摘要:
在燃料电池商业化极具紧迫性的现状推动下,为缩短设计周期、节省设计成本,我们认为有必要在燃料电池的设计开发中引入仿真分析手段。为提升燃料电池的性能均一性及运行可靠性,通常对电池执行流体仿真工作。对于单电池流体仿真,可以直接物理建模,通过质量守恒方程、动量守恒方程的数学模型研究各流道间的流体流动状况,为双极板设计(/改善)提供指导。而对于电堆流体仿真,新源动力基于多年开发经验引入了多孔介质的数学模型,实现了数百节电堆的全尺寸流体仿真,量化了各单池间的流量分配差异性,为电堆歧管、气口端板、公共通道的结构提供深入理解和设计指导。

1 引言
在我国节能减排、“碳达峰”、“碳中和”的大背景下,适用于车载应用场景的质子交换膜燃料电池(PEMFC)已成为新能源技术的研发焦点。
新源动力股份有限公司作为中国第一家致力于燃料电池产业化的企业,在PEMFC的设计开发过程中积累了丰富的研发经验,在缩短设计周期、节省设计成本的理念推动下进行了多年的电池仿真工作,主要包括流体仿真、结构仿真、系统仿真、电控HIL仿真,等等。本专题介绍在PEMFC单池及电堆设计中的流体仿真工作。
PEMFC包含阴极、阳极、冷却腔体,分别为氧化剂、还原剂、冷却剂提供流动通道。当电池结构设计不合理时,存在流体分配不均匀的可能性。另一方面,PEMFC设计者和客户都有提升电池性能均一性的诉求,而流体分配状态会直接影响电池性能均一性。最理想状况下,我们希望单池及电堆在进行化学反应时,单电池的各部位之间、电堆的各单池之间流体分配浓度相同、反应速率相同。以此保证电池具备较好的性能均一性,提高电池运行可靠性及电池寿命。
然而,PEMFC各腔体实现流体均匀分配会存在一些障碍。单池的障碍主要在于双极板结构,主要分两个方面:双极板由“沟”和“脊”组成,“沟”下的质子交换膜(MEA)比“脊”下更容易获得反应物,这就必然导致“沟”和“脊”处的反应速率不同;另一方面,双极板的关键作用是要能够同时对氧化剂、还原剂和冷却剂进行分配和隔离,每种流体至少要有一进一出两个接口,所以一张双极板上至少要有六个流体接口,造成流体向各流道的供给路径不同,因此引起各流道内反应物浓度不同。前者障碍可以通过MEA性能的提高进行改善,后者障碍则需要通过流体仿真的指导进行改善。电堆的障碍主要在于电堆是由数十节甚至数百节单池串联而成,各单池的流体进出口距电堆进出口的流经路径有差别,因此造成各单池间流体分配不均。需要通过流体仿真,优化电堆歧管、气口端板、公共通道的结构设计。
+ + + +

2 电池流体仿真模型
2.1 物理模型
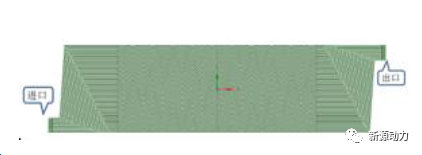
图1 双极板单侧腔体物理模型
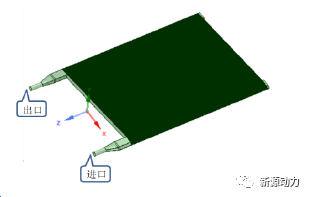
图2 电堆单侧腔体物理模型
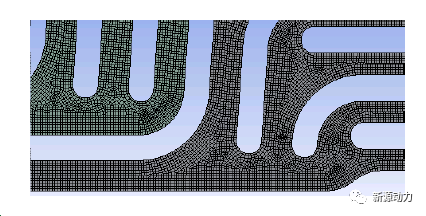
图3 双极板单侧腔体结构网格

图4 电堆单侧腔体结构网格
2.2 数学模型
单电池流体仿真的流体域网格量在五百万左右,采用一般的流体仿真服务器就可以进行计算,为提高求解精度,不对单电池的物理模型进行简化。在流场中,当不考虑物质的消耗时,其流动过程中质量守恒。对于控制体,流入与流出的质量之差等于控制体内质量的增量,所以质量流动满足方程:

