说明:氢气纯化方式这么多年来,未发生重大的技术突破。本章节非常有参考意义。
第五部分 氢气纯化
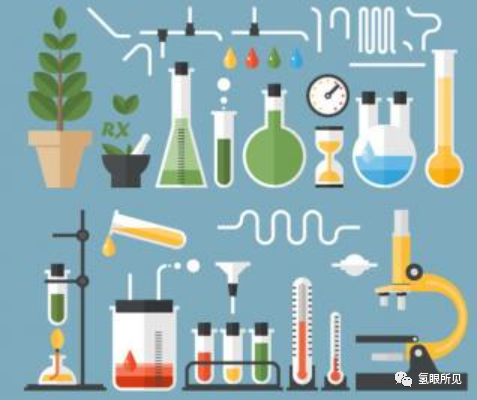
在水电解过程中,由于隔膜并不能绝对阻隔氢气和氧气相互渗透,特别是在氢与氧两侧压力相差大的情况下,又因为电解液是不断循环的,在分离器里,氢气、氧气和电解液是很难达到完全分离,所以工业上用水电解法制得的氢气里含有杂质氧,一般在0.5%以下。又由于制氢过程是气液共存的,所以氢气中还存在饱和含水量。这些杂质的存在,对于现代工业生产和科学研究是很不适应的。例如半导体材料硅的生产,对氢气中的含氧量要求在5ppm以下,含水量要求露点在 -50℃以下,不然的话,氧会溶解在硅里,改变单晶硅的电阻率,甚至导致导电类型的改变。又如金属高温热处理、粉末冶金、微电子电路、光导元件、化学合成等生产过程中,如果氢气中含有少量的氧或水分,那么高温下会使原材料发生氧化,这是因为高温下金属能直接与氧化合,也能夺取水中的氧形成氧化物,这将严重影响材料的质量。随着生产的发展和技术的进步,氢气的应用范围已越来越广泛工艺过程对氢的纯度要求也将越来越高。工业上纯化水电解氢的方法主要是催化脱氧加吸附干燥,纯氢中的杂质残含量<1ppm,露点可达-80℃,已能满足许多部门的需要,所以本章主要讲述此法。
当原料氢中各种组分较多,又对产品氢纯度要求很高时,可采用变压吸附法(见第一章及本章降压再生)钯合金膜扩散法、低温吸附法、金属无机膜分离法、金属氢化物法等,把多种杂质同时去除。
第一节催化脱氧
一、催化脱氧的原理
催化脱气就是利用催化剂(俗名触媒)使氢和存在于气体中的杂质氧发生化学反应而生成水,从而达到除掉杂质氧的目的:

为什么催化剂能够加快氢和氧之间的反应呢?目前虽然还没有彻底弄清楚原因,但人们认为:这与催化剂本身能大量吸附溶解气体的性质有关,因为当催化剂吸附溶解了大量气体之后,等于把气体浓缩了,这就增加了氢氧分子相互碰撞进行化学反应的机会,而当一些氢、氧分子发生了化学反应,放出热量使温度升高,又反过来促进其它氢、氧分子进行化学反应。
氢与氧的催化反应几乎都在催化剂表面进行,所以要加快反应速度就得增加催化剂的表面积,使氢与氧在催化剂表面有良好的接触条件;另外则要求气体能迅速地扩散到催化剂表面,增加氢与氧之间的接触机会,这就是要提高气体的流速。催化脱氧的气体流速,通常用空间速度来表示,所谓空间速度就是单位体积的催化剂,在单位时间里所能处理的气体体积,它的单位为“m3气体/m3催化剂·h“”简化为h。提高氢气的空间速度对催化脱氧有利,但气流流速不能无限加快,不能使氢与氧在催化剂表面还没有来得及反应就被气流冲走了,所以每一种催化剂都有一个适当的空间速度。
二、催化剂及其性能
脱氧催化剂活性最高的大多是元素周期表中第Ⅷ类展性重金属元素,如钯(Pd)、铂(Pt)、银(Ag)、镍-铬(Ni-Cr)、铜(Cu)等。把这些金属元素附在多孔性物质上,常用的载体有浮石、硅藻土、活性氧化铝、分子筛、硅胶、活性炭、碳纤维半导体粉末等;制作的方法有:机械混合、浸渍、共同沉淀、离子交换等方法。所制得的催化剂必须有合适的形状,巨大的表面积,足够的机械强度,良好的化学稳定性和耐热性。常用的氢气脱氧催化剂有以下几种:
