氢 能 华氢汇智能科技(浙江)有限公司
氢 能 华氢汇智能科技(浙江)有限公司
当前PEM电解槽电堆的电流密度通常为2A/cm²,通过设计改进,有望将其提升至6A/cm²。更高的电流密度可以直接提升功率密度,从而减少单位功率下的材料消耗与设备体积,降低生产成本。
电堆的电极面积目前一般为1500-2000cm²,而未来随着技术的进步,电极面积可能会扩大至5000cm²,最终达到10000cm²以上。为了适应这种规模的扩展,可以采用相同厚度但更坚固的膜,通过串联来支持更大面积的电堆单元。这些设计改进将有助于提升PEM电解槽的单堆功率,从目前的1MW提升至5MW,甚至10MW,从而提高电解系统的经济性。
尽管功率密度提高,但实际运行时需保持较低的电压,以提高能效并简化废热管理。低电压下运行不仅可以减少电堆的电力损耗,还能减少冷却系统的负担,从而进一步优化成本。
降低膜厚度以提升效率与减少能耗
质子交换膜是PEM电解槽的核心组件之一,其厚度直接影响到电解过程的能效和电堆的稳定性。目前市面上主流的质子交换膜是Nafion N117膜,厚度为180μm,在2A/cm²电流密度下运行时,效率损失约为25%。然而,近年来一些膜的厚度已降至20μm,在相同电流密度下,效率损失减少到约6%。
尽管降低膜厚度能够提高效率并降低能耗,但膜的厚度预计不会降至5μm以下。这是因为膜的机械强度会随着厚度降低而下降,导致其耐久性不足。尤其是在高压差条件下,过薄的膜容易受损。此外,薄膜的使用还对生产工艺提出了更高的要求,特别是在催化剂涂覆与PTL结合时,薄膜的机械鲁棒性至关重要,必须保证其在较大面积上能均匀承受压力并避免损坏。因此,在减薄膜的同时,确保其机械性能的平衡十分关键。
氢
能
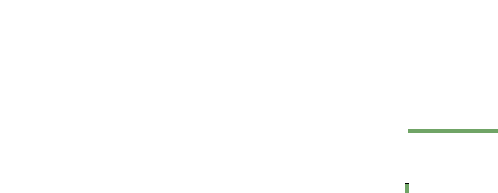
华氢汇智能科技(浙江)有限公司
优化多孔传输层(PTL)与双极板设计,减少昂贵涂层的使用
