氢能作为一种零碳能源,具有来源丰富、洁净环保、燃烧值高、无污染、可储运等一系列优点,被誉为21世纪最具发展潜力的二次能源。氢能利用形式广泛,氢燃料电池汽车、燃料电池叉车、燃料电池电站、通讯基站应急备用电源等氢能利用典型产品已逐步推广,这对解决世界面临的能源和环境问题具有重要意义。
氢能利用完整链条包括生产、储存、运输、应用等几方面,而决定氢能是否广泛应用的关键是安全可靠的储氢技术。车载储氢技术主要包括高压气态储氢、低温液态储氢、固体储氢和有机液体储氢。其中,高压储氢因具有设备结构简单、压缩氧气制备能耗低、充装和排放速度快等优点而备受重视,是目前占绝对主导地位的氢能储输方式。
综合考虑压缩能耗、续驶里程、基础设施建设、安全等因素,高压储氧气瓶的公称工作压力一般为35-70MPa。高压储氧气瓶主要分为四个类型:全金属气瓶( Ⅰ型) 、金属内胆纤维环向缠绕气瓶( Ⅱ型) 、金属内胆纤维全缠绕气瓶( Ⅲ型) 、非金属内胆纤维全缠绕气瓶( Ⅳ型)。其中,Ⅰ型、Ⅱ型重容比大,难以满足氢燃料电池汽车的储氬密度要求。Ⅲ型、Ⅳ型瓶因采用了纤维全缠绕结构,具有重容比小、单位质量储氧密度高等优点,目前已广泛应用于氧燃料电池汽车。
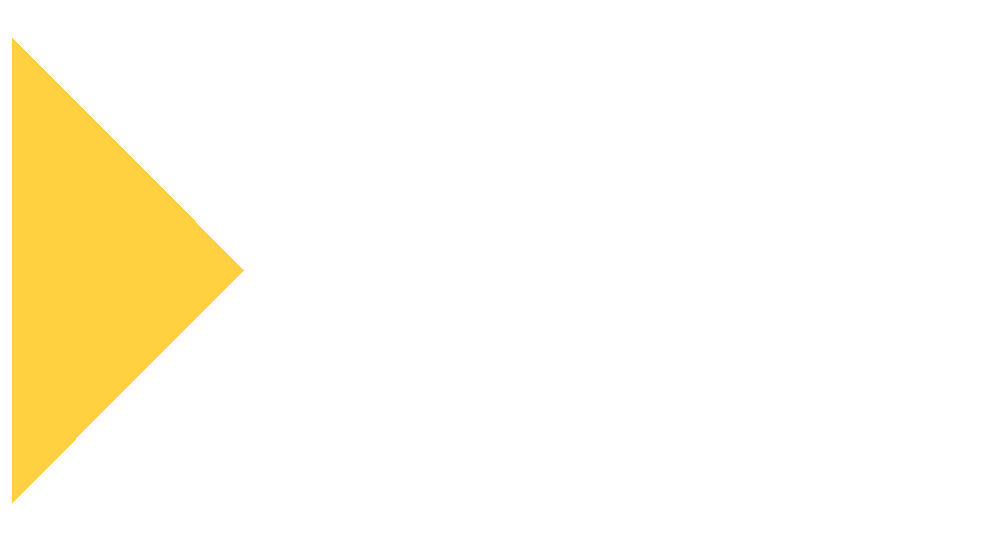
伴随氢燃料电池和电动汽车的迅速发展与产业化,氢储运的难题正成为全世界的研究热点。储氢瓶是其中极其重要的一种储运介质,下表列举了不同储氢瓶的各项性能对比。
伴随氢燃料电池和电动汽车的迅速发展与产业化,Ⅳ型储氢气瓶因其质量轻、耐疲劳等特点正成为全世界的研究热点,日本、韩国、美国与挪威等国的Ⅳ型储氢气瓶均已量产,其余国家也有相关计划加大Ⅳ型气瓶的研究力度。
IV型储氢瓶的制造成本在3000~3500美元,主要包括:复合材料、阀门、调节器、组装检查、氢气等,其中复合材料的成本占总成本的75%以上,而氢气本身的成本只占约0.5%。储氢瓶技术的发展趋势是轻量化、高压力、高储氢密度、长寿命,相比传统的金属材料,高分子复合材料可以在保持相同耐压等级的同时,减小储罐壁厚,提高容量和氢存储效率,降低长途运输过程中的能耗成本。因此,复合材料的性能和成本是IV型储氢气瓶制备的关键。
复合材料储氢气瓶由内至外包括内衬材料、过渡层、纤维缠绕层、外保护层、缓冲层。储氢气瓶进行充气的周期可能较长,而氢气在高压下又具有很强的渗透性,所以氢气储罐内衬材料要有良好的阻隔功能,以保证大部分的气体能够储存于容器中。
