提高燃料电池汽车从油箱到车轮的效率和使用寿命可靠性的材料解决方案
8月 21, 2021
– 1 –
文凭。英格。于斌,全球系统专家电动汽车,帝斯曼工程材料
Tamim P. Sidiki 博士,DSM Engineering Materials 全球移动营销总监 Robert R. Janssen 博士,DSM Engineering Materials 首席科学家
提高燃料电池汽车从油箱到车轮的效率和使用寿命可靠性的材料解决方案
提高油箱到车轮效率的材料解决方案和
燃料电池的寿命可靠性
请保持页脚不受自己的文字影响!
抽象的
提高燃料电池汽车从油箱到车轮的效率和使用寿命可靠性的材料解决方案
燃料电池技术是交通零排放的重要贡献者。燃料电池堆作为燃料电池发动机的心脏,是一种电化学装置。由于其工作机制和工作条件,从燃料电池中使用的材料中浸出的离子会导致灾难性后果,例如催化剂中毒、膜堵塞和系统绝缘水平降低。这种离子还可以加速金属双极板的腐蚀。此外,塑料部件的水解降解会导致机械劣化和尺寸蠕变,从而使系统的稳健性和介质密封性能面临风险。在本次演讲中,我们将展示有关此类离子浸出的影响的最新结果,以及专用材料的开发如何不仅可以实现最低的离子浸出,而且还可以在所有工程材料中实现高机械保持力和熔接线强度。因此,燃料电池运行的具有挑战性的可靠性和效率要求也可以实现超过 20,000 小时的使用寿命。
简洁版本
提高油箱到车轮效率的材料解决方案和
燃料电池的寿命可靠性
燃料电池技术为交通零排放做出了重要贡献。作为燃料电池发动机的心脏,燃料电池堆是一个电化学部件。由于工作机制及其工作条件,从燃料电池中使用的材料中浸出的离子可能会产生灾难性后果,例如:B. 催化剂"中毒"、膜堵塞和催化剂减少
系统内的绝缘性能。这种离子还可以加速金属双极板的腐蚀。此外,塑料部件因水解而变质会导致机械降解和尺寸变化,从而危及系统的坚固性和密封性能。本演讲将展示有关这种离子浸出效果的最新结果,以及特殊材料的开发如何不仅可以实现世界上最低的离子浸出率之一,而且还可以在所有工程材料中实现非常高的机械保留和焊接强度。
抽象的
化石能源促成了工业革命,但它也是局部空气污染最负面的来源,也是 CO 2和其他温室气体的排放源。根据世界卫生组织 (WHO) 的数据,地球上十分之九的人呼吸着被污染的空气,每年造成 700 万人死亡。世界卫生组织的结论是,大约四分之一的心脏病、中风和肺癌死亡可归因于空气污染。全球平均气温上升归因于温室气体排放量的增加,这就是为什么全球正在努力从化石能源转向更可持续的能源——最终目标是可再生能源。
在温室气体的不同来源中,交通部门、化学工业和钢铁工业的排放是气候变化的主要贡献者——例如,大约 4% 的年总排放量和大约 24% 的二氧化碳排放量来自燃烧化石燃料运输部门。然而,交通运输中的化石替代品——电子燃料、纯电池和燃料电池——都存在一些局限性,这对更广泛的市场接受度来说是一个挑战。
在本文中,我们将主要关注氢燃料电池技术,并展示使用过的工程材料在离子浸出和耐水解性方面的重大改进,这将直接影响燃料电池堆在运行中的罐到轮效率和使用寿命可靠性。解决燃料电池技术目前的缺陷将是提高市场接受度和市场渗透率的重要贡献。
氢是替代化石燃料的候选者之一
CO2 浓度超过 400 ppm,是 80 万年来大气中的最高浓度(见图 1)。几乎所有这些都可以归因于人类排放。根据国际能源署 (IEA) 的数据,主要涉及公路、铁路、航空和海运的交通排放量占全球二氧化碳排放量的四分之一。仅货运一项就消耗了运输部门所用能源的约 40%。