1)0603型铜催化剂
它是用氧化铜附在在硅藻土上,制成直径6x6mm的颗粒,堆比重~1kg/L,工作温度为200~250℃,空间速度为3000~5000/h,当初含氧量为<1%时,脱氧后残含氧量<10ppm。该催化剂在使用前,应该用氢气或氢、氮混合气以3000/h的空速进行活化还原处理,当还原气出口温度升至200℃后,残含氧量达到所规定的纯度时即可投入使用。

脱氢时工作温度为200~250℃,气体空速为2000~3000/h,脱氢能力可根据需要而有所不同,残含氢量可达到<1ppm。
2) 651型镍铬催化剂
它是用镍、铬附在多孔性物质上,制成直径5x5mm的颗粒,堆比重为1.1~1.2kg/L,工作温度为50~100℃空间速度为5000~8000/h,当初含氧量<3%时,脱氧后残含氧量<5ppm。该催化剂在使用前,应该用氢气在200℃下,以3000~5000/h的空速进行活化还原4~5小时,当出口氢中含氧量达到要求,即可投入使用。活化后的催化剂呈黑色且有光泽遇空气要燃烧,长期不用时应充水或充氨保护,短期不用时,应保持气气正压,防止倒吸空气。如果原料气中存在碱雾、酸雾SO2、H2S、CO、NO2、NO等杂质,均会影响催化剂活性。
3) 105型分子筛
它是用钯负载在A型分子筛上加工制作而成,堆比重约~0.7kg/L。采用钯分子筛,原料氢气必须预先进行干燥,否则将影响催化剂的活性。催化反应可在常温或120~150℃下进行,空间速度为5000/h,当初含氧量<1%时,残含氧量可达0.25ppm。在常温工作时,本催化剂需要定期进行再生。“105”型催化剂在使用前应进行活化还原处理,其方法与分子筛使用前活化方法相同,活化后吹冷至常温,再以空速为10000/h的氢气常温还原。
4) 活性氧化铝镀钯
它是用钯盐附在活性氧化铝上加工制作而成的一种高活性催化剂,这种类型的催化剂在国内外都得到广泛的应用。当原料气的温度高于其露点温度10~15℃时,催化反应就可以在不加热的情况下进行。当气体空速为5000~10000/h,初含氧量<3%时,残含氧量可达0.25ppm。
5) 159系列钯催化剂
159系列是相继开发出来的三代钯催化剂产品,159A、159C型钯催化剂,脱氧深度高,处理量大,价格低,而且在室温下就能将氢气中的氧脱至0.5ppm以下,还不需要再生,已在工业上得到广泛应用。
6) HC-1型催化剂
HC-1型催化剂是用金属氧化物及贵金属钯,负载在Al2O3、CaO、SiO2、MnO2等金属氧化物上加工制作而成,呈黑色小球,堆比重约1.18g/ml。该催化剂具有两种脱氧机理,一是有氢存在下,氢与氧发生催化反应生成水,而达到脱氧的目的;另一是在无氢情况下,脱氧剂本身与氧发生反应使脱氧剂主组分由低价氧化物变为高价氧化物,而达到脱氧目的。
HC-1 型用于氢中脱氧,由于活性高,可高空速下使用,脱氧浓度很宽,催化剂用量小,脱氧效果仍然很好。
