在过去的十年里针对零间隙碱性电解的研究表明,透过“Zero Gap”设计的电解池性能可以实现显著提高。通过采用更紧凑的电池设计,这可以为碱性电解的性能提供一个阶梯式提升变化的潜力,如下图所示,传统设计与零间隙设计的主要区别在于使用多孔电极而不是金属板(还有一个区别在于极板流场也在发生变化)。这使得电池具有非常小的电极间隙,紧凑的设计和很高效率。它迫使气泡从电极的背面释放出来,减少了它们对电池电解电压的增加(减少了气液混合相里面大气泡导致电阻增加导致电耗增加)。
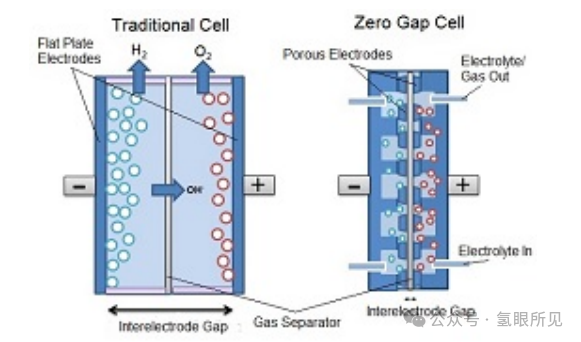
零间隙碱性电解
零间隙碱性电解是通过压缩氢氧离子传输膜或气体分离器(隔膜)两侧的两个多孔电极来工作的。这使得两个电极之间的间隙等于膜的厚度(<0.5 mm),而不是传统设置的(> 2mm),从而显着降低了两个电极之间由大量电解质产生的欧姆电阻。气体扩散层提供从多孔电极到双极板的电气连接,同时允许电解溶液的进料补给,并去除气体产物(请仔细琢磨这里的结构)。
1967年,Costa和Grimes首次提出了零间隙碱性电解,在微孔气体分离器(隔膜)两侧使用网状电极(基本上目前多数已经做到了这一点)。当代的重要研究表明,零间隙设计的电解池电流密度可以大幅增加。最近的研究主要集中零间隙结构在阴离子交换膜电解槽上的开发,它具有低阻值和在差压下操作的潜力。包括使用高比表面积的泡沫电极等新的电池设计也被开发出来了,以及采用直接沉积在(隔/分离)膜上的类似燃料电池类型的膜电极(MEA)方式。与传统方法相比,零间隙设计更为复杂,因此结构部件也有所不同。零间隙电解槽采用多孔电极压在蚀刻或冲压的流场板(双极板)上,而不是采用于有限间隙电解的单一平板类。催化剂材料要么直接沉积在多孔电极上(现状较常用),要么直接沉积在膜上(AEM技术尽可能采用该方式),而传统的设计是将催化剂直接沉积在平面极板上(这已经是一种很古老的做法了)。现状用的电催化材料都可以直接转移到新的设计中,只是沉积(涂覆)方法可能需要调整以将材料沉积到多孔基板上。两种电池设计都可以使用相同的气体分离器(隔膜),但是零间隙设计开辟了与阴离子交换膜一起工作的可能性(结构趋同性)。