大气二氧化碳浓度
全球平均长期大气中二氧化碳 (CO 2 ) 浓度,以百万分之几 (ppm) 为单位。可以使用来自冰芯的保存空气样本以高分辨率测量CO 2浓度的长期趋势。
100 ppm 50 ppm
0 ppm
803719 BCE 600,000 BCE 400,000 BCE 200,000 BCE 2018
资料来源:EPICA Dome C CO 2记录 (2015) 和 NOAA (2018) OurWorldInData.org/co2-and-other-greenhouse-gas-emissions • CC BY
图 1:历史大气中的 CO2 浓度,来源:Our WorldinData.org ( https://ourworldindata.org/grapher/co2-concentration-long-term )
为了将温度上升保持在避免最严重气候影响的范围内,IEA 建议交通排放需要在 2020 年左右达到峰值,然后迅速下降。
交通部门的脱碳将为每个人创造一个更清洁、更健康和更负担得起的未来,并且可以在不损害现代性所期望的移动便利性的情况下做到这一点。此外,立法以及公共和私营公司越来越多的努力加快了电气化的步伐。
燃料电池避免了化石燃料燃烧过程中产生的空气污染和全球变暖。氢基燃料电池仅在使用点是水时才会产生水作为副产品。此外,燃料电池的效率优于任何柴油或燃气发动机。
虽然移动行业通过各种高性能塑料和复合结构替代金属,不断提高传统内燃机的效率并减轻车辆重量,但动力总成的电气化是解决交通运输行业排放量增长挑战的重要组成部分,因为它消除尾气排放。为了进一步加强 CO 2减排,燃料电池还可以减少空气污染,并且可以进一步帮助减少声音污染,因为与内燃机 (ICE) 相比,燃料电池的运行安静。
相对于纯电动汽车,燃料电池电动汽车有很多优势,见图2
− 与内燃机汽车相当的快速加油时间
− 续驶里程可与标准 ICE 车相媲美
− 船上没有沉重的电池
− 燃料电池与锂电池 (LiBs) 性能对天气的依赖性有限
作为移动领域电气化的支柱之一,燃料电池技术,尤其是质子交换膜燃料电池汽车 (PEMFC) 越来越受到关注,它确实在效率和排放之间取得了有益的平衡。由于重量和续航里程增加的相关性更高,几乎所有主要 OEM 都已经在或计划投资于燃料电池汽车的商业化,首先针对卡车和公共汽车。
在各种燃料电池技术中,特别是 PEMFC 是首选,因为它的工作温度足够低(80°C 到 110°C),启动时间短,能够以纯氢气和环境空气作为氧化剂运行,并且具有可比性- 为 ICE 加油的时间。
图2:不同传动系的续航里程比较
除了 PEMFC 的所有优点外,它还是一种精密的设备,需要从材料选择、设计、制造和质量控制方面进行谨慎考虑。燃料电池结构的材料选择不当可能导致灾难性故障。杂质,例如从材料中浸出的离子会逐渐堵塞膜并导致使用寿命缩短。燃料电池系统中的组件暴露在高湿度和温度下会发生材料水解,从而导致变形和降解。这种物质影响将显着降低燃料电池系统的性能并危及其效率和寿命。
质子交换膜燃料电池车
作为电动动力系统的一种选择,燃料电池改变了获取和发电为车辆提供动力的方式。与部分或完全依赖锂离子电池动力的插电式混合动力汽车 (PHEV) 或全电池驱动电动汽车 (BEV) 不同,燃料电池汽车 (FCEV) 搭载电化学发电系统,可将氢气转化为和氧气转化为电能。热量和水是此过程中产生的唯一副产品。