HC-1型具有良好抗水性能,在饱和水汽下,不需加热连续脱氧有效;它还具抗NH3、CI2、 H2S等杂质的能力,耐温性能也好,在450℃不因发生烧结影响活性。在常温常压下长期脱氧有效,不需活化再生,在使用前也不需要预先活化处理,可直接投入使用。长期使用不发生粉化与流失。
7) 506系列HT型催化剂
HT型催化剂是用贵金属负载在n型半导体上加工制作而成呈青白色的柱体(2x3、3x4、4x5、5x6mm)颗粒,堆比重为1.1~1.2g/cm3。该催化剂脱氧活性高,除氧深度深,单位时间处理量大,当空速为2000~30000/h,初含氧量<3%时,残含氧量<0.5ppm。它可以在常压~25MPa、常温~600℃下使用,无需再生使用前也不需要活化。它还具有良好的抗水性可在饱和水汽工况下工作而不改变脱氧活性,具有较大的抗NH3、H2S、SO2等中毒的能力。它耐温性能好650℃不粉化、不烧结,仍保持原有的催化活性。由于HT型催化剂具这些特点,就使普氢既高效深度脱氧,又工艺流程简单,操作方便节省能源,长期使用脱氧性能不变。
三、脱氧器
用户根据对气体的纯度要求及催化剂的性能、价格,选择合适的催化剂。催化剂的需要量(G)可根据下式来计算:
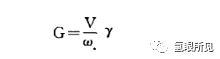
式中:
V-:需纯化的气体体积m3/h:
w:催化剂的设计空速(/h);
Y-:催化剂的堆比重,kg/m3。
也可根据催化剂的处理能力来计算:
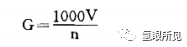
式中:
n--催化剂的处理能力,L/kg.h。
原料气的催化脱氧是在脱氧器里进行的。脱氧器通常做成直立圆筒形,它的高度与直径比,一般采取>3,这样可延长气体与催化剂的接触时间。当氢中含氧量为1%时,催化反应热可使气体温度升高165℃,所以在原料气中含氧量较高时,应特别注意催化剂的过热。为此,可在脱氧器的进口端催化剂层里,加入导热性能好的耐火材料,如粘土碳化硅、刚玉等,稀释催化剂,加长催化反应段。为了安全生产,一级脱氧量不应超过3%。
在使用脱氧器时应注意出口气体温度,因为它是随着原料气的初含氧量和催化脱氧的效果而变化的;应时刻保持系统正压,防止空气倒吸。当脱氧器停止运行需要检修时,应先降低温度并用氮气置换(651型可用水)。
第二节 吸附干燥
气体的干燥方法有很多,可用液体如硫酸、氯化锂、溴化锂、甘油等来吸收气体中的水分,也可用活性固体进行吸收,常用的固体干燥剂有氢氧化钠、氢氧化钾、硫酸钙、氯化钙、过氯酸镁等。电解氢较为普遍的干燥方法是先用低温冷冻法除去大量水,再用多孔性的固体吸附剂进行深度吸附水。
一.吸附的基本概念
吸附是用多孔性的固体吸附剂处理气体混合物,使其中所含的一种或数种组分被吸附到固体表面而达到分离的过程。吸附过程主要是由于固体表面能的作用,其机理甚为复杂,有物理和化学两种因素在起作用。
