1.背景意义及解决的关键问题
全球新能源汽车正进入转型升级的关键时期,汽车的生态环境正持续改善。其中,发展氢能燃料电池汽车成为全球共识。我国已将氢能燃料电池汽车列入国家发展战略,预计2030年年产量将达到百万辆。
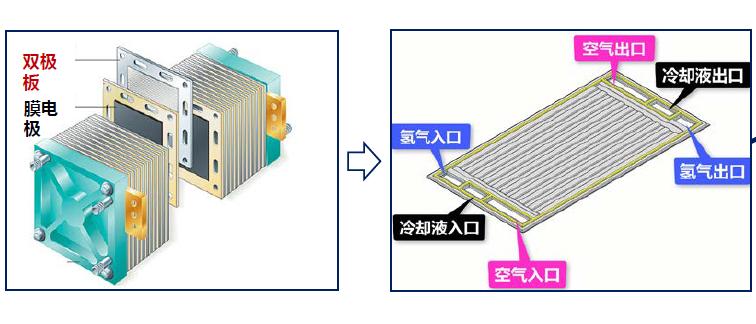
双极板作为燃料电池堆的核心部件之一,约占电堆体积的70-80%、重量的60%和成本的30%,其决定了电堆的体积和质量功率密度。金属双极板导电率高、热传导率高、机械性能好以及阻气性高,适合应用于要求高功率密度电堆的领域(如乘用车)。通过对氢燃料电池用金属双极板部件关键技术调研分析,提供金属双极板部件技术研发最新进展,促进金属双极板及燃料电池的国产化元件,降低氢燃料电池及金属双极板成品部件的技术门槛,构建氢能及氢燃料电池应用服务生态。
在金属双极板领域,日本丰田与本田、瑞典Cellimpact、德国Grabener与Borit、美国Dana与treadstone占据全球90%的市场份额。典型代表产品是丰田纺织生产的用于丰田Miari 2的钛基材金属双极板。通过预先在轧制钛卷材上进行碳纳米复合涂层表面处理,无需在冲压成形后进行再处理。单片厚度0.8 mm(厚度可达到0.05-0.3 mm)、腐蚀电流密度低于0.8 μA/cm2,对应电堆的体积功率密度为5.4 kW/L,运行寿命超过5000 h。
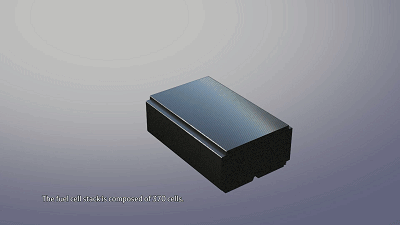
国内目前金属双极板还处于研发及试用阶段,未实现大规模的商业化应用,尤其缺乏长时间燃料电池整车运行工况下的测试验证工作。典型代表产品是新源动力股份有限公司的金属双极板,其采用不锈钢材料冲压制造工艺而成,单片厚度1.07 mm、腐蚀电流密度小于1.0 μA/cm2、市场占有率60%,对应电堆的体积功率密度3.3 kW/L,电堆运行寿命超过5000 h。
2. 技术先进性及国际对标
2.1 该领域技术国内外发展现状、最优水平及趋势
