本文从 PEMEL 结构和制氢机理出发,结合技术优势,回顾了该技术的发展历程和应用现状,综合分析PEMEL的瓶颈问题与未来的应用前景。
长按识别二维码关注公众号,点击下方菜单栏左侧“微信群”,申请加入群聊
一、 PEMEL 电堆结构和电解水制氢机理
双极板是用于支撑集电器与膜电极、传递电子及提供物质传输的通道[11]。气液扩散层作用是在电催化层和双极板之间提供有效的电接触,并确保它们之间的气/液传输。气液扩散层需具备适宜的孔隙率以便于反应物水的传输和生成物气体的移除,以及最佳孔径值来平衡扩散层中的质量传递和电催化层中的电荷传递的竞争过程[12]。液相的水通过阳极多孔层的孔道传递到催化层,而随着反应的进行,氧分子在反应位点以气泡的形式成核积聚在孔道内,可能会引起孔道堵塞阻碍液相水的传递,导致质量传递的损失。
如图 1(b)所示,Zhang 等[15]设计了反应可视化的PEMEL装置,由具备直孔和形态可调节的气液扩散层以及微尺度可视化系统组成。他们通过可视化装置观测到反应优先发生在催化剂层与液体/气体扩散层之间的三相界面上,这表明装载的大多数催化剂未充分发挥作用。因此,改进多孔扩散层的设计不仅提高了质量传递效率并减少了催化剂的浪费,对电解池实现高电流密度操作具有重要价值。
2、PEMEL反应热力学和动力学分析
长按识别二维码关注公众号,点击下方菜单栏左侧“微信群”,申请加入群聊
二、PEMEL常用催化剂及反应机理
尽管催化剂目前并不是电解池最主要的成本因素,但随着其他成本的下降以及对贵金属需求的增加,研发资源丰富、长期稳定和活性优异的电催化剂材料将是实现 PEM 电解池大范围高效应用的重要前提,图 3 展示了目前用于阴极HER 和 阳极OER 反应最新的催化剂。
1、析氧反应催化剂
阳极的 OER 反应是制约电解水性能的瓶颈。OER反应缓慢的动力学引起阳极处过高的电位,从而占据 PEM 电解池中主要的能量损失。
但Ir是地球上最不丰富的贵金属元素之一,不适合大规模生产。因此需要寻找低成本的替代材料,有效地降低 OER 的动力学限制,提高水的分解效率[40]。近年来大量的研究关注于过渡金属氧化物 (TMO) 作为 OER 的高性能电催化剂,由于相对较高的活性,钴基氧化物是研究最广泛的非贵金属催化剂[35],以过渡金属为基底的磷化物、氮化物以及硫化物也已被证明能够被应用于酸性介质中,但这些材料均容易在酸性条件下发生氧化和溶解。而Mn基氧化物被证明在电解液中存在催化剂溶解-再沉积的动态平衡过程,使其在全 pH 范围内具有优异的本征活性与稳定性[41]。
HER反应包含两步质子-电子传递,酸性条件下该反应机理主要经历下列三个步骤,如式(6)~式(8)。
其中,Had表示吸附的氢原子;*表示氢吸附的活性位。催化剂的性质决定HER反应经历Volmer-Heyrovsky 过程或者 Volmer-Tafel 过程,结合 Tafel斜率可以判断反应路径及相应决速步骤。铂(Pt)基催化剂由于其近乎零的过电位和在极端pH条件下优异的稳定性,被认为是HER电催化剂的“圣杯”。同样,贵金属材料的高成本和稀缺性阻碍了它们大规模的实际应用[48]。因此为了在性能和成本之间保持更好的平衡,必须在不牺牲活性的情况下降低Pt 的负载量。优化Pt 基催化剂活性中心的常用策略主要包括将 Pt 颗粒尺寸缩小到亚纳米簇甚至单原子级别提高原子利用率[24, 49],与其他金属形成合金调整电子结构[50]以及调控金属-载体的相互作用[51]等。