式中,V是控制体体积,A是控制体的控制面,t表示时间,ρ表示密度,表示矢量速度,n表示控制体的单位法向量(指向控制体外部)。等式第一项表示质量增量;等式第二项表示通过控制面的流通量(流出是正,流入是负)。根据奥-高公式,在直角坐标系下,上式可转化成微分形式:
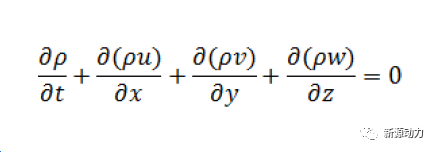
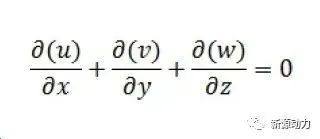
另一方面,流场的动量时间变化率等于作用于流场的外力总和,所以对于控制体满足动量守恒方程:
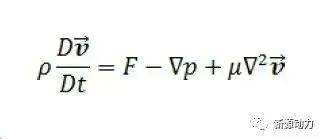
式中,F表示控制体受到的外力,p表示压力,µ表示流体动力粘度。在直角坐标系下,当流动是稳定状态时,可忽略上式的瞬态项,变成以下形式:
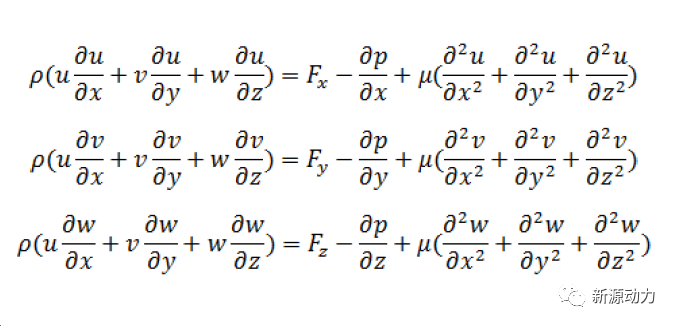
电堆的流体仿真比较复杂,对于数十甚至数百节单池组成的电堆,对空气、氢气、冷却剂单个流体域进行网格划分时,网格量就可达1亿~1.5亿,已远远超过常规仿真工作站的计算能力。通过分析发现,电堆流体仿真工作的目的在于研究和改善单池彼此之间的流体分配均一性,而不是研究各单池内的流动细节。所以能够把电堆中的各单池想象成多孔介质,将单池简化成增加了流动阻力源的流体区域,其阻力源提供一个与速度相关的动量源项:
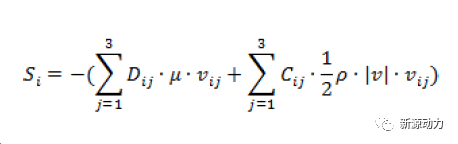
式中,Si是第i(x,y,z)方向的动量源项;D与C是阻力系数;右侧第一项是粘性损失项;右侧第二项是惯性损失项。对于均匀多孔介质,上式可写为:
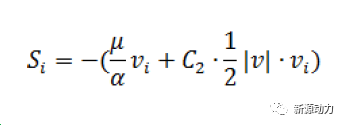
式中,α是渗透率,C2是惯性阻力系数。此时D等于1/α。
动量源项作用于流体在宏观上表现为多孔介质在流体流动方向上产生了一个负的压力梯度,即:
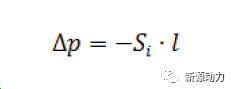
+ + + +

3 电池流体仿真的应用示例
对于单电池流体仿真,采用图1、图3的物理模型和网格结构,同时采用单电池三个工况下的操作条件作为仿真的边界条件进行数值求解,如表1所示。
表1 单电池流体仿真边界条件
由于双极板的微流道结构,采用试验手段是得不到各流道流量差异性的。通过流体仿真计算得出在工况1的边界条件下双极板各流道的流量分配如图5所示。由图可见,能清晰区分各流道的流量分配趋势,量化了单池流道的流量分配差异性,以此为双极板设计(/改善)提供指导。另外,仿真求解了三个工况下的单池进出口压力降,如表2所示,用于电堆流体仿真。

图5 单池各流道的流量分配仿真结果
表2 单池流体仿真压力降
对于电堆流体仿真,采用图2、图4的物理模型和网格结构,同时采用电堆在某工况下的操作条件作为仿真的边界条件进行数值求解,如表3所示。
表3 电堆流体仿真边界条件
根据第2.2节对多孔介质模型的描述,进行电堆流体仿真之前需要先进行渗透率α、惯性阻力系数C2的拟合求解。根据表2数据,拟合成以下形式:
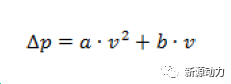
具体地,
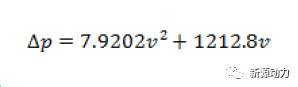
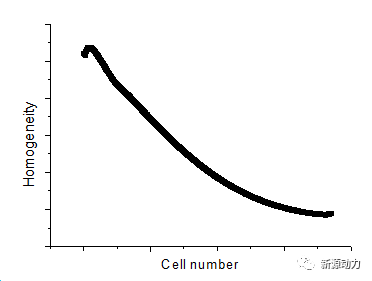
图6 电堆各单池的流量分配仿真结果
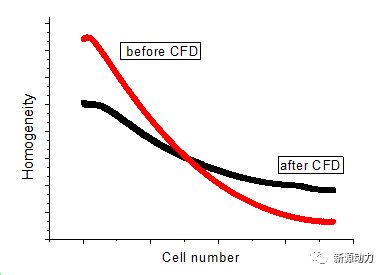
图7 优化前后电堆各单池流体均一性比较
+ + + +

