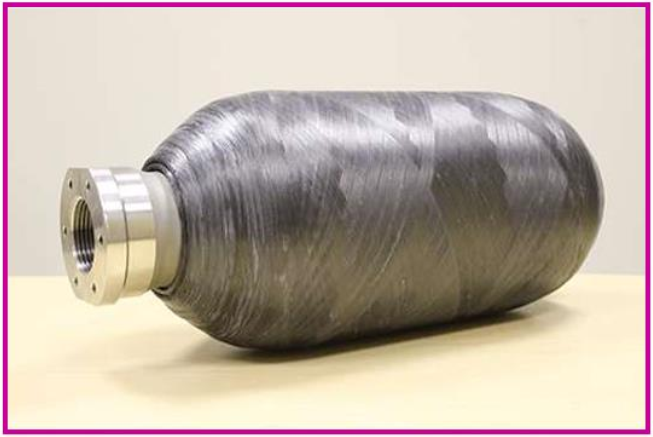
总部位于英国的 DuraStor 和后续主机财团被动员起来,以找到一种安全有效的方式,在高压下储存足够的氢气或天然气,使燃料电池驱动的电动汽车拥有与传统液态石油燃料和内燃机相当的行驶里程。热塑性复合材料提供了一种可能的解决方案。图中所示为碳纤维/乙醛胶带缠绕容器部分缠绕。
DuraStor 团队设计了一个旋转模塑乙醛内衬(图中有四个内衬,每个内衬的气体入口/出口硬件安装在容器底部),该内衬与缠绕的乙醛/碳纤维胶带兼容在从现在到 2025 年逐步实施严格的法规之前,世界上大多数汽车制造商都在争先恐后地提高燃油效率和/或减少温室气体排放。为此,这些原始设备制造商正在减少车辆质量,并探索替代动力系统选项(要全面了解汽车制造商为制造更省油、符合排放标准的车辆所做的努力,请点击右上角“编辑精选”下的“汽车碳纤维布:未来的形状”)。后者中最有趣的是燃料电池。虽然在我们看到广泛部署之前,必须清除主要的技术和后勤障碍,但是燃料电池的汽车(FCV- fuelcell vehicle ) 正在开发中或已经在进行道路测试。燃料电池电动动力装置非常有趣,因为它们最常见的两种燃料——氢气(H2)和压缩天然气(英文称CNG-compressed-natural gas) 的唯一燃烧副产品是水和热,这使得零排放汽车(ZEV- zero-emissions vehicles)成为可能。
最大的障碍之一是氢气燃料储存。几十年来,工业界一直在安全地处理氢气,几乎可以在任何地方从各种投入(生物质、煤炭、地热、水电、核能、太阳能、风能、水电解,甚至 CNG 生产氢气。从成本、能源安全和生命周期分析的角度来看,这种灵活性非常有益。但这种极轻的气体(比空气轻 14 倍)的能量密度(按重量计)是传统液体石油燃料的三倍,但能量(按体积计)要少得多。此外,氢分子是世界上最小的,因此储存容器的抗渗透性成为一个真正的问题,以免燃料泄漏。因此,很难在大多数汽车的小空间内装足够数量的 H2,以复制当今汽油动力汽车每油箱 500 公里的行驶里程,尤其是当目标是在不增加车辆质量的情况下实现这一点时。尽管有替代方案,但最实用、成本最低的车载 H2 储存方法是将工作压力为20-70 MPa 的压缩气体储存在储罐中,储罐必须进行爆破强度为其额定压力两倍的试验。今天氢气储存可使用四种类型的压力容器
I 型(全钢)容器既重又笨重。
II 型储罐(用碳纤维/环氧树脂缠绕的钢或铝内衬)它们更轻,但成本更高。每一个都能承受高达 30MPa 的工作压力,用于散装运输或加油站的固定气体储存。
III 型储罐与 II 型储罐类似,但完全采用碳/环氧复合材料缠绕。它更轻,但成本更高,可承受更高的工作压力(至 82.5 MPa,带有铝内衬),主要用于商用卡车上的 H2 或 CNG 储存。