近年来研究表明,许多低成本的非贵金属基化合物是具有竞争力的HER 催化剂,例如,非贵金属硫化物、碳化物、硒化物、磷化物、氮化物和氧化物[52],其中典型的便是基于 MoSx和 CoPx的 HER电催化剂,具有较高的催化活性[53]。尽管商业化的PEMEL 大多数使用的是铂族催化剂,但非贵金属催化剂廉价的成本以及日益改善的性能展现了其投入商业化、取代贵金属催化剂的广阔前景。
三、 PEMEL制氢的优势
AEL 装置使用 KOH 或 NaOH 水溶液作为电解质,隔膜为石棉,镍材料用作电极。产生的氢气的纯度约为 99%,但必须通过脱附过程去除生成气体中的碱雾,为此通常使用脱附。与 AEL 相比,PEMEL 以质子交换膜替代石棉膜,传导质子并隔绝电极两侧的气体。同时,PEMEL 装置采用零间隙结构有助于其高压操作,电解池体积更为紧凑精简降低了电解池的欧姆电阻,大幅提高了电解池的整体性能。图2显示了三种主要的电解水制氢技术即 AEL、PEMEL 和 SOEL 的电解池性能总览图[19]。
纵轴是不同电流密度下电解池以低热值(LHV)为基础的效率,表示效率越高,操作成本越低。上横轴表示不同电流密度下单位面积的产氢速率;下横轴是电流密度的变化,表示电流密度越大,产氢能力越强,资本成本越低。图2表明PEMEL的运行电流密度通常高于1A/cm,至少是AEL电解池的4倍以上;效率也略高于AEL,单位面积产氢速率也是三者中最具优势的。从制氢效率的角度来看,SOEL 最高,PEMEL 次之,但是 SOEL 由于其操作温度较高,解决材料降解和使用寿命方面具有较大的挑战,因此仍处于开发阶段,远未达到商业化状态。
表1总结了三种电解水技术的主要参数。表1中的参数对比表明,AEL、PEMEL 两项技术均已实现了商业化,具备MW级的制氢能力和较长的使用寿命;同时参数对比突出了PEMEL以下的优点:
①电解池运行电流密度显著高于其他两项技术,降低了电解的总体成本。高的电流密度是由于PEMEL 的质子交换膜比AEL 的电解质更薄,提供了良好的质子传导性(0.1S/cm±0.02S/cm),从而减小了欧姆损失[20]。
②产氢纯度最高,质子交换膜的气体渗透率远低于 AEL 的石棉膜,尽可能避免了气体交叉渗透现象,这有助于 PEM 电解池在生成的气体中没有碱 雾, 因 此 对 环 境 更 加 友 好;同 时 这 也 允 许PEMEL 在宽范围的功率输入下工作。此外,质子交换膜能够实现差压设计,阳极端常压,阴极端压力最高可达350bar (1bar = 105Pa),有利于提高产氢纯度。
③可冷启动,一般5℃以上即可,运行温度可为室温~80℃,启动时间为毫秒级,生产速率可以在整个负载范围内发生变化,维持可再生能源稳定地输入电网,使储能应用更加灵活,而SOEL装置由于组件的热膨胀系数不同,开启和关闭过程时间较长。
长按识别二维码关注公众号,点击下方菜单栏左侧“微信群”,申请加入群聊