一般说来,吸附过程都是放热的,所以降低温度将有利于吸附的进行,增加压力也将有利于吸附的进行。吸附剂对于各种溶质的吸附能力,是随着溶质的沸点升高而变大,因高沸点的物质容易凝结,氢气中还含有少量的氧和水蒸汽。氢、氧和水的沸点分别是 -252.7℃、-183℃和100℃,相互之间的差值很大,它们的混合物在与吸附剂相接触时,首先是高沸点的水蒸汽被吸附,而且放出大量的热,而氢几乎不被吸附。
虽然所有的固体表面,对于流体来说都多少地具有吸附作用,但符合工业需要的吸附剂必须具有巨大的内表面,而其外表面仅占总表面的极小部分,故可把它看作是一种极其疏松的固态泡沫。现将氢气净化中几种常用的吸附剂分别作介绍。
二、几种常用的吸附剂
1) 活性氧化铝
活性氧化铝是由r-Al2O3或它与x、η-Al2O3的混合物,在600℃以下脱水制成的。它的比表面积的大小取决于原料、煅烧温度和加热时间。作为吸附剂的活性氧化铝,有吸水能力较强,表面积一般在300m2/g左右,它的机械强度和热稳定性也较好。
2) 硅胶
硅胶是无色、微黄色玻璃状多孔结构的固体,它具有很大的内表面,一般在500m2/g左右,十分亲水,是一种很好的吸附剂。它的分子式可写为:

硅胶的制造过程是用硅酸钠溶液(水玻璃)与硫酸或盐酸作用,使混合物凝结成冻胶,再用水洗去盐类与过量的酸然后干燥、破碎并筛分而成。根据硅胶的内孔径大小,可分为粗孔(孔径>10nm,1nm=10-9cm)和细孔(孔径约3nm)两种。粗孔硅胶的吸附性能较差,主要用来在水蒸汽和气体含量很高时吸附它们,以及用来净化液体,也可用作催化剂载体。细孔硅胶在温度低气体含湿度高相对湿度大、流速慢的情况下具有良好的吸附性能,用来吸附气体中的水蒸汽或其它杂质气体,可用作电解氢的吸附剂。为了防止破裂,在粒状的细孔硅胶中,常常加入4~10%的氧化铝。硅胶在遇到大量水时,会发生崩裂现象而变成粉末状。
用作干燥剂的硅胶有时加入二价钴盐而成变色硅胶,因二价钴盐在无水状态时呈兰色,但在溶液中或含水时晶体则为红玫瑰色。CoCl2·xH2O在逐渐吸水时颜色变化非常明显:

3) 分子筛
分子筛是由粉末状多水合硅铝酸盐晶体,加入粘合剂后塑合而成,呈米白色或带土红色。其化学通式为:
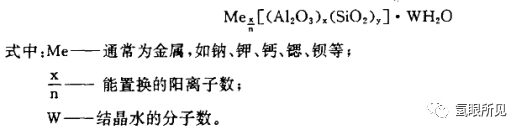
这种泡沸石晶体内部含有大量的水加热脱水后就形成许多大小相同的微孔,它具有很强的吸附能力,能把比孔径小的物质吸收到孔内,而不能吸附大于孔径的分子,从而把大小不同的分子分离开来,起到筛分分子的作用所以叫分子筛。分子筛可根据气体分子的极性、不饱和度和极化率进行选择吸附,对极性分子和不饱和度越大的分子具有很强的吸附力。水是极性很强的分子,分子筛对水有强烈的亲和力。
分子筛不溶于水及有机溶剂,具有很高的抗毒性及热稳定性,在700℃下能保持其晶格及性能不被破坏,且具有很高的催化活性。但能溶于强酸、强碱所以分子筛应在PH=4~12范围内使用。
目前,人工合成的分子筛主要有A型X型和Y型三种。根据分子筛孔径和性质不同,A型分子筛又分3A(钾-A型分子筛)、4A(钠-A型分子筛)、5A(钙-A型分子筛)及其它。3A即表示分子筛微孔直径为0.3nm,4A、5A依此类推。用作脱水的分子筛一般采用5A(水分子的直径为0.289nm)。