IV 型储罐采用高密度聚乙烯(HDPE)或完全包裹碳纤维/环氧树脂的橡胶衬里。最轻但最昂贵的是,它们的性能与 III 型坦克相似。不幸的是,某些金属和合金往往会吸收 H2,导致脆化,从而降低油箱的耐久性。混合材料储罐在混合材料界面处容易疲劳,这会限制其使用寿命。此外, 热固性环氧树脂基体使报废回收变得复杂,这对销往欧盟的汽车制造商来说是一个额外的难题。以前可用储罐,储存的燃油太少,无法满足足够的行驶里程,难以回收和/或缺乏足够的耐久性,无法在汽车上大量使用。
2010 年,成立了一个名为低成本、耐用热塑性储氢罐(又叫“DuraStor” )的多合作伙伴、多年研究项目,通过调查 IV 型储氢罐替代品的减少来解决这些问题。DuraStor 的部分资金由 InnovateUK(英国威尔特郡斯温顿)提供,于 2014 年初结束。英国一个名为氢能—存储和传输优化(HOST)的项目在,部分资金由英国技术战略委员会提供,同样的目标和但成员的一些变化。据报道,选择这两个项目的成员不仅是因为他们的技术专长,还因为他们愿意和有能力在研究成果转化为商业产品时形成可行的供应链。在市场研究得出最初的压力容器设计规范后, DuraStor 团队转向材料和工艺。一项专利调查显示,该领域的大多数知识产权涉及热固性复合材料,但一名熟悉廉价热塑性内衬材料抗渗透性的团队成员说服团队对其进行探索,因为它们不仅比金属轻,而且加工速度更快,比热固性材料具有更大的冲击强度和再加工/回收能力。此外,热塑性塑料可以重新熔化,提供了单独生产内衬和外包覆的机会,然后将它们连接起来,形成一个整体式罐,可以避免现有金属/复合材料混合材料中出现的疲劳问题,并促进回收。通过消除除耦合硬件外的所有金属(可以隔离),可以减少或消除氢脆和电偶腐蚀。
“在这些项目的前期工作中,我们与汽车制造商进行了多次讨论,这些制造商显然对燃料电池技术感兴趣,但对当前储氢容器的长期性能缺乏信心,”但项目负责人解释道。“我们的联合体成员相信,热塑性复合材料比热固性塑料具有更好的耐久性。”DuraStor 评估了三种半结晶热塑性树脂(由美国德克萨斯州达拉斯塞拉尼斯联合会成员提供),它们具有良好的机械性能和耐化学和渗透性:聚对苯二甲酸丁二醇酯(polybutylene terephthalate) 、 聚苯硫醚(polyphenylene sulfide)和聚甲醛(POM 或缩醛)(POM, or acetal)。
POM 的选择基于两名团队成员之前的工作,以及其在汽车燃料装卸组件和低压燃料储存中的长期使用历史。衬里应为整洁的 POM,以优化渗透阻力,但必须加强外包层,以最大限度地提高容器的环向强度和耐爆裂和耐穿刺性。该团队选择了连续碳纤维而不是 e 玻璃纤维,因为前者具有更大的重量比强度,并且已经被许多储罐制造商与环氧树脂一起使用。单向胶带被认为是最实用的纤维形式,可确保非常低的空隙率和无干点,这两种材料对抗渗透性都至关重要。工艺选择从空心内衬开始。由于泄漏是不可接受的,该团队希望生产一个整体的内衬,而不是组装内衬。为了管理成本,该过程需要在研究量上成本低廉,并可扩展到汽车生产量。