氢眼所见寻找有缘的氢能人,有缘之人可添加微信“zen13480834343”
好吧,太久没太关注燃料电池了,也好久没有再阅读相关资料和文献了,想当初我还是是个做燃料电池的,这个公号最早更多的内容也是在讨论燃料电池,燃料电池也算是我进入氢能行业的引路人,今天就当怀旧插播一篇和燃料电池控制相关的内容吧!
说明:本文来自于:
Proceedings of the 14th International Symposium on Process Systems Engineering – PSE 2021+
June 19-23, 2022, Kyoto, Japan © 2022 Elsevier B.V. All rights reserved.
燃料电池(FC)系统控制器用于电堆、空气、H2和热管理系统,并与系统硬件模型集成。这些控制器允许在闭环模拟下灵活地改变系统硬件规格和操作条件。该文章对虚拟FC系统的硬件和控制器设计及系统性能评估进行了论证和验证,为实际的产品系统开发过程提供了有益的参考。
一、介绍
FC-系统控制器的作用是在考虑硬件限制的情况下,通过操纵系统组件来确保FC堆栈中的最优条件,以实现系统效率和加速响应等最大的系统性能。在许多FC系统制造商中,只有在系统试验台的原型制造出来之后才能进行控制器的设计工作。由于系统试验台的准备周期长,费用大,因此对用于虚拟控制器开发和评估的系统集成模拟器的需求很大。尽管对控制系统的研究非常重要,但对燃料电池本身的研究更为深入,而对FC电堆、包括空气、H2和冷却系统等系统组件的FC系统以及FC系统控制器的研究则少得多。利用FC堆叠的物理模型和空气、H2和冷却系统的系统组件开发了集成FC系统模拟器。该模拟器可以以可接受的精度和允许的计算时间估计第二代MIRAI(图1所示的最新商用燃料电池电动汽车(FCEV))的整个燃料电池系统的动态行为。该模型可用于乘用车、公共汽车和轨道的商用车、铁路、船舶、航空和固定式发电机等广泛的应用系统开发,尽管它只包括FC堆栈的硬件模型,不包括FC系统组件和控制器。