分子筛在使用前先要进行活化处理,一般活化温度在450~550℃(常压)或350℃(真空度0.1~1.0pa)。如通气流活化则温度可降低。活化时间应根据分子筛的量而定,1cm厚的分子筛层通常保持活化温度15min即可。由于分子筛本身是热的不良导体,如需活化的数量较多,则活化的时间需相应增加。变色分子筛的活化温度不能超过350℃,不然会影响变色能力。
三、 吸附剂性能比较
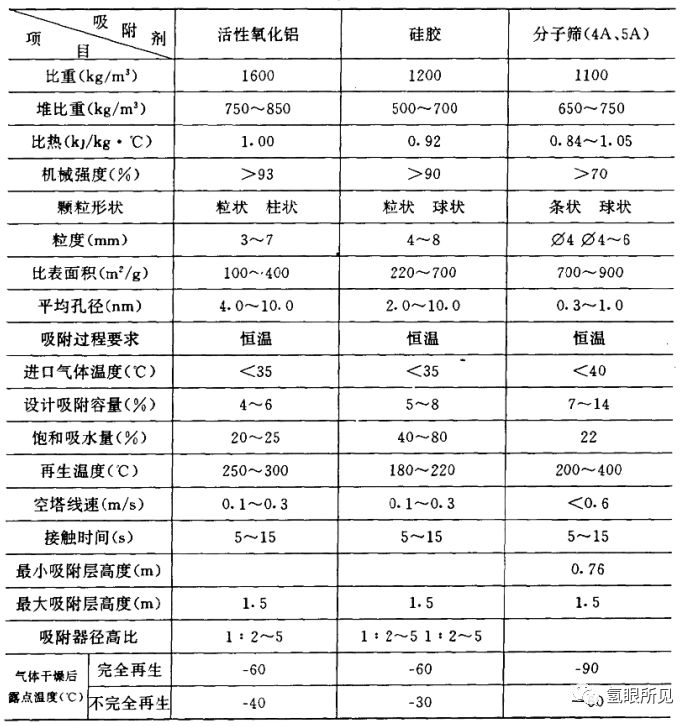
1.对相对湿度低、温度高、流速快的气体,活性氧化铝和硅胶的干燥能力要大为降低,但分子筛仍有较高的吸附作用,可使气体深度干燥及纯化。
2.相对湿度低于30%的气体进行干燥时,分子筛吸水性能比活性氧化铝和硅胶有明显的优越性;当气体的相对湿度高于40%时,则采用硅胶作干燥剂较为合理。
3.工业上在处理湿度大的气体时,有时先用冷冻或加压方法除水,再用活性氧化铝或硅胶脱水,最后用分子筛深度脱水,这样能达到满意的效果。
小结: 吸附剂在低温下干燥效率比较高,但对高温气体进行干燥时,则采用分子筛较为合适。
另,管路系统的材料和组成结构所产生的污染影响是十分明显的,钢管铜管内表面氧化物的存在,由于氢和氧化物中的氧作用,会使氢中含水量增加。实践证明,高纯气体输送管路采用不锈钢材料较为理想,因为不锈钢对杂质及水分的活性较其它材料弱,耐腐蚀及机械工艺性、综合经济性都较好,可以达到百米以上输送高纯气体其纯度“不衰减”。
四、吸附剂的再生
吸附剂吸附水分后其干燥能力逐渐下降,当达到饱和失去吸附能力时,必须停止工作进行再生处理。吸附剂的再生方法,一般采用加热使被吸附的水分脱吸出来,也有采用降压或抽真空的方法。
(一)加热再生
吸附剂在常温或低温下进行吸附,当吸附达到饱和后,加热吸附剂,使被吸附的水分脱吸出来,再使其降温冷却。这样整个过程就分为工作、加热和冷却三个阶段。一般说来温度越高吸附剂的脱吸也就越快越完全,残存含水量越少。但温度过高会使吸附剂的使用寿命相应缩短,吸附性能降低,以至失去吸附作用;反之,温度越低再生就越慢不完全。所以加热再生的温度是根据各种吸附剂的热稳定性而有不同的范围。加热吸附剂的方法,可采用热气流加热并带走水汽。热气流可以是氢气本身进行循环,此法操作方便,但当用户对氢的需要量变化太大时不能适应。这是因为当氢气流量太大时,有限的吸附剂纯化不了过量的氢气;当流量太小时用作加热的气流所带的热量不能满足加热的要求,吸附剂达不到再生温度。但后者可采用加大再生气体的流量,使部分气体返回到原管路进行循环的方法加以解决。有氮气的单位且用户对氢中含氮无严格要求时,也可采用氮气作加热再生气,这样容易降低再生气的含水量,提高吸附剂的干燥度。
再生气体的露点、再生温度对活性氧化铝硅胶和分子筛的残存含水量影响,见图5-3。
例如使露点温度为0℃的再生气体,在150℃温度下均匀加热,活性氧化铝的残存含水量为1.5%,硅胶为1%,分子筛则为5%,而且正因为是平衡状态,所以即使再延长时间也不会再减少了。