IV型储氢瓶的结构主要包括以下部分:
(1)内胆:瓶壁总厚度约为20~30mm,最内层与氢气直接接触的是阻气层,厚度约为2~3mm,材料是PA6、PA612、PA11、HDPE等,起阻隔氢气的作用;
(2)中间层:是比较厚的耐压层,材料是CFRP碳纤维增强复合材料,由碳纤维和环氧树脂构成,在保证耐压等级的前提下,尽量减小该层厚度以提高储氢效率;
(3)表层:最外层是表面保护层,厚度约为2~3mm,材料是GFRP玻纤增强复合材料,由玻璃纤维.1和环氧树脂构成。
塑料内胆的全复合材料气瓶( Ⅳ型瓶) ,采用高分子材料做内胆,碳纤维复合材料缠绕作为承力层,储氢质量比可达 6%以上,最高能达到7%,进而成本可以进一步降低。
内胆是储氢气瓶的核心部件,起到阻隔氢气的作用,其主要存在以下几个关键技术点:
(1)耐氢气渗透性和耐热性
氢气子极易透过塑料内胆的壳体材料,选材时必须考虑原材料的氢气阻隔性能。此外,氢气在经过阀门的节流作用后,气体温度会升高,随后气体被压缩到气瓶工作压力,温度同样升高,内胆原材料需具备合适的氢气渗透性和耐热性能。
PA6树脂在防止氢气渗透方面具有卓越的性能,并具有出色的机械性能,包括耐充填和排放氢气时储罐温度突然变化的耐久性以及低温环境下的抗冲击性。可通过对PA6材料渗透性进行了原材料级别的改性处理,并提高材料的软化温度至180°C左右,能满足使用要求。
(2)良好的低温力学性能
为了避免加注温度过高对内胆原材料造成损伤,通常将气源进行冷却,一般冷却至-40 ℃,当低温氢气充入气瓶内部,内胆在低温下将会变硬而脆,易破裂,内胆原材料的低温力学性能显得尤为重要。
(3)良好的工艺性
塑料内胆成型技术包括注塑成型、滚塑成型、吹塑成型等。目前丰田、现代等燃料电池汽车所采用的Ⅳ型储氢气瓶内胆成型工艺均为注塑工艺。注塑工艺是成本较低,运用也较为广泛的内胆成型方式,同时须配合后续的焊接工序,才能成型内胆。
在传统的铝内胆全缠绕气瓶强度设计中,一般不考虑内胆承载,理论上气瓶的内压完全由增强纤维承担。但事实上,气瓶内胆在工作压力下始终处于拉应力状态,这是制约气瓶疲劳寿命的关键。为同时满足储氢气瓶重量轻、耐疲劳性好的要求,选择合适的内胆形状与尺寸意义重大。