金属双极板弯曲强度高、厚度小、导热能力强,适合大批量、低成本生产,所组装的燃料电池体积小、重量轻、功率密度高、低温启动性能好,是乘用车用双极板的主流技术路线。在金属双极板领域,日本丰田与本田、瑞典Cellimpact、德国Grabener与Borit、美国Dana与treadstone占据了全球绝大部分市场份额。金属材料固有的密度高和不耐腐蚀性,难以满足乘用车在重量方面和长期使用方面的要求,因此发展高耐腐蚀、高导电性、低成本的涂层材料成为发展方向。以日本神户制钢为代表的碳纳米复合涂层技术实现了预先在钛卷材上进行表面处理后冲压一步成形制造,无需后续表面处理,极大提高了生产效率和降低制造成本,该产品已成功应用于丰田Mirai 2。另外,国外产品的技术优势主要体现在金属双极板表面涂层耐腐蚀处理的同时,保证接触电阻小,形成了金属基底材料表面的高导电性与高耐腐蚀性的有机统一。
目前国内金属双极板普遍存在寿命短、表面涂层腐蚀电流大、制造成形一致性差的缺点,尚不能完全满足乘用车要求5000 h的技术指标。金属基材、防腐蚀、焊接技术是制约金属双极板发展的关键。国内外在技术储备上的差距主要在原材料,材料配方,构型设计、精密成形、高效连接和涂层等方面。
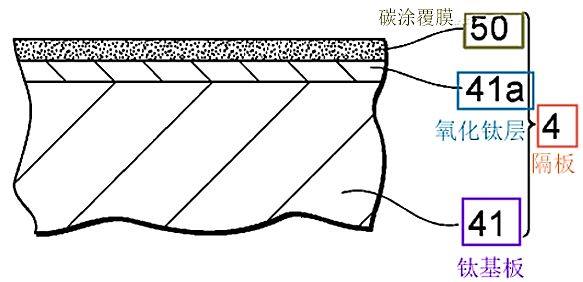
在金属双极板领域,国外典型代表产品是丰田纺织/神户制钢生产的用于丰田Miari 2的钛基材金属双极板。通过预先在轧制钛卷材上进行碳纳米复合涂层表面处理,无需在冲压成形后进行防腐涂层表面处理。单片厚度0.8 mm(厚度可达到0.05-0.3 mm)、腐蚀电流密度低于0.8 μA/cm2,对应电堆的体积功率密度为5.4 kW/L,运行寿命超过5000 h。
目前国内金属双极板还处于研发及中试阶段,并未实现大规模的商业化。以上海治臻为代表的金属双极板产品采用连续冲压技术,双极板厚度为0.1 mm,流道深度0.3-0.5 mm,宽度为0.8-1 mm,其对应电堆的体积功率密度达到3.3 kW/L,金属极板厚度要比业界最薄的石墨板降低52%,比石墨极板电堆功率密度提升2.4倍(注:数据公开报道)。
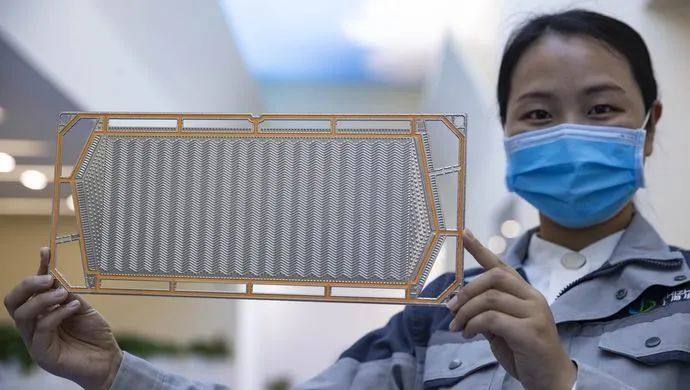
上海治臻、大连新源动力、华中科技大学、上海交通大学、同济大学、上海捷氢科技有限公司、武汉理工大学。珠海格力电器股份有限公司、佛山市清极能源科技有限公司、华南理工大学、南科燃料电池有限公司、深圳市雄韬电源科技股份有限公司、爱德曼氢能源。
觉得有用的点再看哦!
原文始发于微信公众号(氢能人):金属双极板关键部件开发进展分析
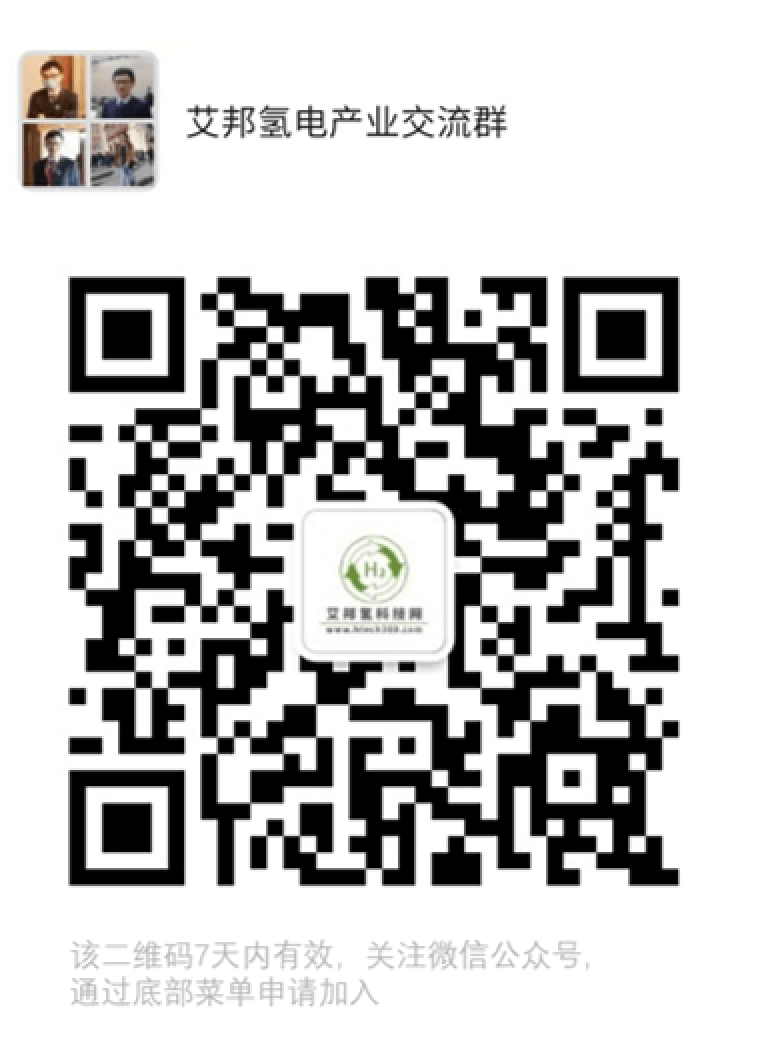