多孔传输层(PTL)和双极板是PEM电解槽的重要组成部分,特别是在阳极侧,PTL通常由涂覆铂的钛烧结多孔片构成。钛材料易于钝化,因此涂覆铂可以起到保护作用,同时铂还能有效降低层间电阻,提供优异的导电性。当前PTL的铂负载量通常为1-5mg/cm²,或约12.5g/kW。然而,铂的高成本对系统的整体成本有很大影响。研究表明,PTL的层间电阻可能导致1.35kWh/Kg H2的电力损耗,约占氢气低位发热值(LHV)的4%。
未来的降本方向包括减少或替代钛材料。目前研究的替代材料包括铌、钽和不锈钢,这些材料可以在特定条件下替代钛,并减少甚至完全避免铂或金涂层的使用。此外,研发新型的保护涂层,使其在确保材料耐腐蚀性和稳定性的同时,不含贵金属,从而进一步降低材料成本。
催化剂涂覆膜的优化设计与自动化生产
催化剂涂覆膜的生产工艺是影响PEM电解槽成本的另一重要因素。通过生产自动化,建立可靠且低成本的催化剂和膜供应链,可以大幅降低生产成本,并提升制造效率。自动化生产能够实现规模化效应,从而使催化剂和膜的单位成本显著下降。
同时,通过优化电极设计,特别是催化剂在膜上的分布方式(如并行设计等),可以减少催化剂的使用量,而不影响催化效率。这一技术改进能够显著减少贵金属催化剂的用量,进一步降低系统成本。
目前,PSFA膜的供应商相对稳定,主要包括Chemours、Solvay、Asahi-Kasei、3M和Gore等。这些供应商已实现规模化生产,膜的面积可以达到3m²,能够满足大规模PEM电解槽的需求。随着膜生产规模的进一步扩大,供应链的完善将使PEM电解槽的成本进一步降低。
氢
能
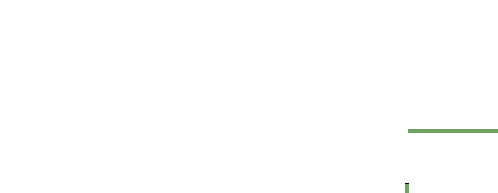
华氢汇智能科技(浙江)有限公司
电解槽|极框垫片自动裁切机
Ø设备功能
本设备实现电解槽极框垫片的自动裁切。
Ø设备参数
1.重复定位精度:±0.02mm;
2.垫片切割速度:1.5m/min;
3.垫片尺寸切割精度:±0.1mm。
Ø设备优势
1.本设备切割出的垫片边缘光滑无毛刺;
2.可一次性完成切割多种孔图案,兼容性高;
3.切割头具备自矫正功能,减少了操作者的装配时间。
原文始发于微信公众号(华氢汇智能):PEM电解槽的降本途径
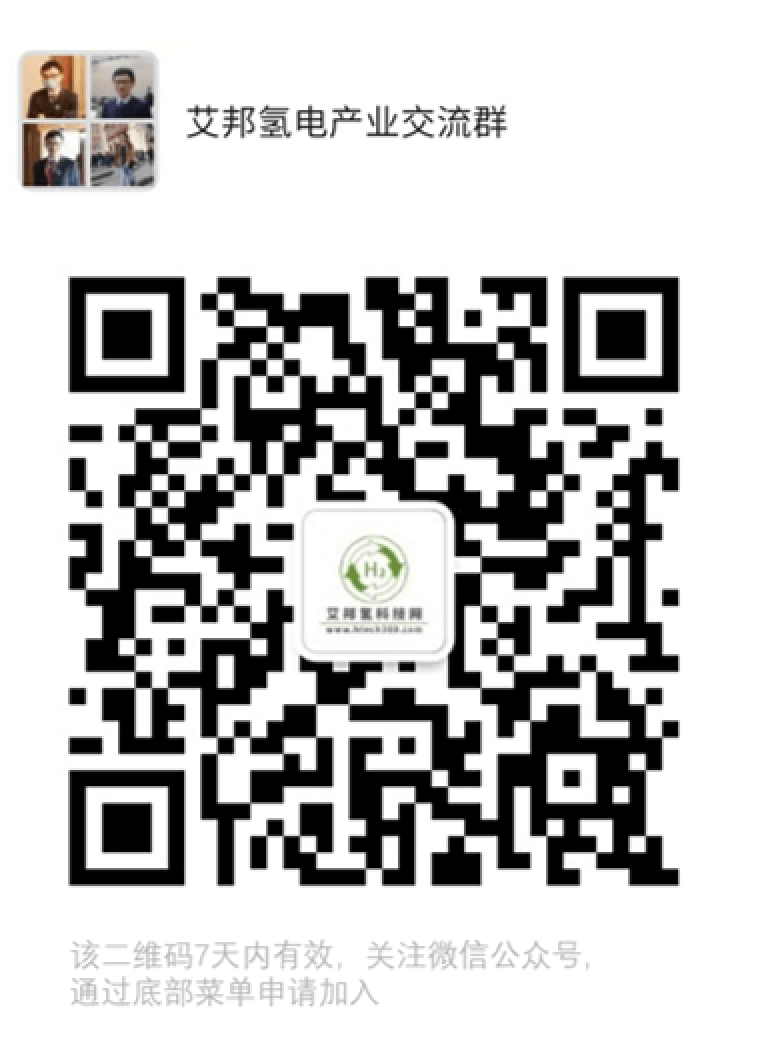
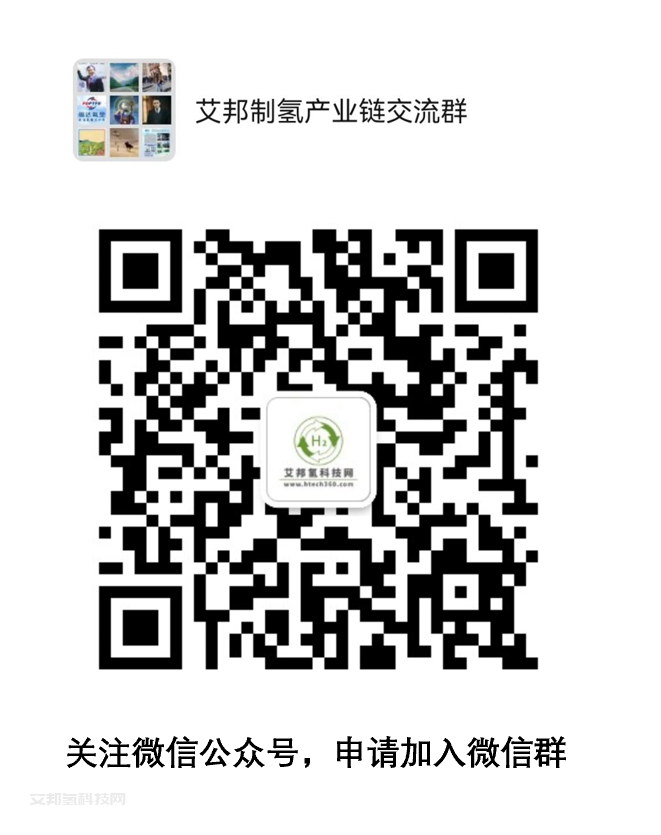