吸附剂的吸附能力,随着再生次数的增加最初会下降,但到了一定程度后变化就不大了,所以一般情况下不需要更换,但当吸附剂破碎,影响气体阻力时,需将吸附剂过筛处理。采取加热方法再生的吸附干燥系统见图5-4
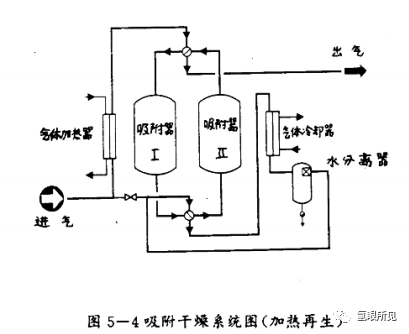
原料气先经过气体加热器加热,再经过上部四通阀,用来加热再生塔I中的吸附剂;带水汽的气流经过下部四通阀至气体冷却器、气水分离器除水,再经过下部四通阀至塔II吸附干燥,产品气经上部四通阀外送。当塔I加热、冷却结束塔I工作结束时,即进行两塔倒换。倒换时两个四通阀必须同步,同步的方法可使两阀杆连接起来。采用四通阀可使管线简化,操作方便,也不至于产生误操作。
(二)降压再生
吸附剂在不同的压力下具有不 同的吸附容量,在较高压力下吸附最大,随着压力降低吸附量也随之降低。根据吸附剂这个特性,在生产中我们可以在较高压力下进行吸附,在常压或抽真空情况下以少量产品气进行脱吸再生,这是变压吸附技术的一项应用。由于这种再生是在常温下进行的不需要加热,所以也称无热再生,应用这种方法可以获得高纯度的气体。由于吸附是在压力下进行,气体中相当量的水分被预先压缩成液体,压力下吸附剂的吸附容量也增大,又降压时被吸附的水分也能迅速脱吸,所以采取降压再生的吸附装置体积小,整个周期可缩短到几分钟,而且容易实现自动化操作。
采取加压吸附、降压再生干燥方法的设备,一般采用两塔式,其中一塔加压吸附,另一塔降压脱吸,见图5-5。
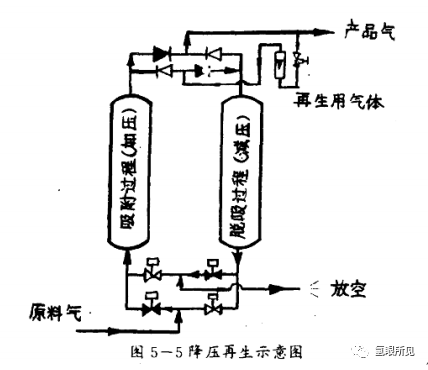
原料气经I塔吸附水分后,干的产品气从出口端引出,其中有一部分经调节阀、止回阀,送入II塔,在降压情况下对I塔进行再生,再生后排空。
吸附与脱吸两个过程的气体产品气 流量之比,等于两个阶段的压力之比:
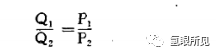
式中:
Q1:吸附塔进气量,Nm3/h;
Q2:脱吸塔再生气流量 Nm3/h;
P1:吸附过程的绝对压力,MPa;
P2--脱吸过程的绝对压 力,Mpa。
利用上式可以计算出降压再生所需的最小耗气量。如果再生气量减少,那再生将是不完全的,会使吸附剂的残余含水量逐渐增加;如果加大再生气耗比,那可使吸附剂再生完全,提高气体干燥度。再生气可以是除水后的产品气,也可另用氮气。
吸附是放热过程,脱吸是吸热过程,为了使吸附热不流失,并用于脱吸再生,那工作周期一定要短,一般在10min左右。如果原料气含湿量低温度低空塔线速低,与吸附剂接触时间长,那有利于提高气体干燥度。在降压脱吸时提高再生气温度,即微热再生,可延长工作周期,减少再生气量。
重要:前面已经连载了五篇,包括:
1.《电解水原理》
2.《电解槽结构》
3.《制氢流程与槽体组装》
4.《电解水制氢生产流程与组装》
5.《电解水制氢如何节能》
6.《电解水制氢的纯化》 本章内容
7.《气体的分析方法》 ......
8.《安全技术》 ......
有兴趣的请往前翻公众号。
原文始发于微信公众号(氢眼所见):电解水制氢读书笔记之【氢气纯化】