三一氢能通过创新仿真技术的应用,成功应对电解槽开发过程中的诸多难题。三一氢能完整的电解槽结构-流场-温度场的仿真体系、电化学仿真以及整机结构强度的仿真验证方法提高了电解槽可靠性和稳定性,为氢能行业高质量发展提供保障。 电解槽,尤其是大产气量的碱性电解槽,其内部气液流动状态极为复杂,对电解槽的表观性能和潜在寿命有着直接影响。由于极板直径大、进出口位置距离远以及小室空间小等因素,气液流体在内部往往处于不均匀分布和流动状态,导致局部流体滞留和回流现象。这种流体滞留不仅会造成电解余热积累,使局部温度高于其他部位,还会对隔膜、电极和极板造成不同程度的损伤。因此,深入了解和优化电解槽内部的流体流动状态及温度分布,对于提高电解槽的性能和可靠性至关重要。 传统电解槽的开发主要依赖经验积累和尺寸放大,以实现产气量的提升。然而,这种方法忽视了尺寸放大对流体流动状态的不利影响,导致大产气量电解槽的可靠性问题频发。为了提升电解槽的开发质量,必须对其内部的流体流动状态和温度等因素有直观的认识,从而避免相关问题的发生。 三一氢能依托三一集团资源,建立了完整的电解槽结构-流场-温度场的仿真体系、电化学仿真以及整机结构强度的仿真验证方法,可以自主完成电解槽仿真模拟工作,赋能产品研发和工艺设计的迭代优化。 结构-流场-温度场仿真 电解槽结构设计方面,三一氢能建立了完整的电解槽结构/流场/温度场/多物理场的耦合仿真体系,指导电解槽整体结构的迭代优化,有效提高电解槽流场/温度场均匀性,对于提高电解槽长期运行的稳定性、降低电解能耗具有重要作用。 针对电解小室内复杂的气液流体流动状态,通过构建电解槽三维仿真模型,模拟极板结构对流体流动及传质传热过程的影响,通过调整液道孔和气道孔数量及位置、调整极板凹凸点高度及排布规律等方案,研究电解小室内气液流体流动和传质传热过程的变化规律,获得最优结构,有效提高电解槽小室碱液流量分配的均匀性和温度分布的均匀性,解决槽体超温问题,降低电解槽能耗。 (图:电解小室流体流向仿真) (图:电解小室温度分布仿真) 在槽体核心零部件选型过程中,三一氢能将极板结构和电极材料相结合,建立完整的电化学仿真模型,用DOE方法论分析优化乳突高度、各结构关键尺寸等对能耗、产氢量等指标的影响,优化零部件组合,解决电极、极板接触内阻大的问题,降低内阻导致的电压降,降低电解能耗。 (图:电解小室电化学仿真) 三一氢能针对零部件加工、槽体组装等过程涉及的零部件运输、吊装等工序的要求,利用材料物性参数结合结构仿真模型,模拟端板、双极板等组件在各种吊装状态下的形变,为组件减薄与其性能达到有效平衡提供参考。 未来,三一氢能将继续聚焦圆形槽、方形槽、PEM 槽、BOP 的“3+1”技术路线,不断完善并强化集成设计、材料研发、仿真分析、试验验证、电气控制、制造工艺、氢安全设计等七大核心能力。同时,三一氢能期待与行业客户、设计院、供应商、科研院所、行业机构等深化合作,共谋氢能装备的高质量发展,为实现“双碳”目标贡献三一的力量与与三一方案。
原文始发于微信公众号(三一氢能):三一氢能|创新仿真技术破解电解槽开发难题
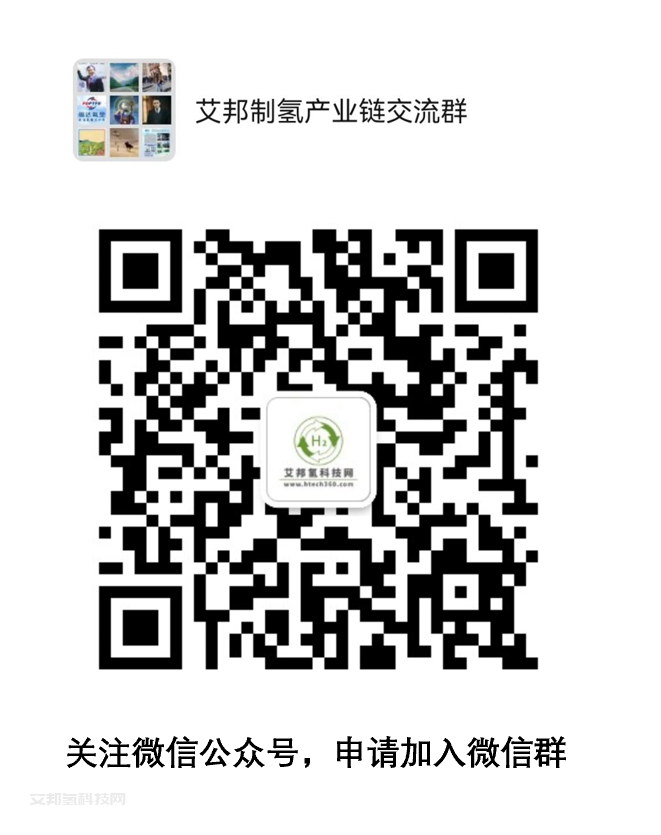