IV型瓶内胆多采用PA6、高密度聚乙烯(HDPE )以及PET聚酯塑料等,对应的成型工艺主要为注塑、吹塑和滚塑成型。丰田、现代已量产的IV型瓶均为注塑+焊接工艺,该种成型方式成本低、运用较广泛、但良品率也较低,且必须配合后续的焊接工序。
碳纤维储氢气瓶树脂基体不仅需要满足气瓶对力学强度和韧性的要求,同时由于在长期充气放气的使用环境中,基体容易发生疲劳损伤,因此需要高强韧、耐疲劳树脂体系以保障气瓶的使用寿命。湿法缠绕成型所用的树脂基体,除了要满足相应性能外,还要求其在工作温度下具有较低的初始粘度以及在该温度下具有较长的适用期。环氧树脂具有黏结强度高、固化收缩率小、无小分子挥发物、工艺成型性好、耐热性、化学稳定性好、成本低等优点,而且具有很大的改性空间,并且其来源广泛、价格合理,适用于湿法缠绕工艺体系。
IV型高压储氢气瓶复合材料层的树脂主要采用环氧树脂。环氧树脂是目前树脂基复合材料中常用的热固性树脂基体之一,具有黏结强度高、固化收缩率小、无小分子挥发物、工艺成型性好、耐热性、化学稳定性好、成本低等优点而广泛用于纤维缠绕工艺。
(1)良好的力学性能
树脂在复合材料中的作用是固定纤维,并通过树脂与纤维之间的界面传递载荷,使得纤维强度发挥至最大化。需要树脂具备较高的韧性和强度,但是两者是矛盾的,相互间的平衡是树脂改性关键技术难点。
(2)良好的热稳定性
对于Ⅳ型储氢气瓶,需要使得固化温度低于塑料内胆软化温度,而保护内胆结构。为了保证气瓶在实际使用过程中完全处于安全状态,就需要树脂玻璃化转变温度大于 105 ℃,一般而言,固化温度越低,固化后的玻璃化温度也就越低,这与保护塑料内胆结构稳定形成了矛盾体,需要对树脂进行相应的改性。
(3)良好的工艺性能
树脂适用期合适,黏度适中,是树脂工艺性的重要表现。车载储氢气瓶的复合材料层厚度一般在 20~30mm之间,缠绕时间较长,树脂适用期较短,会使得树脂浸润性变差,影响复合材料性能。固化炉的加热方式是通过空气对流,热辐射对气瓶进行加热,使其固化成型,黏度不合适,使得树脂较难排出气泡,且热量由表面向内部传递,内外存在温度梯度,固化后会在表面形成气泡,内部形成孔隙等缺陷,甚至严重影响产品性能。
