燃料电池主要由质子交换膜、催化剂层、空气扩散层和双极板组成。双极板作为燃料电池的核心部件,在燃料电池中,起到了膜电极结构支撑、分隔氢气和氧气、收集电子、传导热量、提供氢气和氧气通道、排出反应生成的水、提供冷却液流道等诸多重要作用,其性能很大程度取决于流场结构。
在金属双极板成形过程中,密切相关的因素有材料(抗拉强度、屈服强度、延伸率、n值等)、成形机(压力稳定性、行程精度等)、模具结构和精度(结构强度、加工精度、流道表面粗糙度、模具调整方法等)以及流场的结构设计。
随着新天宇公司从事燃料电池金属双极板模具设计开发的种类和数量增多,工程技术人员在成形分析、模具设计与模具调试过程中,总结相关经验数据,探讨了流场参数对流场成形效果(流场起皱、开裂、流程深度差、翘曲等)的影响,通过本文,以供金属双极板流场设计者参考。
一、流场参数
目前流场形状有直通道、蛇形、螺旋形、交指型和网格形等,同时相关研究人员也在不断开发新型流场,如仿生流场、3D流场,而实际应用中、以氧极板采用直通流道、阴极板采用S形流道居多。
流场参数主要有流道拔模斜度、开口内圆角、根部圆角、流道宽度、流道深度,流道间距、S形流道波长和波高等。
二、流场参数与成形结果的关系
1.拔模斜度的影响
通过对拔模斜度的计算和有限元分析,可得到拔模斜度和延伸率成负相关关系。
在一次成型的情况下,18°以下拔模角,拉延时实际延伸率通常超过50%,极容易出现流场开裂的情况,特别是S形流场的转角处,建议一次拉延最小拔模角≥20度。
2.圆角的影响
通过计算和分析,圆角半径和实际延伸率成负相关关系。当使用不锈钢SUS316L,材料厚度0.1mm,一次成型的情况下,建议最小圆角半径≥0.1mm。
3.成型次数的影响
通过分析和试验,建议的成形次数和成型角与圆角的关系:
4.材料、成型角和流道之间步距的关系
通过试作不同材料,不同流道间距和流道高度,试验得到如下结论:
1) 使用SUS316L材料,当流场高度0.5时,最小流道间距可达到1.1,平面宽度0.2;
2) 使用TA1材料,当流场高度0.5时,最小流道间距可达到1.4,平面宽度0.4;
以上数据仅做参考,不作为金属双极板流场设计的依据。欢迎同行和金属板设计者进群批评指正。
来源:NEWSKY新天宇
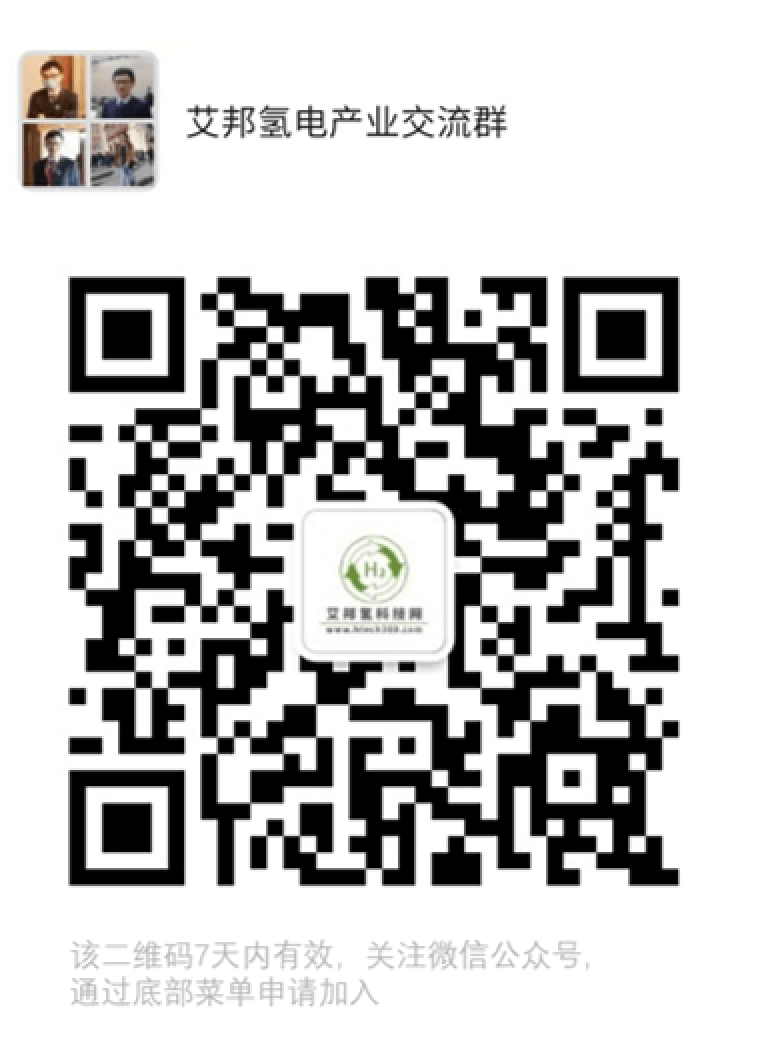