高效可靠的燃料电池系统可以在商用车辆中运行超过 15,000 小时,需要强大的电化学转换过程。进气和过滤、氢气供应和再循环、燃料电池堆、热管理和相关控制系统等组件需要在早期设计阶段进行无缝和可靠运行。完整的系统布局见图 3。
图 3:燃料电池系统的防喷器
作为车辆核心的实际燃料电池堆由数百个单独的电池和由塑料或金属制成的各种部件组成。每个单独的电池由双极板和膜电极组件 (MEA) 的夹层结构制成,膜电极组件 (MEA) 具有两个气体消散层 (GDL) 和 Pt 催化剂涂层膜。
GDL 通常由基材(例如复写纸)和微孔层组成。涂有催化剂的膜由覆盖有两个催化剂层的质子传导膜组成——该膜通常由全氟化磺酸 (PFSA) 制成(见图 4)。
图4:单个细胞的示意图
催化剂氧化氢分子并分离电子和质子。然后质子可以选择性地通过质子交换膜 (PEM) 从阳极移动到阴极,而电子不能通过膜,将被迫通过外部电路,从而产生电流。在此过程中会产生H 2 O 和热量作为副产品(见图 5)。
图 5:MEA 示意图(来源:Kitiya Hongsirikarn 博士对杂质对质子交换膜燃料电池组件性能的影响)
塑料选择不当可能导致失败
各种材料,例如金属、橡胶和热塑性塑料,都被用于构建燃料电池系统。工程塑料因其易于加工、重量较轻和固有的电绝缘性而被选中。可以使用的工程塑料种类繁多。
然而,要构建具有长期可靠性的燃料电池系统,选择正确的材料对于确保最佳效率和使用寿命性能至关重要。图 6 总结了工程材料选择不当可能导致的潜在故障。
图 6:潜在的故障模式
纯度很重要
鉴于燃料电池是一种电化学装置,可能无意中参与主反应过程的元素会降低燃料电池的性能。杂质,例如离子和有毒气体,可能来自气体(H2 和空气)供应回路和热管理回路,以及用于构建系统组件的材料。因此,了解材料的优点和局限性对于燃料电池系统的成功至关重要。
潜在的杂质通常是有毒气体,例如 H 2 S、CO 和 NH 3,它们被认为是对燃料电池污染最严重的气体,以及来自外部污染或材料腐蚀的离子污染。气体中的杂质会导致严重的 Pt 基催化剂中毒,从而导致质子产量减少(见图 7)。
Na +、Ca 2+、Fe 2+、Ma 2+、Al 3+、Si 4+等材料的离子污染会导致严重的膜堵塞。结果是质子传输能力和膜电导率显着下降。此外,冷却回路中过多的离子浸出会降低车辆的绝缘水平,也会加速金属双极板的腐蚀。虽然制造商通常会采取积极措施来减少供应气体的离子污染,但作为工程材料供应商的帝斯曼还有助于减少系统中使用的塑料材料的离子浸出。
图 7:外部气体污染导致的催化剂中毒(来源:能源科学与工程,第 7 卷,第 6 期,页数:2519-2539,首次出版:2019 年 9 月 4 日,DOI 10.1002/ese3.441)
质子通过膜的传输机制
典型的 PFSA 离聚物基膜的分子结构如图 8所示。它由两个区域组成,PTFE 主链提供化学/机械/热稳定性,亲水性全氟醚侧带有参与质子传输过程的 磺酸 (-SO 3 H) 基团。
图 8:PFSA 离聚物
质子通过膜的传输主要涉及两种机制,即 Grötthuss 机制和载体或扩散机制(见图 9)。一般来说,车辆机制比 Grötthuss 慢,并且取决于扩散速率。在 Grötthuss 机制中,H + 3 O 形式的质子通过 -SO 3 H 基团跳跃到 H 2 O。
图 9 Grötthuss 跳跃机制(来源:R. Thakkar、H. Patel、U. Chudasama,"质子传输的比较研究:磷酸锆及其金属交换相的性质",Bull. Mater. Sci. 30 (2007) 205 -209)