丰田汽车公司发明了一种可以减少气瓶表面气泡的方法,用于气瓶的树脂分为两种,一种是与碳纤维形成缠绕层的第一树脂,另一种是与玻璃纤维形成保护层的第二树脂。第二树脂的凝胶温度比第一树脂凝胶温度高,在第一树脂凝胶温度下,第二树脂的黏度比第一树脂黏度低,因此,在碳纤维缠绕层固化过程中残留于树脂内部的气体从保护层向外排出,低黏度的树脂使得在固化前能够排出较多的气体,从而抑制气瓶表面气泡的残留,提高表面性状。
碳纤维缠绕成型工艺可分为湿法缠绕和干法缠绕,其中湿法缠绕由于其成本较低、工艺性好,因此应用较为广泛,湿法缠绕设备主要包括纤维架、张力控制设备、浸胶槽、吐丝嘴以及旋转芯模结构。国际上较先进的六维缠绕技术能够很好地控制纤维走向,实现环向缠绕、旋向缠绕以及平面缠绕相结合。实际生产中多采用旋向缠绕与环向缠绕相结合的方式,环向缠绕可消除气瓶受内压而产生的环向应力,旋向缠绕可提供纵向应力,提升气瓶整体性能。
纤维缠绕层的设计需要考虑纤维的各向异性,根据其结构要求,通常采用层板理论和网格理论来计算容器封头、内衬、纤维缠绕层的应力分布情况,进而确定缠绕工艺中张力选择与线型分布。通过环向缠绕与旋向缠绕交替进行实现多层次结构,选择适当纤维堆叠面积和纵向缠绕角度与旋向缠绕线型,不仅满足强度要求,同时使封头处能够合理铺覆。
干法缠绕工艺以经过预浸胶处理的预浸带为原料,在缠绕机上经加热软化至粘流态后缠绕到芯模上。其优点主要有:
(1)专业生产的预浸纱线/带,可以保证严格控制纤维和树脂(精确至2%以内)含量比例,产品质量好且稳定;
(2)生产效率高,缠绕速度可达100-200m/min;
(3)缠绕设备及生产环境卫生整洁,便于清理,缠绕机的使用寿命也更长。
(1)环向缠绕
环向缠绕是沿容器圆周方向进行的缠绕。缠绕时芯模绕自己轴线作匀速运动, 导丝头在平行于芯模轴线方向的筒身区间运动。芯模每转一周,导丝头移动距离为一个纱片宽。如此循环下去,直至纱片均匀布满芯模圆筒段表面为止。
环向缠绕的特点是缠绕只能在筒身段进行,不能缠到封头上去。邻近纱片间相接而不重叠,纤维的缠绕角通常在85°~90°之间。
(2)螺旋缠绕
螺旋缠绕也称测地线缠绕。缠绕时芯模绕自己轴线匀速转动,导丝头按特定速度沿芯模轴线方向往复运动,这样就在芯模的筒身和封头上实现了螺旋缠绕,其缠绕角约为12°~70°。在螺旋缠绕中,纤维缠绕不仅在筒身段进行,而且在封头上也进行。其缠绕过程为:纤维从容器一端的极孔圆周上某一点出发,沿着封头曲面上与极孔圆相切的曲线绕过封头,并按螺旋线轨迹绕过圆筒段,进入另一端封头,然后再返回到圆筒段,最后绕回到开始缠 绕的封头,如此循环下去,直至芯模表面均匀布满纤维为止。这样,当纤维均匀缠满芯模表面时,就构成了双层纤维层。为保证缠绕后的气瓶满足使用的压力要求,其缠绕方式一般选择环向缠绕和螺旋缠绕相结合的方式。