我国 PEM 电解水技术正处在从研发向工业化的过渡阶段,国内多家单位开展了PEMEL技术的研究工作。20世纪90年代初期中国航天员中心开展空间站电解制氧关键技术预先研究。2012 年,电解制氧装置随“天宫一号”发射顺利实现在轨稳定运行,地面稳定运行达 23000h[70]。20 世纪 90 年代中国科学院大连化学物理研究所也开始研发PEMEL制氢,2019年与阳光电源签订PEMEL制氢技术战略合作协议,合作开发百千瓦级以上大气量PEMEL制氢装备,助力PEMEL制氢科研成果有效转化。2016年,淳华氢能联合同行企业投资160亿在浙江台州建设国内首个氢能小镇,其中六大产业集群包括了PEMEL制氢产业集群。淳华氢能水电解电堆实现在电解系统轻量化的基础上,提高质子膜水电解池的性能[71],避免了运行过程中SPE膜由于高差压出现剪切或机械损伤的问题[72]。2018年,三峡资本与全球最大的 PEM 制氢设备企业——美国普顿公司合作在国内设立生产工厂,引入先进的PEM 电解水制氢技术,进一步提升国内氢能装备技术水平。
我国2019年1月1日开始实施的《压力型水电解制氢系统安全要求》以及2020年1月1日开始实施的《压力型水电解制氢系统技术条件》进一步规范了我国 PEM 水电解制氢技术行业,更有效地推动国内PEMEL制氢产业化进程。2019年中国氢能联盟发布的《中国氢能源及燃料电池产业白皮书》中提到2030年左右氢能市场发展中期,可再生能源电解水制氢将成为有效供氢主体[73]。国内水电解制氢产品虽然在能耗、产氢纯度及其他指标能够与国外产品比肩甚至更具优势,但在大规模、大功率水电解制氢方面,国内与国外相比还有很大程度的不足。因此国内PEMEL制氢产业迫切需要开发大容量、集成式的电解制氢设备,增加质子交换膜国产化程度并降低整个电解系统成本。
五、 PEMEL制氢的发展瓶颈
PEMEL制氢技术正在从研发走向工业化阶段,商业化程度越来越成熟,在国外甚至已被大规模地应用于钢铁厂等行业进行脱碳[74]。但为了制氢成本、性能及耐用性等各方面能够相较于碱性电解池更具优势,PEMEL 技术必须继续突破目前的发展瓶颈。
1、制氢成本
首先是降低制氢成本,其由运营成本和投资成本组成。运营成本主要是电力成本,依赖于可再生能源电力,由于资源分布(风、光)不均和负荷需求不平衡,输送通道的制约,很大程度上影响可再生能源的消纳和利用率。投资成本包括电堆系统、电力电子设备、气体清洁装置和其他前期成本。电力电子设备成本可以通过更好的电流-电压匹配和工厂规模的平衡来解决,但是电堆系统需要进行技术开发才能达到成本目标。
为了通过创新进一步降低成本,需要将工作重点放在成本最高的组件上。电堆双极板组件过去曾占电堆成本的51%[75],但通过采用冲压工艺并消除了贵金属镀层,成本降低了75%,目前只占电堆成本的11%。现今常使用的商用PEM电解槽中,使用1m2的膜电极组成60kW的装 置 , 在 3A/cm2 的 电 流 下 , 实 际 产 氢 量 可 达12.5m3/h。其中膜电极使用 Nafion 117 商用膜的价格在15000元左右,气体扩散层的价格在10000元左右(共2m3),而催化剂的价格按使用Pt/C和IrO2计算,阴极催化剂原料的价格在 5000元左右,而阳极催化剂原料的价格在25000元左右,加上辅料和加工费用,总体价格会有 50% 以上的浮动。因此降低 MEA 和气体扩散层的成本具有重要意义。
贵金属作为稀缺资源,在很多领域有战略应用,随着贵金属的大规模使用,贵金属资源的大量使用,其价格也会逐渐攀升。因此使用非贵金属替代是势在必行的。如能减少使用一半贵金属催化剂用量,就能降低至少30%的MEA原料成本。开发膜制备技术需要在减小膜厚度的情况下,注重质子传导率、氢氧气体交叉渗透以及高压差下的机械稳定性三者之间的平衡[76],这是目前膜技术开发所面临的瓶颈问题。而气体扩散层的微观结构对装置的整体效率起着重要作用,需要在孔隙率和平均孔径值方面进行优化。