考虑了吹塑、铸造和旋转模塑(旋转模塑)。后者的选择基于其较低的模具成本;其低成型应力(减少模后翘曲);能够生产具有良好表面光洁度和受控壁厚的大型部件;事实上,螺纹可以模压在耦合硬件(允许燃料流入和流出)和嵌件中,可以用来最小化模后加工。尽管旋转模塑循环比大多数其他热塑性成型方法慢,但与其他方法相比,家庭工具和旋转站的使用可以以相对较低的成本增加产量。已经被储罐制造商使用的长丝缠绕将是外层工艺,但该团队可能必须修改缠绕头,以处理预浸热塑性胶带。在掌握材料和工艺的情况下,该团队进行了并行测试项目。一些成员对干净的注塑POM 和真空/高压固化 POM/碳层压板进行了小规模机械试验(根据 ISO 527-3、 ISO 178 和 ASTM D3410M)和渗透试验(根据 ISO 5869)。另一个小组设计了衬套、联轴器硬件和旋转模塑工具。2011 年至 2013 年间,几项衬里设计进行了试验。每批中的一些模制衬里被切割,并接受进一步的机械和渗透测试。重要的是,通过测试旋转
模塑工艺中生产的样品,使用类似但不完全相同的 POM 等级和不同的添加剂包覆,验证初步测试结果的准确性。初步测试结果是在具有 POM 等级和添加剂包覆的注塑样品上进行的。相关性非常好,研究小组得出结论,配方和加工差异不会对聚合物的行为产生负面影响。
初步结果
2014 年, DuraStor 团队关于其 2010-2013 年研究的第一份公开报告表明,只要内衬的标称壁厚足够大, 内衬和外包装材料就满足或超过当前的性能要求≥5 毫米。报告后的工作——一项回收研究、额外的衬垫成型试验和初步的外包装缠绕试验——已经产生了数据,将由主办团队用于确定 UD 胶带的缠绕路径。下一步,研究将集中在通过巩固班轮和外包装生产整体式船舶上。其他计划中的项目包括对纤维缠绕头进行改造,以及开发嵌入式/交钥匙机器人制造单元,使混合容器制造商能够采用 DuraStor 技术。随后, HOST 将在 H2 动力的燃料电池汽车(FCV- fuel-cell vehicle ) (上进行一个真实世界的示范项目,以验证材料和工艺技术,并建立一个完全有能力的供应链。
特纳补充道:“许多处于氢经济前沿的组织都是预算有限的小型创新者”。“这就是为什么我们的机器人制造单元需要设计成能够适应定制和原型组件的原因。我们相信,它将促进氢经济的更快发展。”
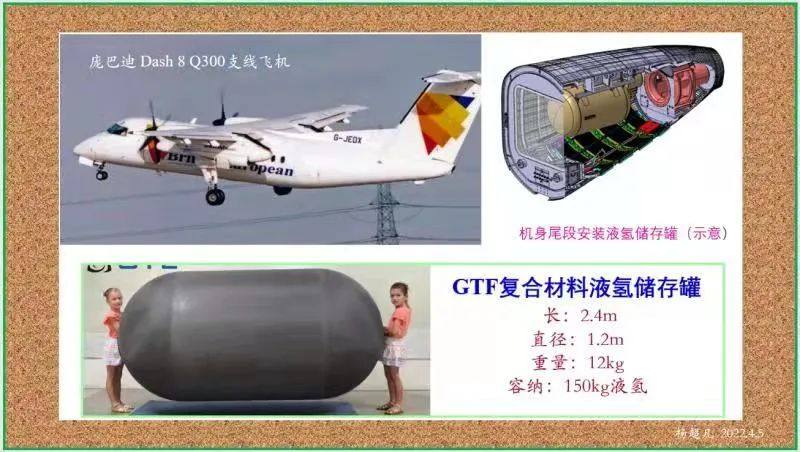
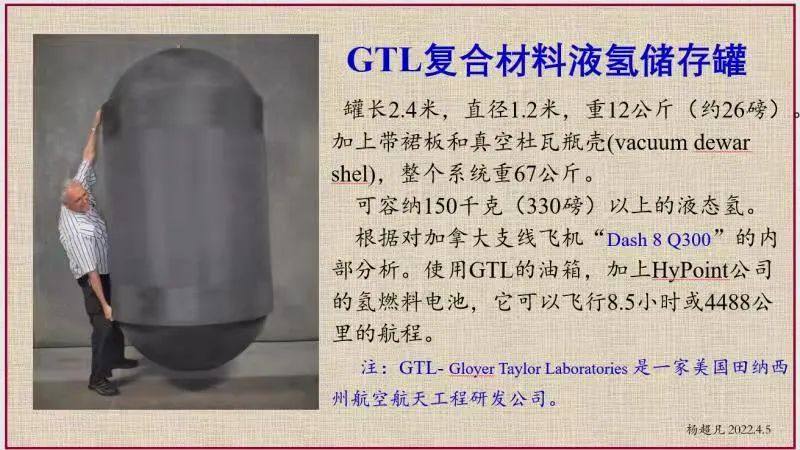
编后语:
此文件是 2015 年 2 月报道的。编译此文件, 一是再次引起对复合材料压力容器的关注。二是注意热塑性复合材料,已经进入这个行业了。三是液氢储存罐的难度远大于此类产品。
杨超凡简介:飞机制造高级专家,近年专攻民机复合材料。原航空工业部首批研究员级高级工程师,享受国务院特殊津贴
原文始发于微信公众号(复材网):专家杨超凡:热塑性复合材料储氢罐的发展及在航空领域的尝试