综上所述,IV型储氢瓶的生产制造流程如下图所示。可以看到高压氢瓶的生产过程主要包括:
(1)衬里加工(将热塑性烯烃聚合物制成内胆)
(2)纤维缠绕成型
(3)检查检验
用于高压下储存气体的压力容器和储罐的发展经历了四个不同的阶段,压力容器的第五个阶段—全复合材料的无内胆储罐(V型),是指不含任何内胆、完全采用复合材料加工而成的压力容器,长期以来V型压力容器一直被认为是压力容器行业产品和技术的制高点。
相比于IV型瓶的树脂衬里内胆、碳纤维强化树脂层的中间层以及玻璃纤维强化树脂层的表层三层结构,V型瓶是无内胆的两层结构,即碳纤维复合材料壳体及圆顶防护层。对比IV型瓶,V型瓶工作压力可达70-100MPa、无氢脆、无腐蚀性、使用寿命可达30年以上、成本中等等优点,亦可用于航天及车载领域。V型瓶的技术目前市场上尚在起步阶段,各行业都在密切关注V型瓶的技术的发展和机会。
芯模由水溶性芯材分两部分铸造、粘合制成,壁厚30毫米。内部有环形加强筋,有助于承受在纤维自动铺层过程中产生的扭转载荷和纤维固化过程中产生的压力。
预浸料精密切割成6.35mm宽的窄带,缠绕总共长度22,000米。缠绕过程使用专用软件控制螺旋和环形缠绕。缠绕24层、厚度达5.5mm
Ⅳ型储氢气瓶的研发除了需要与复合材料联系在一起,更需要与塑料加工制造工艺和塑料密封结构紧密地联系在一起。对我国而言,Ⅳ型气瓶相关技术仍处在一个不断发展、不断进取的阶段,需不断努力完善相应技术理论,为今后型气瓶的研发打下坚实基础。
1. 储氢瓶用碳纤维赛道:氢风已来,大有可为-国盛证券
2. 方鲲,刘康等,V型全复合材料耐高压气罐(瓶)的最新发展,2022
3. 蓑田愛,高圧水素用CFRP容器の開発,ENEOS Technical Review
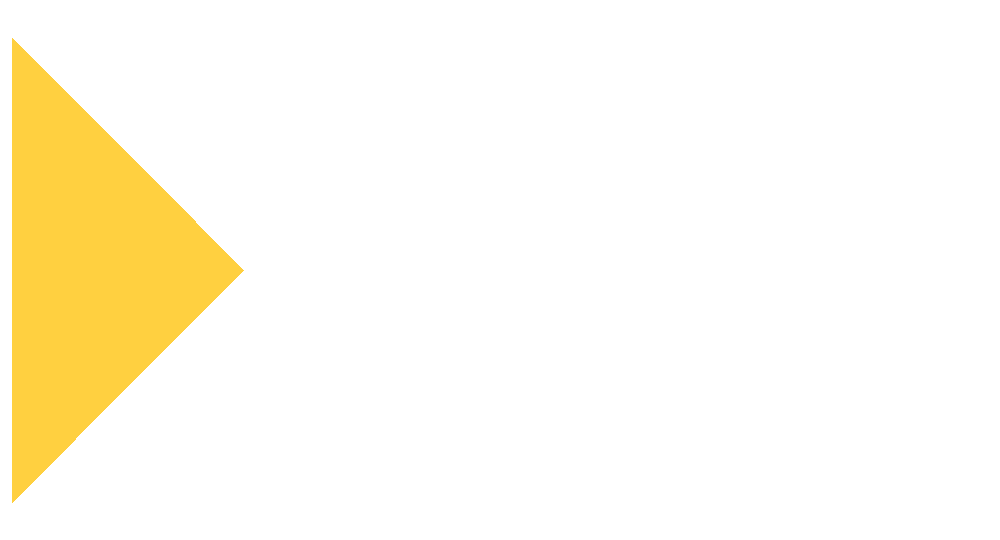
原文始发于微信公众号(氢能技术情报):高压储氢瓶的制造新工艺
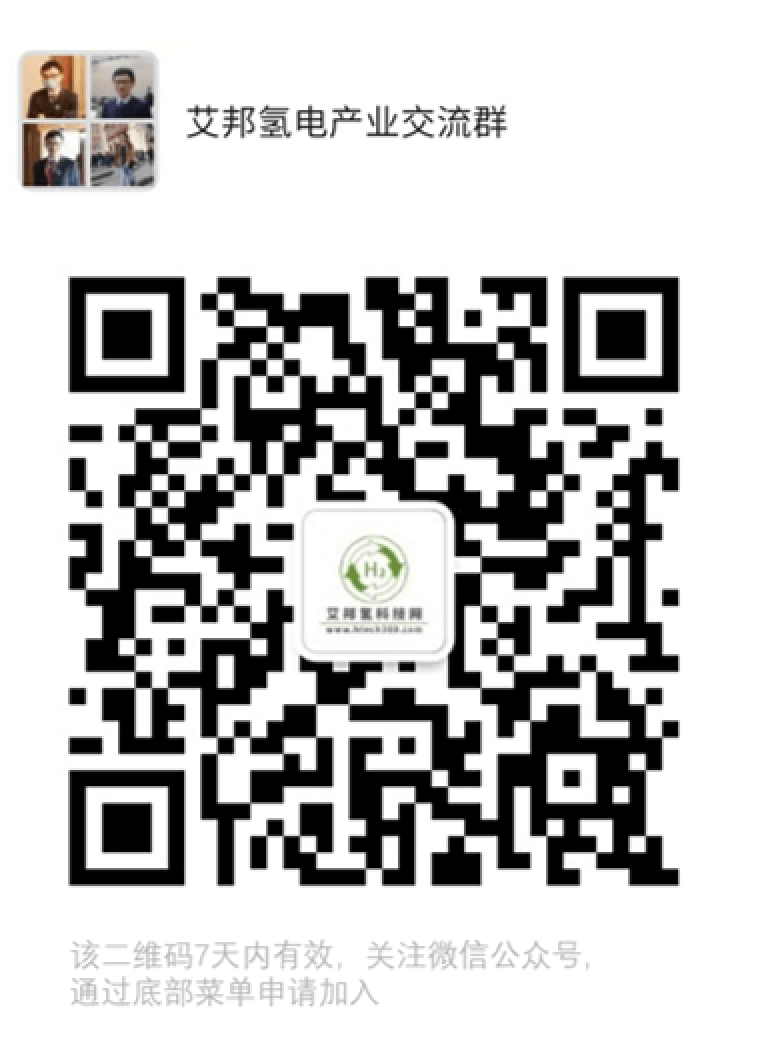