如上一节所述,阳离子(Na +、Ca 2+、Fe 2+、Mg 2+、Al 3+、Si 4+ ...)都具有更高的化合价或更高的分子量。这些阳离子与质子竞争主反应,形成阳离子-水簇,如Na + (H 2 O) 6、Ca 2+ (H 2 O) 6、Fe 2+ (H 2 O) 8 …这些簇具有更高的分子量,并且由于更高的化合价与 -SO 3的亲和力H比质子强。由于这种效应,它显着降低了膜的电导率。因此,质子传输率显着降低。
在最坏的情况下,过度的离子浸出会导致膜上形成针孔,造成永久性损坏。这些类型的问题可能会显着降低燃料电池的使用寿命和效率。图10显示了不同阳离子污染对膜电导率的影响。
图10 阳离子(Na+,Ca2+,Fe3+)对Nafion膜电导率的影响, 195, (2010),7213-7220
耐水解性很重要
由于一个完整的燃料电池系统由三个主要子系统组成——进气系统、氢气供应系统和热管理系统——所有三个系统中的组件都必须在接口处牢固连接和密封,以避免介质泄漏(见图 3 )。
燃料电池系统主要在 70 至 90°C 的温度范围内工作,几乎 100% 的湿度和温和的酸性条件。虽然这些条件乍一看可能看起来很温和,但实际上它们严重到足以严重降低材料性能——尤其是对于长期机械性能,例如抗蠕变性。使用抗水解性较差的材料制造的组件在这种情况下会受到影响,导致翘曲、变形并最终导致密封界面处的介质泄漏。
为了使制造商获得最佳的组件性能,帝斯曼不仅开发了用于燃料电池的优质工程材料,还提供了详细的计算工具来预测在如此恶劣条件下的长期水解性能。
Xytron ™ PPS 燃料电池平台的最低离子浸出
基于对工程材料导致的潜在燃料电池失效模式的深刻理解,并旨在为燃料电池汽车的长期可靠性提供稳健的材料解决方案,帝斯曼创建了基于 Xytron™ PPS 的技术平台,具有业界最低的离子浸出和最高的耐水解性。
DSM 进行了实验和研究,以比较不同聚合物选项之间的离子浸出性能(见图 11 和 12)。
图 11:不同高分子化合物在 100 ℃热水中的吸水率达到平衡
图 12:1,000 小时后的溶液电导率。去离子水浸泡——离子浸出的指示
通过比较图 11 和图 12 所示的数据,似乎聚合物化合物的离子浸出量与其吸湿性呈反比关系。众所周知,由于其分子结构,聚酰胺会吸收水分。吸湿程度显着取决于分子中酰胺基团的密度及其结晶度。
通常,短链脂肪族聚酰胺比长链聚酰胺或芳香族聚酰胺 (PPA) 吸收更多水分。然而,图 12 显示 PA6 和具有 30% 玻璃纤维的 PA66 化合物吸收的水分较少,但离子浸出率较高。根据 DSM 研究,这与玻璃纤维腐蚀和玻璃纤维与聚合物之间界面的降解有关。
由于所有的聚酰胺都吸收了一定量的水分,它为水分( H 2 O )创造了更多的"反应点"来腐蚀玻璃纤维并降解界面化学,从而在这些界面发生额外的离子浸出。此外,吸湿性会降低
第 42届
11
聚酰胺的玻璃化转变温度Tg,导致聚合物的"软化"效应,导致尺寸不稳定和高温抗蠕变性下降。相比之下,聚苯硫醚 (PPS) 几乎不吸水,其非极性分子结构的半结晶材料具有出色的耐化学性和低离子浸出性,以及出色的尺寸稳定性。
尽管玻璃纤维增强 PPS 化合物在离子浸出方面的性能比聚酰胺好得多,但 DSM 通过优化玻璃纤维和 PPS 聚合物之间的界面化学,实现了进一步的显着改进。通过加强界面的结合,DSM 能够将离子浸出降至远低于替代 PPS 化合物的程度。