4 结论
对于单电池流体仿真,可以直接物理建模,通过质量守恒方程、动量守恒方程的数学模型研究各流道间的流体流动状况,为双极板设计(/改善)提供指导。对于电堆流体仿真,新源动力基于多年开发经验引入了多孔介质的数学模型,实现了数百节电堆的全尺寸流体仿真,量化了各单池的流量分配差异性,为电堆歧管、气口端板、公共通道的结构提供深入理解和设计指导。
+ + + +
未经授权不得转载!
作者:赵洋洋 编辑:孙婷
往期推荐

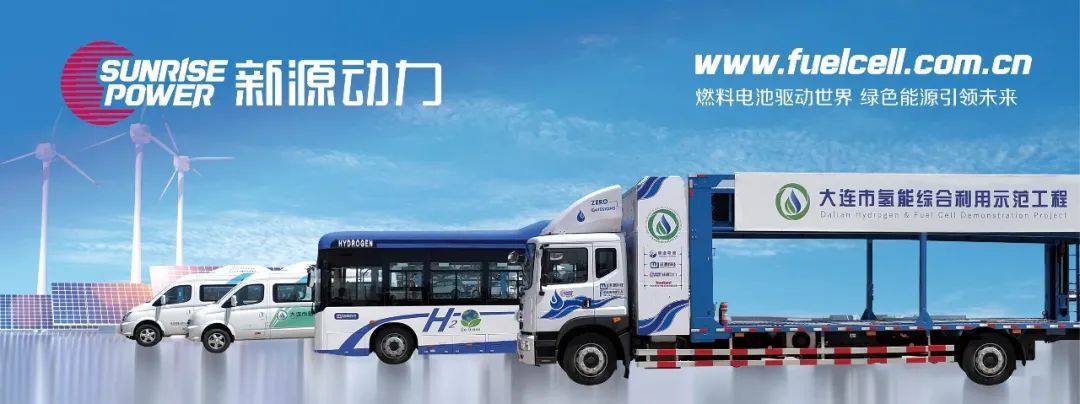
原文始发于微信公众号(新源动力):技术专题 第八期 | 流体仿真是如何在燃料电池开发过程发挥关键作用的
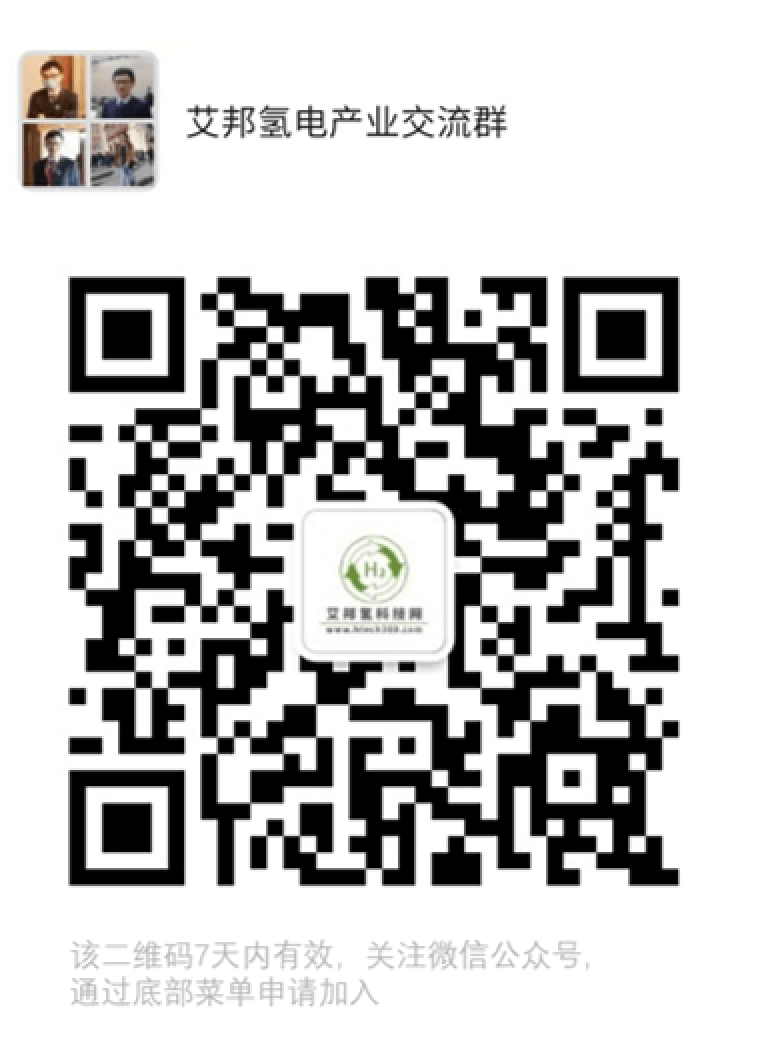