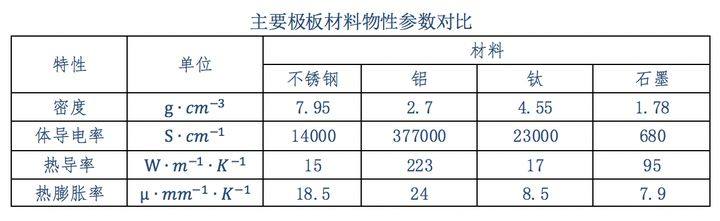
金属材料的导电率和导电率较高,阻气率以及材料强度较高,适合做更薄的极板,但材料容易腐蚀,需要专门的涂层工艺。石墨极板相对厚度较大,但材料较为稳定,在耐久性方面有一定优势。
1 满足活性面积要求
双极板的设计首先要考虑满足电堆功率的活性面积要求,如下图左侧红框发电区域所示,活性面积区域的选择和电堆均匀配气区域和均匀温度分布区域的位置密切相关,否则会对电堆耐久性产生影响。目前燃料电池功率需求不断增大,膜电极活性面积要求越来越大,增大面积的同时要考虑模压及冲压等工艺能否满足大面积极板的加工要求。

2 考虑各方面公差
此外在极板设计时要充分考虑双极板、膜电极和密封线的尺寸公差、形位公差以及装配过程的配合公差,合理的公差设计才能保障产品的可靠性、一致性与耐久性。如下图所示为双极板、密封线和膜电极的配合截面,该配合区域的合理设计对装配性能、干湿耐久性以及活性区域占比有着重要的影响。

3 材料特性与成型工艺
双极板设计过程要充分考虑材料特性与成型工艺,石墨极板强度相比金属板强度较低、气体渗透率较高,因此在极板厚度上要有安全裕量,目前一般雕刻石墨板板材最薄处至少保留0.3mm厚度,模压板材料厚度会再薄一点。如下图所示,左侧石墨板流道底部间有较厚的材料间隔距离,而右侧金属板成型时,氢气和空气形腔的另一侧组合成水路通道,而且极板仅0.1mm厚,比石墨双极板单电池要薄。
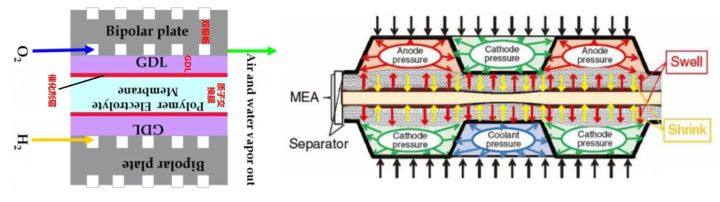
4 配气口和结构强度设计
在极板配气入口处入口设计时,金属板有如下两种方式:
一种在阴极和阳极板间需有配气隔板,结构相对复杂,丰田金属板热压橡胶内部就有用于隔离气体的隔板结构;另一种方式就是呈Z字型的配气结构,虽然会增加密封区域宽度,但整体结构简单。
石墨双极板则使用穿孔的方式,利用阳极板和阴极板配合形成配气口,结构相对简单,这里不做图示说明。
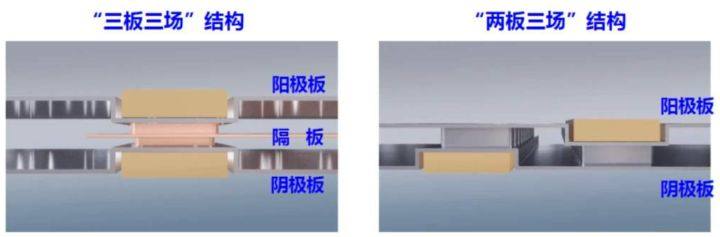
电堆最大功率需要有与其匹配的配气口设计、结构强度设计,配气口面积会影响到电池装配数量的上限,极板结构设计对电堆装配后各个方向的强度,此外气体流动方向、电堆放置方向、过程工艺孔位、巡检取电、取电板取电等因素在设计阶段都要都考虑。不同厂家金属双极板,有三路介质进出口在同一侧的设计,也有出于其它需求的不同设计方案。