在本研究中,开发了具有流线型配置的整个FC系统控制器,其中FC系统净功率的设定值、FC系统堆栈状态变量和FC系统组件的驱动值可以独立确定,并且非常容易修改、替换、添加和删除控制器规格。将这些控制器与上述FC系统硬件模型进行集成,得到闭环FC系统模拟器。该模拟器缩短了整个FC系统和控制器开发的开发周期,减少了不同应用系统原型的开发费用。利用所研制的闭环模拟器,研究了冷却剂散热器尺寸对FC系统性能、FC系统净功率动态设定点跟踪性能和FC系统净效率的影响。
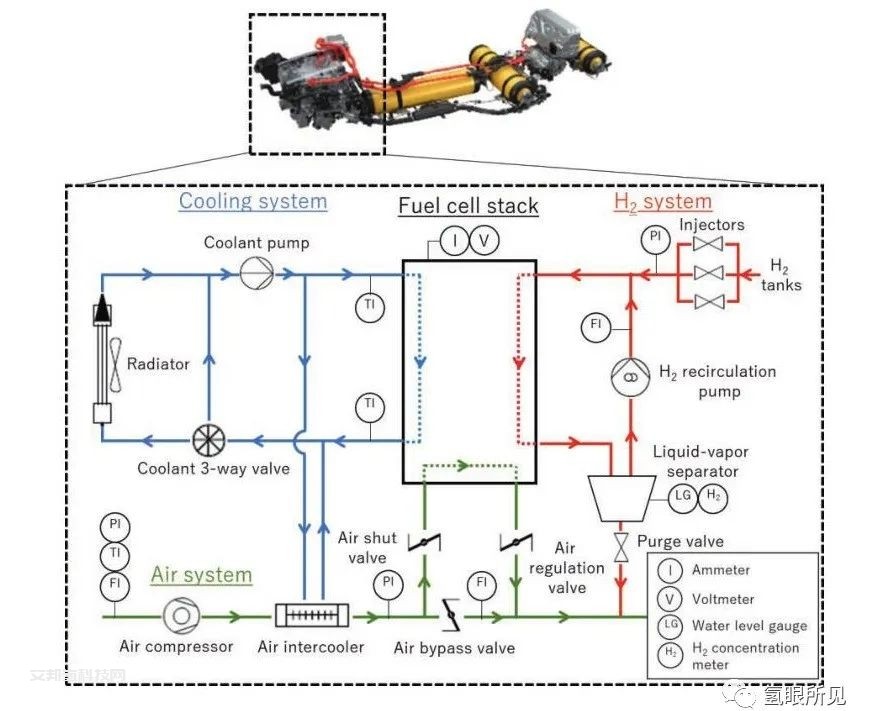
图1:第二代MIRAI中FC系统实现流程图
1.FC系统净功率由式(1)定义:

式中:
:FC系统的净功率,单位是[W]

Pothers:其他系统组件(如DC-DC转换器)所消耗的功率,单位为[W]
2.FC系统净效率定义为式(2)如下:
式中:
:FC系统净效率
:电堆的产热率,单位为[W]
:由下面式(3)和式(4)计算得出:
式中:


:电堆的开路电压,单位为(V)
由本研究开发的FC系统控制器和FC系统硬件模型组成的闭环FC系统模拟器的组态如图2所示。在该模拟器中,FC系统净功率的设定值、环境温度和大气压力是电力控制器的输入。计算出的FC系统净功率以及FC系统中的其他计算值、FC堆叠极化状态(如电流、电压和电阻)、状态变量在整个系统中的分布(如压力、流量、温度和气体组成)以及FC系统组件的执行值(如泵速和阀门开度)。
图2:整个FC系统闭环仿真流程图
图2中的控制器包括电力控制器、FC堆栈控制器和用于空气、H2和冷却系统中的系统组件的执行器控制器。电力控制器确定FC电流的设定值,以减小设定值与系统净功率计算值之间的误差。FC堆叠控制器由空气、H2和冷却状态控制器组成。每个状态控制器根据图1中I和TI所示的传感器测量的FC-堆栈电流和冷却剂出口温度以及预先校准的函数,确定状态变量的设定点,如压力、流量、温度和FC堆栈进出口的气体组成。空气、H2和冷却剂的执行器控制器确定执行器值的设定值,如泵转速和阀门开度,以最小化fc堆栈控制器的状态变量设定值与传感器测量的状态变量的实际值之间的误差,如图1所示。这样一个简单和流线型的控制器配置,使独立调查的最佳堆栈操作条件和硬件规格。
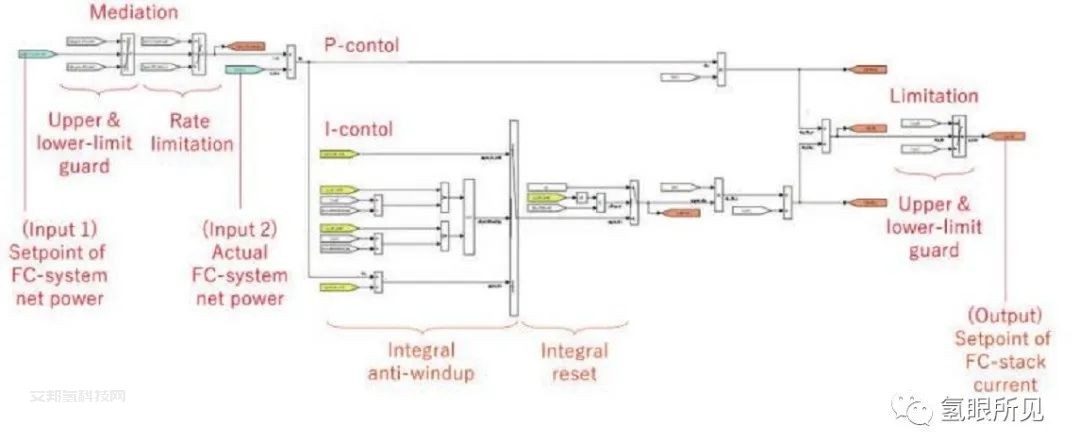