基于镍网/泡沫镍的多孔电极已经在许多碱性电解系统中使用。另涂层不锈钢在阴极方面使用也是一种可能性,尽管不锈钢在氧气存在的情况下受到高电位影响会发生氧化腐蚀。碳布(碳毡)已经被用于碱性燃料电池(阴极侧),由于在高电位下易被氧化,所以它不适合用于阳极侧。
双极板必须具有良好的导电性、低接触电阻和耐腐蚀性。钛由于成本较低通常用于PEM电池,基于不锈钢和镍的板材是碱性电解槽的最佳选择。石墨板可用于碱性燃料电池(AFC)的双极板,但在阳极侧经历的高电位使石墨类材料不适合碱性电解的这一侧。对固体聚合物燃料电池(PEMFC)的界面电阻分析,对使用材料进行了比较,表明随着时间的推移,电阻的增加是由于在极板表面形成了不溶性氧化层。虽然电催化和气体分离器(隔膜)材料的特殊特性对于指导个别领域的适当发展很重要,但它们在完整工作单元中的应用对于证明它们在更大规模上的可行性更重要。
膜电极组装
零间隙设计的组件中心部分称为膜电极组件(MEA),包括与膜两侧接触的两个多孔电极。有不同的方法来生产MEA,可分为两大类:催化剂涂层附着在底物基体上(CCS)和催化剂涂层附着在膜上(CCM)。
这两种方法都采用多孔电极,这提供了增加活性表面积的额外好处,因此对于相同的材料和电池设计,可以实现更高的电流密度。电池的性能取决于催化剂和膜的选择以及电池设计,这使得不同电池设计之间的比较难以量化。零间隙电池的面电阻(Ω·cm2)包括膜电阻,以及电池各层之间的任何界面接触电阻,该值允许在类似的零间隙电池之间进行一定程度的比较,并且有助于指导电池设计在整体电池性能中的重要性。
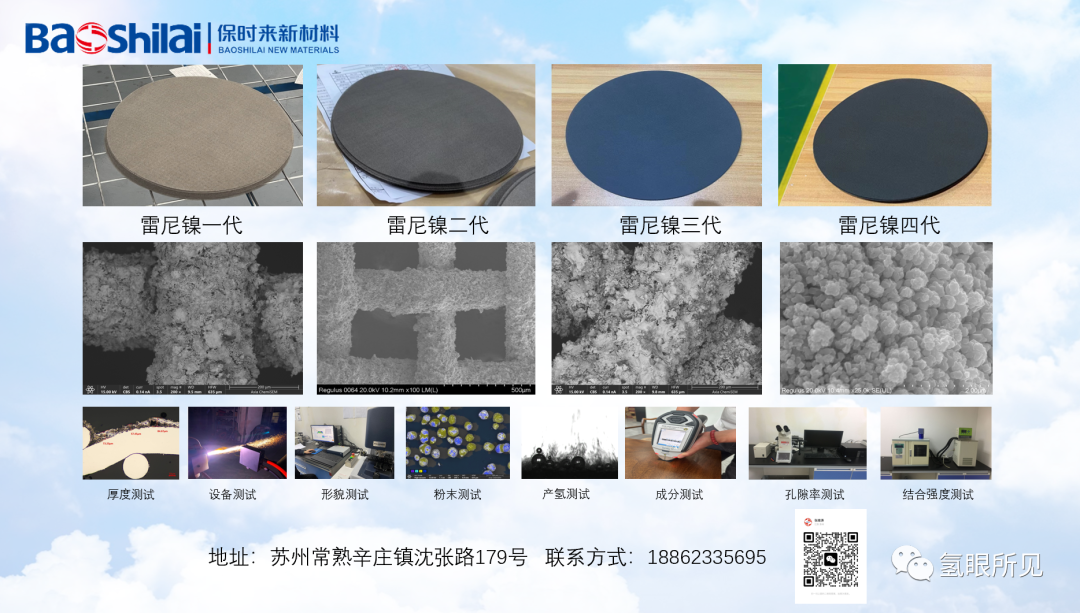
原文始发于微信公众号(氢眼所见):“zero Gap”(零间隙)碱性电解槽的设计
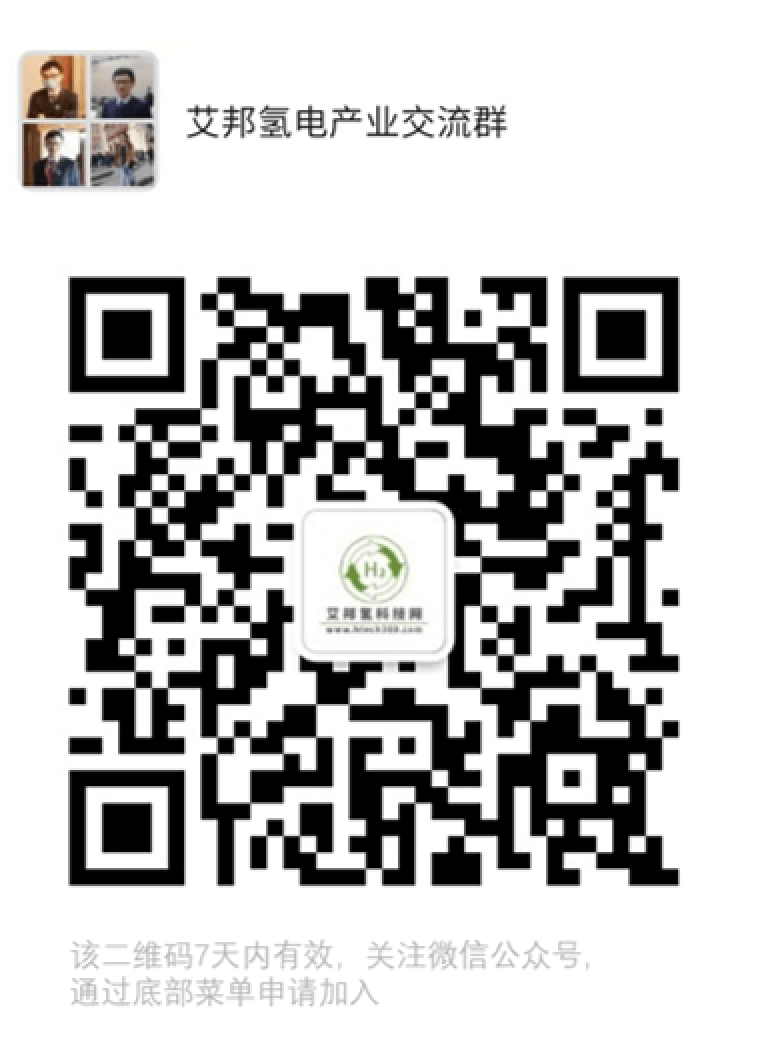