5 流场介质均匀分配
在流场设计方面,空气路、氢气路和水路的设计要保障介质的均匀分配,合理的压降设计要保障不同单池间的均匀分配,尤其在氢气和空气侧还要减少液态水的影响,在流道设计方面还要考虑所匹配的发动机系统以及相对应的工作条件,对此各个厂家的设计都有不同。丰田汽车创新性使用3D流场加强水管理和空气扩散的极板设计如下图所示:
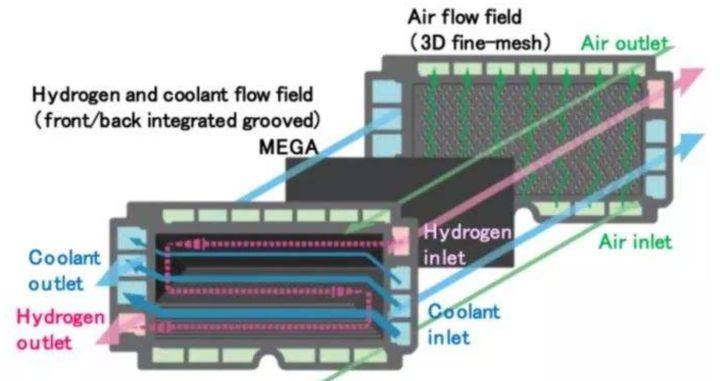
本田汽车改进极板的散热能力和方式,将原有的每节单池散热变为两节单池使用同一散热流场,保障散热能力的同时提升了整电堆的功率密度。
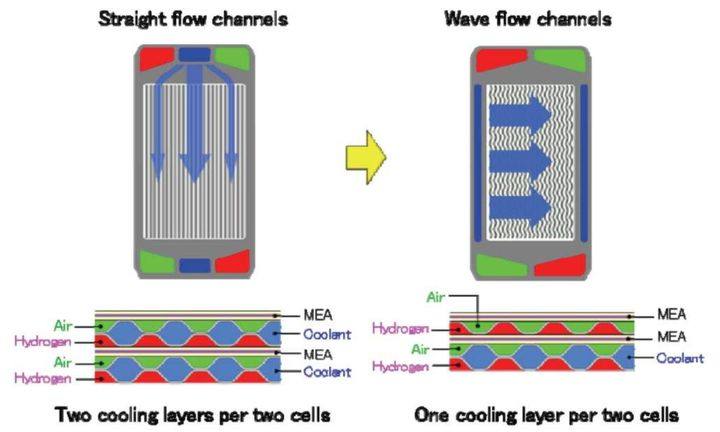
本田汽车在极板之间增加了数值结构,促进反应介质均匀分配,同时改善零部件装配配合性能和极板间的力学性能。
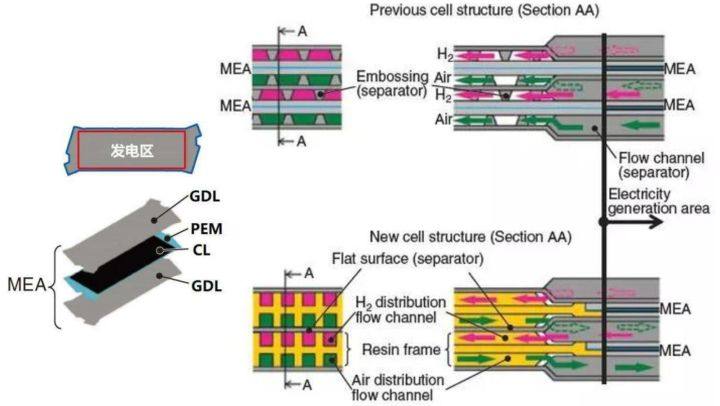
相信在今后随着燃料电池技术的不断进步,会有更多的创新设计涌现出来。
如有工程服务、技术咨询和广告合作需求,请微信关注公众号「氢梯科技」后台私信联系!
往期内容推荐 >>>>
原文始发于:燃料电池双极板设计特点
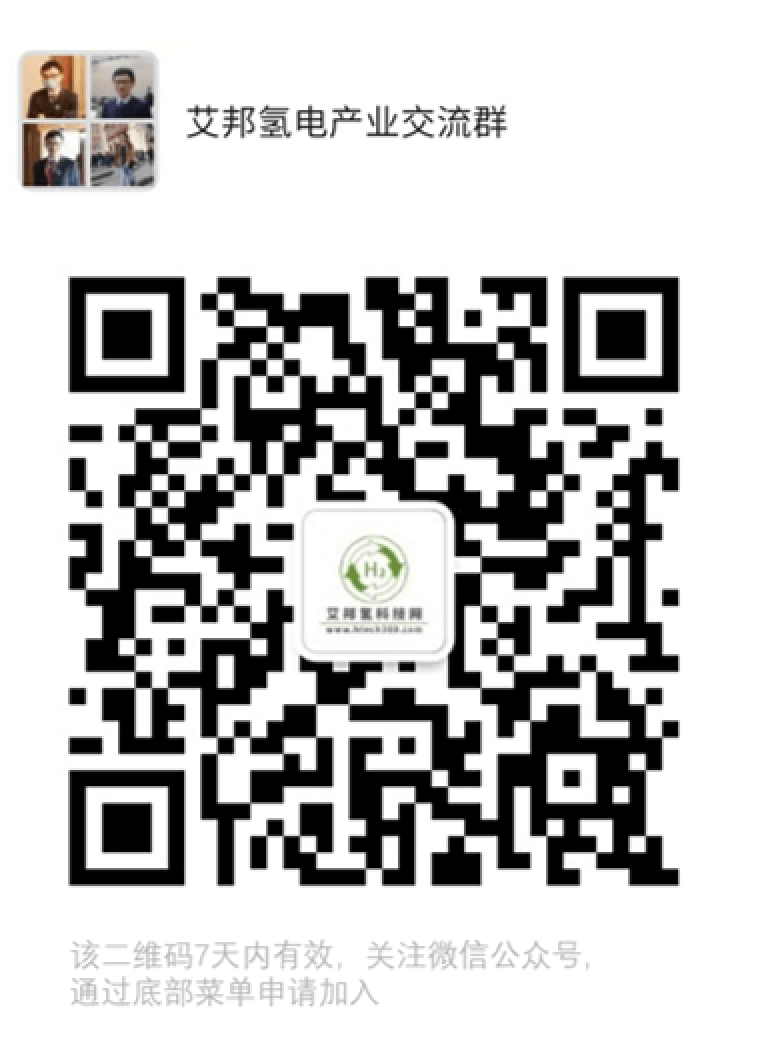