图4是Simulink流程图中包含的气压确定算法。将FC堆栈电流和温度的设定值指定给预先确定的函数,这些函数是基于实验数据建立的,以在考虑电力消耗和空气压缩机损耗的情况下实现最大的FC系统净效率。然后,计算空气压力设定点。预定函数也用于确定其他状态变量的设定点。空气中H2,和冷却系统控制器,通过图3所示电力系统控制器中基于PI控制的相同算法,将FC堆栈控制器输出的状态变量的设定点转换为驱动值,例如泵速和阀门开度。借助图2所示的闭环模拟器,在不制造集成FC系统硬件的情况下,可以优化和确定预定功能和PI控制器参数。这减少了硬件准备的大量工作和费用。
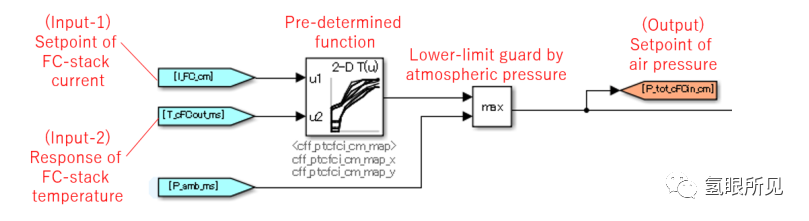
图5为如图2所示的闭环仿真结果,确认了当车速保持在160 km/h不变、冷却剂散热器尺寸变化时FC -系统净功率的设定点跟踪性能。如图5 (a)所示,在基本尺寸散热器的情况下,FC系统净功率可以在小于1%的可接受偏差范围内跟踪设定值。图5 (b)显示,当冷却剂散热器尺寸为基本尺寸的70%时,FC系统净功率在660 - 670秒内偏离设定值3%。在此期间,冷却剂的平均温度上升到105℃,如图5 (c)所示,其中FC堆叠的IV性能由于图5 (d)所示的严重干燥条件而恶化。从这些结果表明,在给定的操作条件下,散热器尺寸减小的限制在85%左右。
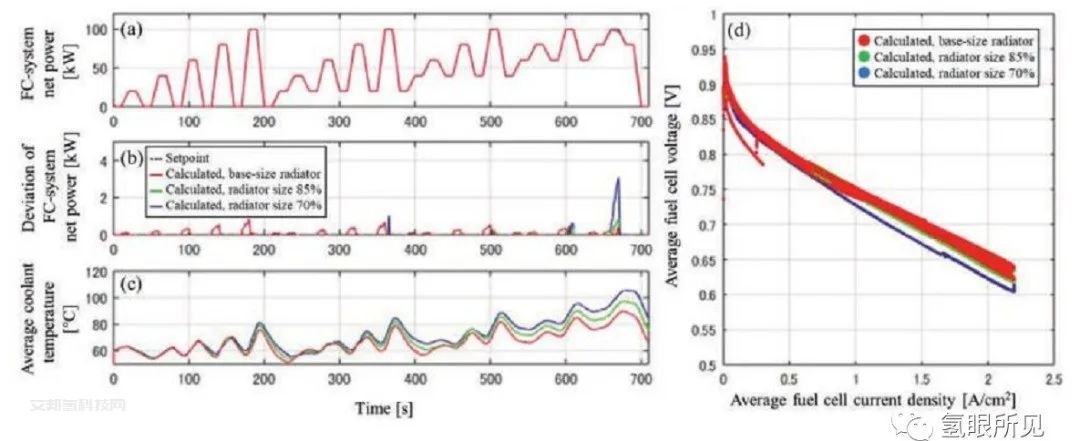
图5:冷却剂散热器尺寸和以下相关设计
(a) fc系统净功率设定点和计算值,
(b) fc系统净功率设定点和计算值之间的偏差,
(c)平均冷却剂温度,

图6:闭环仿真输出fc系统净效率
图5和图6中的例子表明,在本研究中对整个FC系统进行闭环仿真,可以在制造昂贵的FC系统试验台和测试车之前进行详细的系统硬件和控制研究。另一方面,图3中PI -控制的增益和图4中目标状态变量的预定函数等控制参数是通过耗时的试错校准的,理论上无法保证FC系统净效率的最大值。引入模型预测控制(MPC)等最先进的优化技术,实现更高效、更复杂的控制器参数确定过程。
结论:
原文始发于微信公众号(氢眼所见):基于模型的燃料电池堆和系统控制器的开发
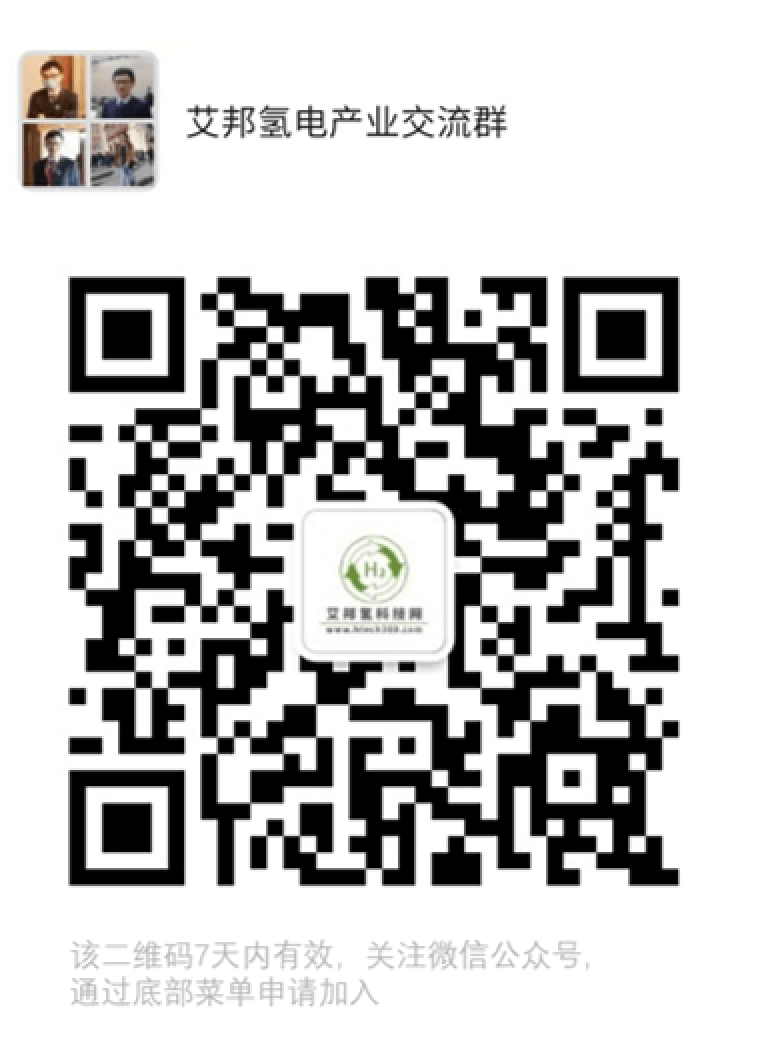