2、电堆性能
其次是提高性能,电堆的性能主要取决于电极材料。目前无论是阳极材料还是阴极材料,性能最佳的仍是贵金属基电催化剂。为了达到既提高性能又降低成本的目标,更多的研究需要关注于降低贵金属的负载以及寻找高性能的贵金属基电催化剂替代品。另一方面,OER 缓慢的动力学和OER 催化剂材料的不稳定性为PEMEL技术的最终商业化制造了技术障碍,利用原位表征技术和理论计算相结合,探索 OER 复杂的反应机理和活性中心的识别及动态演变是未来研究的关键[77]。
3、电堆寿命
最后是增强耐用性,延长电解池的寿命。PEMEL的电能大多由可再生能源多余的发电供给,而这种性质的电源会导致电解池波动性、间歇性地运行, 来应对频繁的启停瞬变。这种情况对PEMEL 会产生何种影响,相关的研究并不多。但可以参考其逆装置PEMFC,PEMFC的启停循环对电解池寿命有很大的负面影响,会引起催化剂材料的降解[78]。因此为了扩大当前的 PEMEL 技术在制氢市场中的份额,研究频繁的启停瞬变对 PEMEL耐用性的影响以及作出针对性地解决策略是必不可少的。通过市场提供的数据样本对电堆各个组件的生命周期以及催化剂材料的降解机理进行研究是一个很好的途径[79]。但由于 PEMEL 技术市场化程度并不算高,能够提供的数据较少,因此如何改善预估组件寿命的方法,以及如何进行加速测试获得更多的数据对电堆使用寿命进行研究以增强其耐用性是目前的一大挑战。
六、PEMEL制氢的应用展望
随着规模从最初的实验室应用扩大到工厂每天数百公斤氢气供给以及电力成本的不断下降,PEMEL 制氢技术在制氢市场将更具竞争力[80]。同时,由于PEM电解池的发展驱动因素与PEMFC不同,目前开始将燃料电池中许多材料和制造技术应用于电解池,为大幅度降低资本和运营成本提供了机会[81]。而且由于 PEMEL 技术应用条件灵活,采用该技术制氢的微型加氢站体积小,可以设计成可移动的集装箱式,装运方便,适合应用在土地有限的大城市、临时场所、独立的产业园区。
针对和下游产业的联合应用,PEMEL 制氢技术能够生成纯度在 99.9% 以上的氢气,可以在比AEL 电解装置 (约 30bar) 更高的压力 (约 50bar)下生产氢气,更好地适应下游高压需求的应用。
-
第一条途径可以作为化工原料和来自工业废气或空气中捕集的CO2合成甲烷、甲醇以及费托合成产品。 -
第二条途径可以和来自空分的N2进行Haber-Bosch 合成氨[87]。 -
第三条途径为直接作为能源应用,PEMEL 技术可以作为加氢站的制氢方法,为燃料电池汽车提供动能,减轻交通运输行业造成的尾气污染[88]。除运输外,家庭供暖和工业高品质热源也是可能出于脱碳目的而提高低碳氢需求的行业。将氢气混合到现有的天然气网络中几乎 不 需 要 对 基 础 设 施 或 终 端 用 户 设 备 进 行 调整[89-90]。 - 此外,超纯氢气作为还原气体和保护气体,是电子器件和芯片加工行业的关键原料,主要应用于半导体器件、集成电路芯片以及液晶平板显示器生产等领域,随着我国集成电路产业和软件产业的升级转型,超纯氢气将拥有更大的用武之地。
原文始发于微信公众号(艾邦氢科技网):质子交换膜电解水制氢技术的发展现状及展望
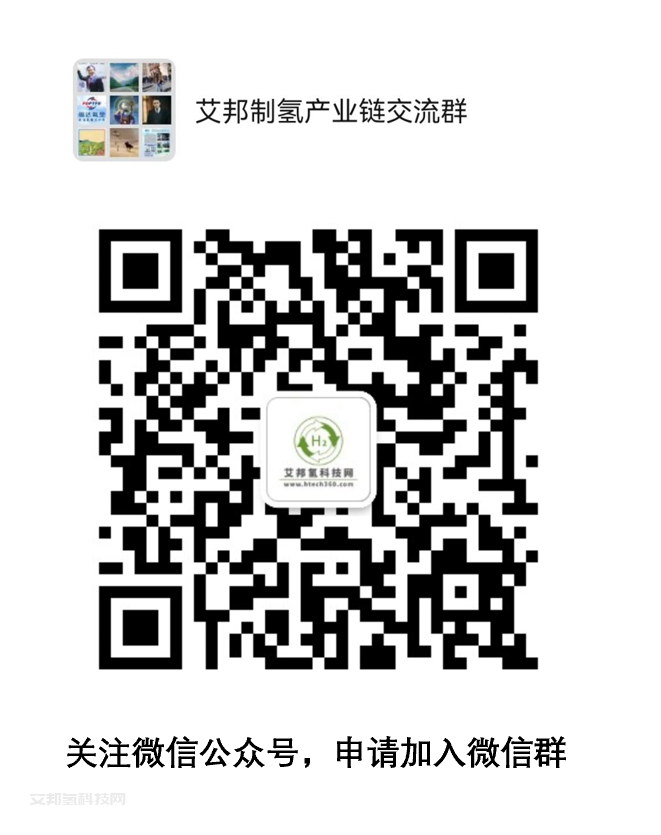