图 13:90 ℃ DI 水孵育后绝对离子(所有离子的总和)浸出比较
图 14 90 ℃ DI 水孵育后的溶液电导率
图 13 和 14 显示了完全暴露于 90°C 去离子水后的离子浸出和溶液电导率结果。Xytron™ G4080HR 是 Xytron™ PPS 燃料电池平台的牌号之一。Xytron™ G4020DW-FC 是标准 Xytron™ PPS 等级,竞争等级是交联 PPS 化合物。这三个等级都是 40% 玻璃纤维增强 PPS 化合物。
为了在实验中模拟真实的燃料电池系统运行,样品孵育期间的去离子水在每个数据点都被完全刷新,以避免局部离子浓度平衡,因为在实际应用中水不会静止。除测试外,还进行了长达六周的连续孵化,以供参考。这显示了相同的趋势——采用专用接口技术的 Xytron™ G4080HR 显示出最低的离子浸出和溶液电导率。没有这种接口技术的其他标准等级显示出类似的更高量的离子浸出和溶液电导率。
Xytron TM PPS 燃料电池平台提供最高的耐水性
工程材料的高耐水解性对于确保燃料电池组件在环境影响下的良好机械性能至关重要。图 15 和 16 比较了不同聚合物的耐机械水解性。
图15:高分子化合物95 ℃热水老化对比-模量
图16:高分子化合物95 ℃热水老化对比-强度
第 42届
13
一般来说,与 PA 相比,PPS 显示出更好的长期机械保持力。然而,在 PPS 组中可以看到明显的差异,尤其是在拉伸强度方面。特别改进的 Xytron™ G4080HR 材料可实现最高的机械保持力。PA 较高的吸湿性会使 Tg 降低,从而导致材料软化(见图 17)。长期接触热水后,H 2 O 会分解酰胺基团并水解塑料材料,导致其分子量严重降低。
图 17:高 Tg PPA 和 PPS 在不同状态下的 DMTA-储能模量(E '模量)比较(成型时干燥,吸湿至饱和后和水解老化后)
聚酰胺,即使是具有高玻璃化转变温度 (Tg) 的聚酰胺,也会受到这种软化行为的影响。含有 40%GF 的 Xytron™ G4080HR 是一种极其稳定的材料,即使在 135°C 下老化 3000 小时,也不会导致 Tg 偏移。含 35%GF 的高 Tg PPA 化合物在 90°C 热水中浸泡不到 250 小时,直至达到水分含量约为 3.8% 的吸湿平衡。
此类 PPA 化合物通常被称为行业中最具耐水解性和最高 Tg 的聚酰胺,但 PPA 仍会遇到从 149°C 降至 68°C 的 Tg 转变。由于 Tg 决定了聚合物的分子流动性,低于 Tg 的聚合物分子被冻结,没有流动性,因此它是刚性的,具有很强的抗蠕变性。高于 Tg 时,分子变得可移动并且能够被扭曲和移动。这种由于吸湿而产生的"软化"效应导致尺寸稳定性和抗蠕变性显着降低。
100% 湿度下 90°C 的工作条件对于燃料电池系统来说是非常典型的。即使具有最高 Tg 的聚酰胺在这样的条件下也会完全湿透,在最初的几百小时运行之后就已经如此。因此,会发生聚酰胺分子的水解降解。
如果燃料电池部件是用聚酰胺制造的,它们的尺寸会膨胀。机械性能,如抗蠕变性、机械强度和模量会下降,导致部件变形。由于在密封界面处引起的蠕变和变形,燃料电池系统面临着很高的故障风险。图 18 总结了机械保留和离子浸出性能与长期水解老化的关系。
图 18:材料耐水解性和离子浸出性能排名
帝斯曼系统地研究了不同聚合物的水解老化机理,并在高温水解溶液中获得了超过 10,000 小时的测量数据。DSM 不仅能够比较高分子化合物的水解性能,还可以预测在水或水/乙二醇系统中长达 30,000 小时的机械保留时间。图 19 显示了基于 Xytron™ PPS G4080HR 的长达 30,000 小时的拉伸强度建模,具有良好的预测精度。
