
点击上方“蓝字”,关注更多精彩

氢气高能量密度、高还原性以及清洁性特点,让氢能拥有广泛的应用场景。在全球环保趋严的背景下,氢冶金技术不但从根本上实现钢铁生产碳排放为零的可能,而且还降低高精钢材性能低、质量不稳定等问题,对我国钢铁产业升级和高质量发展具有重要实践意义。
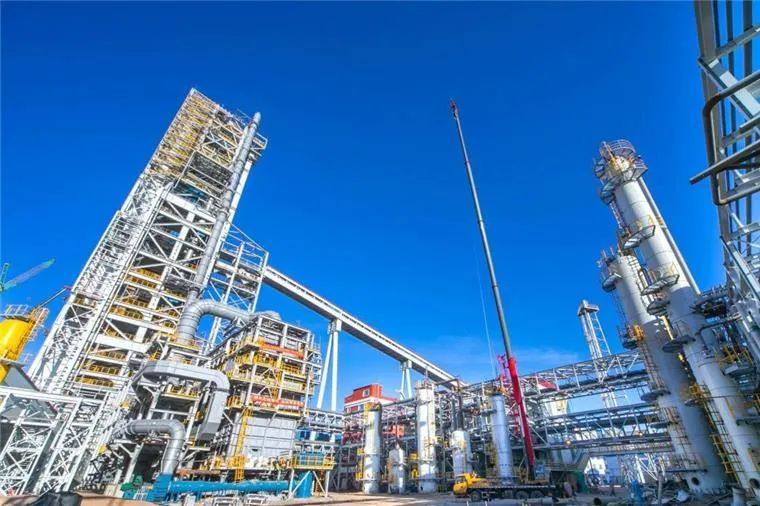
氢冶金技术

1
高炉富氢冶炼
高炉富氢冶炼即通过喷吹天然气、焦炉煤气等富氢气体参与炼铁的过程。相关实验表明,该工艺在一定程度上能够通过加快炉料还原,减少碳排放。但高炉富氢冶炼是基于传统的高炉,焦炭的骨架作用无法被完全替代,氢气喷吹量存在极限值,因此其碳减排幅度在10%-20%。

2
气基直接还原
气基直接还原是指使用氢气与一氧化碳混合气体作为还原剂,将铁矿石转化为直接还原铁,再将其投入电炉进行进一步冶炼。氢气作为还原剂的加入使碳排放得到了有效控制,相较于高炉富氢冶炼,气基直接还原工艺二氧化碳排放量可减少50%以上,碳减排潜力极大。
国内外发展现状
近年来,全球钢铁行业都在积极开展氢冶金实践。欧洲、日本、韩国等国家的钢铁企业均制定了包括氢能冶金在内的低碳冶金技术路线图,目前已有部分氢冶金技术的案例,例如瑞典HYBRIT项目、萨尔茨吉特SALCOS项目、德国蒂森克虏伯项目等。
目前我国已经研发出了比较完整的钢铁氢冶金系统。以河北省河钢集团的120万吨规模氢冶金示范工程为例。该项目是全球首次使用焦炉煤气“自重整”方式制氢,用获得的氢气直接还原含铁原料,生产出高品质的直接还原铁。
值得强调的一点是,制氢使用的焦炉煤气是钢铁企业生产过程中产生的副产,其本身就含有55%至65%的氢气成分,是非常合适的可以直接利用的氢能源,此外焦炉煤气中含量约15%的甲烷在经历高温转化后最终也会变成一氧化碳和氢气。
该新式氢冶金与配套的电路炼钢流程可以减少二氧化碳、氮氧化合物和烟粉尘排放达70%以上。相较同等生产规模的传统“炭冶金”方式,“氢冶金”技术每年可以减少约160万吨的二氧化碳排放。整个氢冶金过程,既回收利用了老式生产方式产生的副产品废气,也减少了整个冶金过程中的污染物排放,成功实现了传统“碳冶金”向新型“氢冶金”的颠覆性绿色低碳新转变。
氢冶金发展趋势
全球氢冶金项目研究主要分三步,2025年之前,建立中试示范项目验证大规模氢冶金的可行性;到2030年,利用副产氢气进行氢冶金工业化生产;到2050年,实现绿氢对灰氢的替代,进行绿色经济的氢冶金工业化生产。
从长远的发展来看,氢能与钢铁产业的合作是双赢的结果。氢能帮助钢铁企业节能减排、延伸业务、完成转型,钢铁企业为氢能提供了更多的落地应用,丰富氢能下游产业链,促进其发展。虽然目前由于环境和成本等各种因素,钢铁工业还没有实现“一氢到底”。但随着碳达峰、碳中和任务的迫近,钢铁工业逐渐从“减碳”过渡到“代碳”,氢冶金未来无限。
文章来源于网络
原文始发于微信公众号(万旗氢能):氢冶金技术促进钢铁工业绿色低碳发展
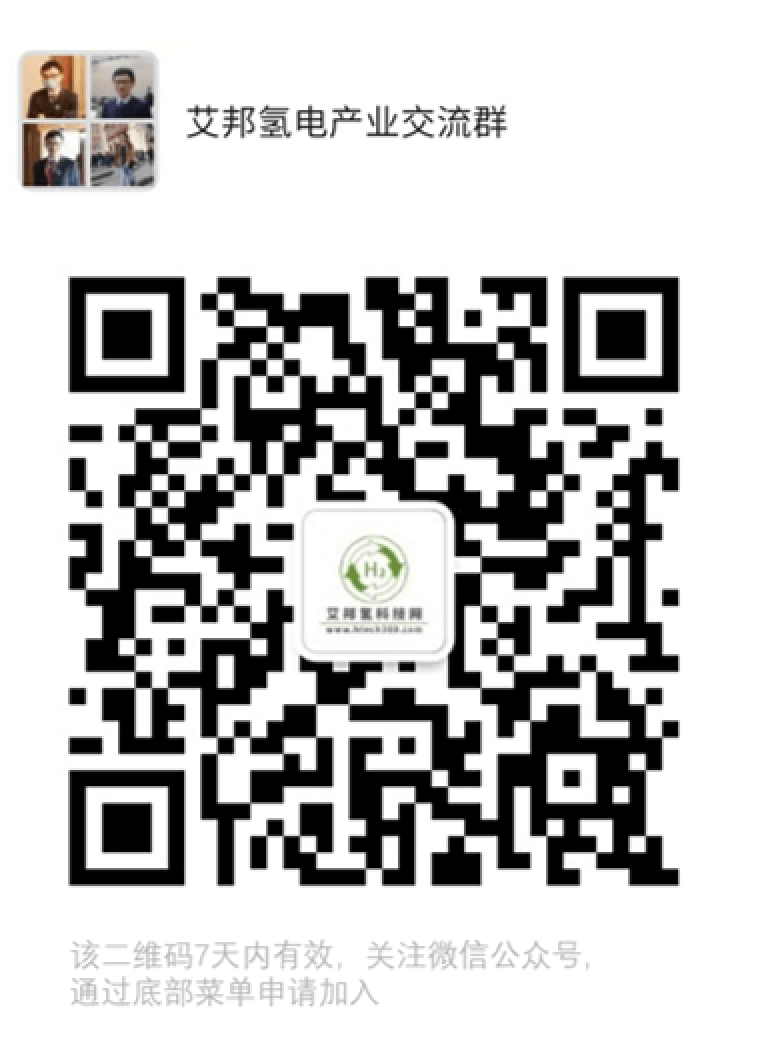