图 19:拉伸模量建模与基于 Xytron ™
PPS G4080HR 的测量数据之间的比较显示模型预测与实际测量数据之间的良好一致性
第 42届
15
图 20:在 95 ℃ Xytron ™ PPS G4080HR 中长达 30,000 小时的拉伸强度保持率预测
图 20 显示了 Xytron™ PPS G4080HR 在 95°C热水中的 30,000 小时拉伸强度预测结果。其极其稳定的机械保持力使其成为业内最好的耐水解材料,性能优于所有 PPA 并显着优于其他标准 PPS,为组件的长期可靠性提供了足够的安全裕度。
概括
先进技术正在彻底改变人类运输的动力系统。PEMFC 燃料电池提供了零排放和最低环境影响的新可能性,这将有助于实现碳中和社会。
PEMFC燃料电池的应用不仅限于汽车,还可以应用于叉车、飞机、轮船和无人机。它是一个具有巨大可能性的技术平台。在许多国家,由于缺乏对制氢和加氢站基础设施的投资,PEMFC 在汽车领域的首次尝试和部署仍停留在商业运输领域,日本除外。在日本,有一项雄心勃勃的政府激励计划来建设氢能社会,日本 OEMS 在其中处于领导地位。
如前所述,不同交通工具的燃料电池核心技术几乎相同,因此构建可靠性最高的燃料电池系统以覆盖大部分交通工具非常重要。例如,商用车辆通常需要超过 15,000 小时的使用寿命。因此,选择第一次使用正确的材料将避免燃料电池系统的潜在故障,并确保竞争优势。
凭借 DSM 研究多年来所做的全面研究,我们有信心提供满足不同燃料电池组件要求的材料选择。在所有潜在的工程材料中,PPS 已被确定为最适合燃料电池系统的聚合物,因为它具有固有的优异性能,例如耐化学性、耐水解性、优异的尺寸稳定性和低离子浸出。
借助 DSM 创新接口技术,我们能够创建 Xytron™ PPS 燃料电池平台,该平台具有:
-
同类产品中最低的离子浸出率,确保最高的燃料电池效率和使用寿命;
-
在水解环境中保持最佳强度和韧性(在所有工程塑料中)——它优于其他 PPS 和 PPA,为工程师提供最大的设计灵活性
-
同类产品中最佳的尺寸稳定性、抗疲劳性和抗蠕变性,即使在老化后也能确保系统在其使用寿命内的高可靠性
-
水解和热老化前后的最佳焊缝强度,确保最高的机械可靠性
目前,借助 Xytron™ PPS 燃料电池平台,帝斯曼能够提供三个等级:
-
Xytron™ PPS G4080HR(标准)
-
Xytron™ PPS + 30%GF+ 抗冲改性剂,具有更好的韧性
-
Xytron™ PPS + 40% GF + 冲击改性剂,用于平衡强度和韧性
帝斯曼战略方向的一部分是专注于 PEMFC 并对其进行投资。我们致力于与工业伙伴合作,推动这项有前途的技术向前发展,用我们明亮的科学创造美好的生活。
要了解有关 DSM PPS Xytron TM等级的更多信息,您可以联系以下人员或访问我们的网站:
-
于斌-全球电动汽车技术专家(HEV、PHEV、BEV、燃料电池)Bin.yu@dsm.com
-
Tamim sidiki-全球汽车营销总监;Sidiki.tamim@dsm.com
-
邱军——欧洲应用专家和化学科学家;
Qiu.jun@dsm.com
-
Pot Abel- 欧洲应用专家
Abel.pot@dsm.com
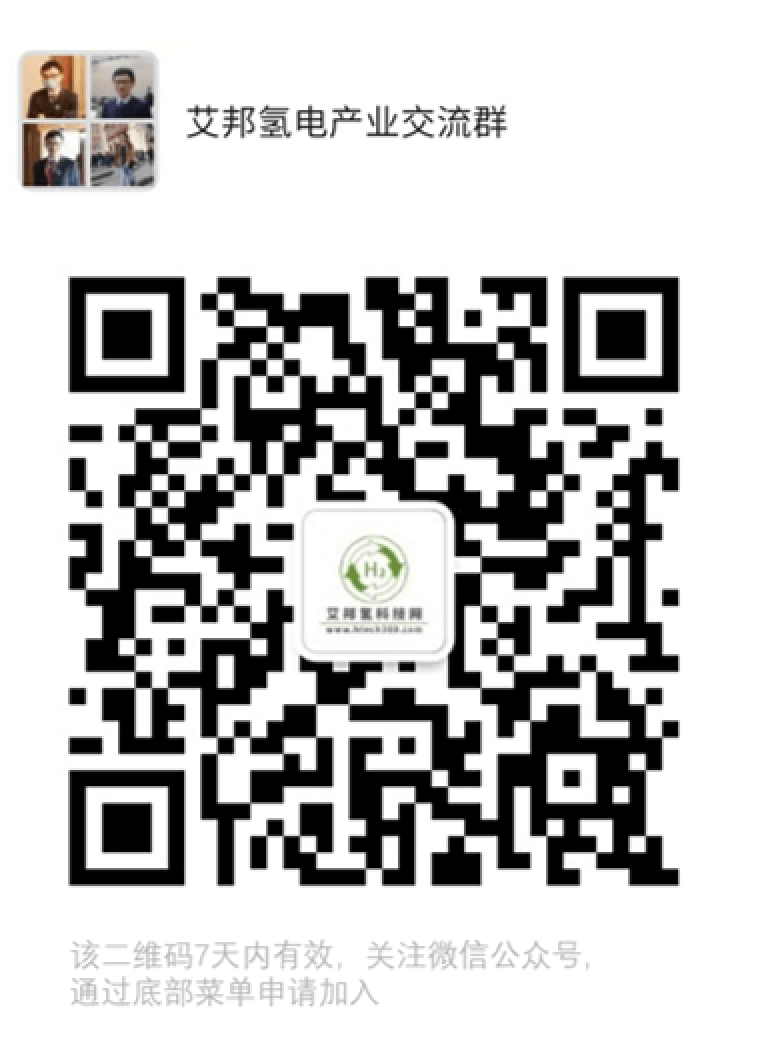